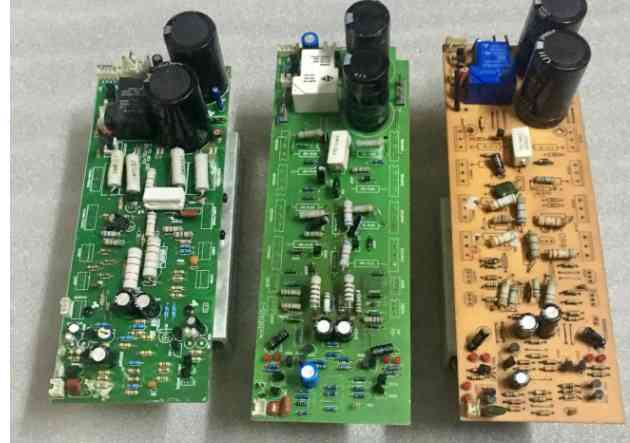
SMT machine is the most important equipment in SMT factory. The principle is to vacuum absorb components through the mounting head, and then mirror the movement of the center point of the identification component coincides with the PCBA coordinates, and finally release the mounting. This process includes the main technology of the whole SMT machine, such as automatic control technology, mechanical motion technology, visual detection and sensing technology, industrial computer and information processing technology, etc. We may rarely really understand the main technology of the SMT SMT machine in the ordinary working process, but whether the SMT SMT machine is advanced or not directly affects the production efficiency and quality of the whole SMT SMT factory, so the efficiency and quality of the production line depends on the speed and quality of the SMT machine. Next, Shenzhen patch processing plant -kingford- to share with you, I hope to bring you some help!
1. Industrial computer and information processing technology
Because the servo control is strict to the real-time requirements of the industrial computer system, at the same time, the chip machine equipment needs to have the ability of multi-task synchronous processing, such as online programming, multi-task interface and real-time work. Therefore, it is necessary to establish a real-time multitasking control model for SMT mounters, which runs on the real-time multitasking operating system and serves as the realization platform for SMT control. Information processing includes information access, exchange, operation, judgment and decision, etc. Computer is the main tool to realize information processing. Information processing technology and computer application are the most active factors to promote the development of SMT machine and electromechanical integration technology. SMT SMT machine control is completed by computer, generally adopt secondary computer control: each machine has its own set of control software, to achieve the control of mechanical structure movement; The master computer uses software to realize programming and man-machine interface. With the vigorous development of computer technology, windows operating system has completely replaced DOS, OS2 and other platforms, which makes the operation of the patch machine more visual and intelligent, the intelligent level of the patch machine has been greatly improved.
2. Mechanical motion technology of the SMT machine
In the SMT process, due to the high-speed operation of the SMT machine, combined with the precision of the mounting components, it is required to implement the high-speed and miniaturization of the parts. The requirements of the mechanical motion part of the SMT machine are as follows: 1. Design, manufacture and assembly technology of micro, precision and high precision mechanical parts; 2, sports machinery express response, low loss, high efficiency, precision positioning mechanism in line with transmission technology; 3, high precision, intelligent, high speed patch technology; The mounting head is an important operating structure of the mounting machine. In order to make the mounting machine run stably and meet the accuracy requirements, the mounting machine is usually driven by ball screw. At present, the guide rail of the SMT machine is generally integral or movable guide rail. The new SMT machine is developing from the traditional single way conveying to the multi-way conveying structure, and the mounting head is also developing to the single head multi-suction nozzle to the multi-suction nozzle.
3. Automatic control technology of SMT machine
The combination of automation control technology and computer control technology has become the most important technology in electromechanical integration equipment. Automatic control technology is the core of the whole SMT placing machine. As the installation efficiency of components is affected by the size of PCBA, the electronic components used and the type of feeder, etc., various factors should be taken into consideration when selecting the type of placing machine. In addition, program optimization should ensure the movement sequence and path of the mounting head in the actual production process. The total travel time of the entire circuit board is the shortest, so as to achieve the most efficient mounting efficiency. Due to the strict requirements on efficiency and precision of SMT mounters, PCBA components shall be mounted and positioned at high speed, and the positioning accuracy shall be maintained within 0.05mm. At the same time, the mounting strength of components also needs to be strictly controlled, so it should meet the requirements of speed, acceleration, vibration, impact and mounting strength. SMT mounters need to establish motion control models and intelligent control strategies to achieve high precision, high efficiency and high speed.
