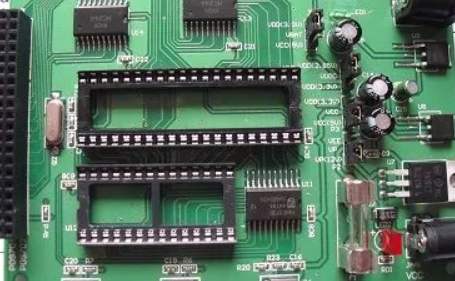
Shenzhen kingford has its own SMT plant, which can provide SMT SMT processing services of 0201 components with minimum package, supporting incoming material and sample processing and PCBA OEM. Next, we will introduce how to select SMT patch inductance.
How to select SMT chip inductor?
Inductance is a common electronic component in SMT patch. The inductance of SMT patch is also called power inductance, high current inductance and surface mounted high power inductance. It is one of the basic electronic components of SMT patch processing, having the characteristics of miniaturization, high quality, high energy storage and low resistance
Inductance is the ratio of the magnetic flux of the wire to the current that produces the alternating flux in and around the wire when an alternating current is passed through the wire. So how should we choose the inductance of smt patch during SMT patch processing?
1. The total width of the inductance of the patch should be lower than the total width of the inductance, so as to avoid the change of the inductor value caused by excessive tensile stress caused by excessive welding materials during water cooling.
2. The precision of the patch inductor that can be purchased on the market is mostly ±10%. If the precision is higher than ±5%, it must be ordered in advance.
3. Some patch inductors can be welded by reflow furnace and wave soldering, but some patch inductors can not be welded by wave soldering.
4, maintenance, can not be replaced by a single inductor quantity into the patch inductor. In order to ensure operating characteristics, it is also necessary to know the operating frequency segment of the patch inductor.
5. The appearance design and specifications of the chip inductor are similar, and the appearance design has no significant logo. When welding or making patches by hand, you must be very careful not to take the wrong part or the wrong part.
6. At the present stage, there are three kinds of common chip inductors: the first kind, microwave heating with high frequency inductors. Suitable for applications in the frequency band of about 1GHz. Second, high frequency patch inductors. Suitable for series resonance control circuit and frequency selection power supply circuit. Third, practical inductors. Generally applicable to dozens of MHZ power supply circuit.
7, different commodities using magnetic diameter is different, even if the use of the same amount of inductor, the resistance measurement is not the same. In the high frequency control loop, the resistance measurement does great harm to Q value, so we should pay attention to the design scheme.
8. The tolerance is an index value of the patch inductance according to the larger current flow. When the power supply circuit must bear a large current basis, this index value of the capacitor must be taken into account.
9. When the power inductor is used in the DC/DC converter, the size of the inductor immediately endangers the working attitude of the power circuit. Combined with the actual situation, the inductor quantity can be changed by adjusting the magnetic coil to achieve the best practical effect.
10. Winding inductors are common in communication equipment working in the frequency range of 150~900MHz. In the frequency power supply circuit of about 1GHz, microwave heating high frequency inductor must be used.
2. Why add test points to circuit board design?
kingford is a professional PCB design company with many years of work experience PCB design team, can provide multi-layer, high density, high speed PCB routing design and PCB design proofing services. Next, why add test points to circuit board design?
Why add test points to circuit board design?
The PCB design and test point is not needed in the production of PCB board, but after the completion of PCBA, the ICT test is carried out to test whether there is any problem in the welding of the circuit board and whether the performance meets the requirements.
In PCB production, the circuit board also needs to be tested to see whether the circuit is open, short circuit phenomenon. This works as a needle bed, testing against each network point.
The light PCB is fine, but the PCBA is fine, it is different, the components are soldered. Especially SMT components, if you use a needle bed, the needle poke SMT components is easy to damage, then how to do? It is necessary to add test points on each line network for the needle bed to be connected. In this way, the needle bed will not damage the SMT element, and the needle bed will be pressed to the flat test point. The test will be more accurate. In the early years, it was stipulated that 90% of the network should add test points.
Some disadvantages of testing with a needle bed are unavoidable. There is a limit to the size of the needles and the minimum spacing between them. It can be a little difficult for high-density boards.
There are so many test points, for the high-density circuit board space, is really stretched, certainly is not realistic. Now, there are a lot of tests that don't include test points, but there are other ways to test. Such as JTAG test, X-REY test, AOI test. However, these tests are not a 100% replacement for ICT testing in some places.
Why do you choose kingford for SMT processing?
1. Strength guarantee
▪SMT workshop: We have imported SMT machines and several sets of optical inspection equipment, with a daily output of 4 million. Each process is equipped with QC personnel, who can keep an eye on product quality.
▪DIP production line: We have two wave-soldering machines, among which there are more than 10 old employees who have worked for more than three years. The skilled workers can weld all kinds of plug-in materials.
2. Quality assurance, cost-effective
▪ High-end equipment can stick precision shaped parts, BGA, QFN, 0201 materials. Can also template patch, loose material hand.
▪ Sample and size batch can be produced, proofing from 800 yuan, batch 0.008 yuan/point, no start-up fee.
3. Rich experience in SMT and welding of electronic products, stable delivery
▪ Accumulated SMT SMT processing services for thousands of electronic enterprises, involving many kinds of automotive equipment and industrial control motherboard. The products are often exported to Europe and the United States, and the quality can be affirmed by new and old customers.
▪ On time delivery, normal 3-5 days after complete materials, small batch can also be expedited on the same day shipment.
4. Strong maintenance ability and perfect after-sales service
▪ Experienced maintenance engineers can repair all kinds of patch welding caused by bad products, to ensure the connection rate of each piece of circuit board.
▪ 24-hour customer service staff at any time response, the fastest speed to solve your order problems.