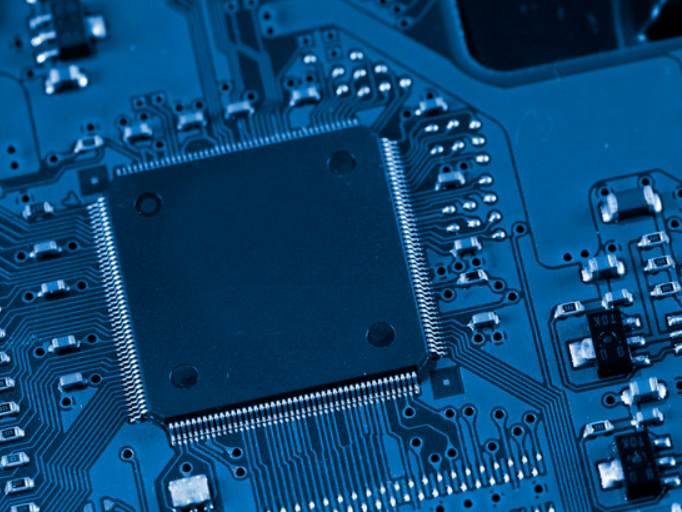
PCB production etching process is divided into: stripping film, line etching, stripping tin (lead). Here is a detailed introduction to the three processes:
Peeling membrane
In PCB board production, only two steps will use film stripping. D/F stripping after etching of the inner line and D/F stripping before etching of the outer line (if the outer line is made into a negative film process). The stripping process of D/F is simple, all are wired horizontal equipment, the use of chemical liquid concentration weight ratio of 1~3%NaOH or KOH.
Line etching
1. Copper erosion mechanism
(1) Copper ions are easy to form copper hydroxide precipitation in alkaline environment solution, in order to prevent the occurrence of such precipitation phenomenon, it is necessary to add enough ammonia water to produce wrong ion groups of ammonia copper to inhibit the occurrence of precipitation. It can also make the original amount of copper and continue to dissolve copper in the liquid to form a very stable ammonia copper ion. Such divalent ammo-cuprous ions can also be used as oxidants to dissolve zero-valent copper metal by oxidation, but in the process of REDOX reaction will produce cuprous ions.
In this reaction, the solubility of cupric ions is very poor, and it needs to be assisted by ammonia, ammonia ions and a large amount of oxygen in the air to make it continue to oxidize into soluble bivalent cupric ions, and then become the oxidant of copper corrosion and continue to corrode copper until the amount of copper is too much and slowed down. Therefore, in addition to eliminating ammonia odor, the etching machine can supply fresh air to accelerate copper corrosion.
(2) In order to make the above-mentioned copper erosion reaction more rapid, the corrosion solution is supplemented with additives, such as:
accelerator can promote the above oxidation reaction faster and prevent the precipitation of cuprous ions.
Banking agent reduces side erosion.
Suppressor inhibits ammonia flight at high temperature and suppressor inhibits copper precipitation to accelerate copper oxidation.
2. Equipment
(1) In order to increase the corrosion rate, it is necessary to increase the temperature to more than 48℃, so there will be a large number of ammonia odor diffuse need to do appropriate pumping, but when the pumping air volume is too strong, useful ammonia will also be a large amount of waste, can be added in the air pumping pipe appropriate throttle valve to do control.
(2) etching quality is often limited by pool effect (pudding), (because fresh liquid medicine is blocked by water, can not effectively react with copper surface called pool effect) This is why PCB board front-end part is often over etch phenomenon, so the equipment design needs to consider the following points:
PCB board thinner line face down, thicker line face up.
The pressure of the nozzle is adjusted as compensation, and the difference is adjusted according to the actual operation results.
Advanced etchers can control the number of seconds when the circuit board enters the etching section and the previous sets of nozzles stop spraying.
Vertical etching is designed to solve the problem of uneven two sides, but it is less used in China.
3. Add add control
The supplemental liquid is ammonia, usually with a very sensitive hydrometer, and the temperature at that time (due to the difference in specific gravity at different temperatures), set the upper and lower limits, higher than the upper limit, start to add ammonia, until below the lower limit. At this time, the location of the detection point and the location of the inlet where ammonia water is added are very important to avoid the waste cost of adding too much ammonia water due to the detection delay (because it will overflow).
4. Daily maintenance of equipment
(1) sludge should not be allowed to sludge the etching liquid (light blue monovalent copper sludge), so it is very important to control the composition, especially if the PH is too high or too low, it may cause.
(2) Keep the nozzle from being blocked at any time. (The filtration system should be kept in good condition)
(3) the specific gravity induction adding system should be checked regularly.
Stripping tin (lead)
This step of stripping tin (lead) is purely for processing, without any added value, but in order to ensure the quality of products, we still need to pay attention to the following points:
(1) The solution of stripping tin (lead) is usually provided by suppliers in two-liquid or single-liquid type. The stripping methods include semi-soluble type and total soluble type, and the solution composition formula includes fluorine /H2O2, HNO3/H2O2, etc.
(2) No matter what kind of formula, there may be the following potential problems in operation:
Attack copper surface;
After stripping the incomplete impact process;
Waste liquid disposal problem.
In order to ensure the quality and stability of PCB products, tin stripping (lead) requires good equipment design, tin plating (lead) thickness control in the pre-production process and the management of drug liquid effects. How can you tell if the etching is good or bad? Mainly through the following points of basis:
1. Sharp edges.
2. Lateral erosion.
3. Etching coefficient factor.
4. Overcorrosion.
5. Etched surface finish.
6. Check whether the spacing between cables is clear.