4. Visual detection technology of the patch machine
The research direction of vision detection and sensor technology of SMT machine is sensor and its signal detection device. It is of great significance to develop the research of vision detection and sensor technology for the development of electromechanical integration technology. Because machine vision is advanced in enhancing detectability and improving detection accuracy, so with the improvement of mechanical and electrical automation technology level, machine vision has been widely used in SMT components, SMT product quality detection and other fields. Today, almost all high precision SMT systems include a visual subsystem for positioning. These subsystems are used to detect and process the original position information of the target, obtain the feedback information needed by the computer, and provide accurate data for the precise component mounting. Visual inspection technology can grasp components for accurate positioning and calibration. Because electronic components now have higher and higher requirements for mounting accuracy, the new full-vision technology for surface mounting technology used in high-precision microelectronics equipment adopts high-precision and high-speed image processing and feature extraction methods. In addition, the visual technology can also recognize the image of the mounted IC, which can be used for component classification, waste disposal, etc., to improve the quality and efficiency of the mounted IC. Machine vision detection technology includes: 1. High speed image processing technology for patch; 2. 2. Machine vision high-speed recognition technology; 3, lighting technology, etc. The machine vision of some advanced SMT machines uses flight detection technology to realize positioning correction and defect detection of electronic components. The technology has the ability of real-time detection and positioning in the process of component picking, positioning and mounting, so that the SMT machine can achieve the purpose of improving the mounting efficiency under the condition of ensuring accuracy.
5. Sensor technology of the patch machine
Mounting equipment needs high reliable and high precision electromechanical detection and positioning technology. In order to make the mounting head of the SMT machine work together, the mounting head is installed with a variety of sensors, which are like the eyes of the SMT machine, monitoring the running state of the machine from time to time, and can effectively adjust the working state of the SMT machine. The more sensors are used, the higher the intelligent level of the SMT machine is predicted. The main types of sensors used in the SMT machine are position sensor, negative pressure sensor and pressure sensor. The position sensor is to monitor the limit position of various motion positions; The negative pressure sensor monitors the change of negative pressure. When the nozzle is not sucked or sucked, the negative pressure data is abnormal. The sensor feeds back the abnormal information to the computer, and the system can alarm in time. The pressure sensor is to allow the mounting head to adjust the mounting force when mounting components on the circuit board, so as to avoid excessive damage to PCB or too small mounting force.
2. How to choose automatic paste press?
In the whole production process of PCBA processing, the printing quality of solder paste is an important factor to determine the welding quality of PCBA. In order to obtain good printing quality of PCBA solder paste, it is necessary to rely on a press with perfect performance and high precision. There are many types and brands of printing presses on the market today, and each of them has different performance and parameters. So how should we choose the printer in PCBA processing? Next, I will share with you and hope to give you some help
First, the accuracy of fully automatic printing press
As electronic products become more and more integrated and fine, the pin of PCBA processing components also evolve more and more dense. Then the printing accuracy becomes particularly important when printing solder paste in PCBA, so the printing accuracy must be considered in the first place when selecting the printing press. At present, the printing accuracy of the selected printing press should be able to reach ±0.025mm, and the repeating accuracy should reach ±0.01mm, so as to effectively control the quality of solder paste printing. Moreover, the clamping device and upper pressing device of the printing press should be taken into account to ensure that the PCBA will not produce bending deformation when clamping and ensure the PCBA flatness.
Two, the efficiency of fully automatic printing press
The efficiency of the printing press is generally determined by the precision of the product. The more precise the product is, the slower the solder paste is. Most current press scrapers are adjustable in the range of 6-300mm/sec. When selecting the printing press, it is necessary to consider that the printing head is driven by two sets of stepper motors, and the pressure of the front and rear scrapers can be adjusted separately to ensure the inconsistency of the front and rear printing caused by the fatigue deformation of the scraper material, so as to effectively control the stroke and improve the printing efficiency. Automatic solder paste printing machine is suitable for different thickness of PCB height manual adjustment platform, to ensure the best contact between PCB and steel mesh, automatic control can improve production efficiency, control quality, save cost, automatic PCB correction, scraper pressure adjustable, automatic printing.
Three, automatic printing press stability
Because the equipment is used for a long time and with high frequency, many aspects of support are needed to ensure the printing quality. Stability is a very important aspect, that is, the repetition accuracy of solder paste printing as we said before can reach ±0.01mm. The new stable solder paste press can ensure the quality of the whole PCBA processing more stably.
Four, automatic printing press image recognition performance
When choosing a fully automatic solder paste press, the first thing to pay attention to is the printing accuracy and the performance of printing itself. For example, there are no defects in image recognition, whether the way of image recognition is reasonable, especially the image recognition of positioning system, because this is the key to measure the precision of a fully automatic solder paste printing press. In addition, it is also necessary to see how the system self-positioning repair function, whether it can carry out simple fault diagnosis and repair. If the equipment can have a certain self-positioning repair function, then it can effectively avoid many problems in the use of the machine.
Finally, kingford would like to tell you that we want to buy a cost-effective fully automatic solder paste press, with special attention to the performance of the equipment in specific use. If conditions permit, they can conduct field research before purchasing, or even ask the equipment manufacturer to take it to the PCBA factory that purchased the same type of printer to see the production situation directly. Equipment warranty is also very critical, good after-sales service of equipment suppliers, will be more conducive to the use and maintenance of the machine. The above content is shared by One Nine Four Two Technology for you to learn more about PCBA processing knowledge, Shenzhen kingford Co., Ltd. is a professional PCBA processing plant integrating PCB design and manufacture, component purchase, PCBA processing, SMT SMT processing, PCBA one-stop service. For many years, we focus on high-quality PCBA processing, production and technical services. Fully able to meet the needs of all kinds of customers. It is your trusted PCBA processing plant