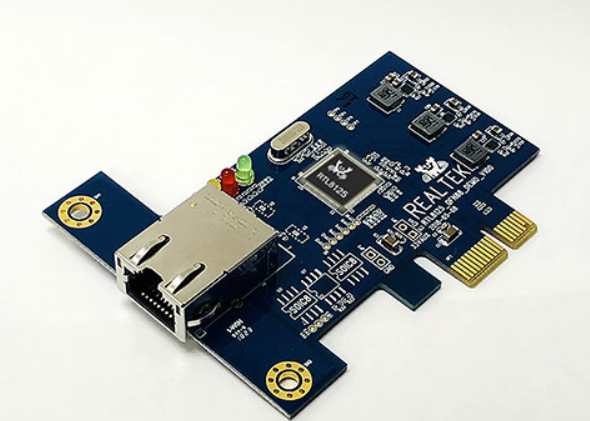
PCBA processing soldering soldering is in the wave soldering process, welding solder material after preheating through the wave peak will lift the solder liquid to a certain height, forming a tin wave, placed above the tin wave need to be welded, so that the solder liquid can wet and coating the solder joint surface, forming a welding joint process. In this process, the solder liquid is applied to the surface of the element's solder joint to moisten and fill the weld, thus forming a welded joint.
PCBA processing soldering soldering soldering reasons may include the following aspects:
1. Performance of solder alloy: Solder alloy needs to have good wettability and fluidity, so that the solder liquid can wet and fill the weld in the welding process, so as to form a complete welded joint.
2. Crest height and period: the selection of crest height and period also has a great impact on welding quality. The reasonable matching of peak height and period can make the time and degree of solder liquid wetting element solder spot surface reach the best state, so as to form a good welding joint.
3. Component solder joint design: component solder joint design will also affect the quality of the welded joint. Reasonable design of solder joint can increase the contact area of welded joint, improve the welding strength and stability.
4. Welding process parameters: the selection and adjustment of welding process parameters will also affect the quality of welded joints. For example, the adjustment of welding temperature, welding speed, crest height and period can make the welding joint achieve the best wetting and filling effect.
Solve the method of PCBA processing wave soldering tin
In the process of PCBA wave soldering, if tin connection occurs, corresponding measures should be taken to deal with it. Common methods are as follows:
1. Adjust welding process parameters: properly adjust welding process parameters, such as welding temperature, crest height, period, etc., in order to reduce the wetting time and degree of welding, to prevent the formation of solder on the solder joints of components.
2. Replace the solder alloy: try to replace other solder alloys with better wettability and fluidity, in order to make the welding process more stable and reduce the possibility of tin.
3. Replace components: Some components themselves have poor wettability, easy to appear tin phenomenon, you can consider replacing other components with good welding performance.
4. Check the surface treatment of PCB board and components: improper surface treatment of PCB board and components is also easy to lead to the occurrence of tin phenomenon, you can check whether there is oil pollution, oxidation and other problems, timely cleaning and treatment of the surface.
5. Check the equipment: check whether there is a fault in wave soldering equipment, such as unstable solder groove temperature, inconsistent crest height and other problems, timely maintenance or replacement of equipment.
In a word, tin connection is a common problem in the process of PCBA wave soldering, which needs to be adjusted according to the actual situation.
2.PCBA processing manual welding skills
Manual welding is often used in SMT processing factories. In order to make the welding of objects better, we must master the technical essentials of welding. Then how to quickly master the technical essentials of manual welding? Next, Shenzhen PCBA processing manufacturer -kingford to introduce PCBA processing manual welding skills.
PCBA machining manual welding skills
The main tool for manual welding is the electric iron. There are many kinds of electric iron. According to the heating method, it can be divided into direct heat type, induction type, constant temperature electric iron, intelligent electric iron, tin suction pump, hot air welding platform, electric heating clip, etc. Manual welding should first choose anti-static constant temperature electric soldering iron.
1. Welding operation posture
(1) Welding distance
The gas produced in welding will cause harm to the human body, so when using the electric iron, the distance between the nose and the electric iron should be more than 30cm, and 40cm is a more appropriate distance.
(2) electric soldering iron grip method
The electric iron has reverse grip, is holding and holding the pen three grip, the reverse grip is stable, long time operation is not easy to fatigue, suitable for high power electric iron grip, is suitable for medium power electric iron or with elbow electric iron operation, the pen holding method is generally used in welding components and maintenance circuit board.
2. Five-step welding method
(1) Prepare for welding -- clean soldering iron: add tin to the iron head, clean the iron head, which is conducive to heat conduction; Do not use a knife or anything else to scrape the oxide layer of the iron head.
(2) Heating welds: put the soldering iron head on the connection point of the welded metal (the place with the largest heat capacity); Heat begins to flow to the surface of the metal being welded.
(3) solder wetting: the tin wire is placed between the connection point of the soldering iron head and the metal to be welded, forming a thermal bridge; Flux flows in the cold direction, infiltrating the pad -- from the soldering tip to the whole pad, removing the oxide layer and promoting heat conduction; When the solder wire is moved to the opposite side of the heat source, the molten tin flows in the direction of heat, wets the pad and pin, and capillary phenomenon, diffusion, dissolution and metallurgical combination occur at the interface; Push the flux residue toward the surface and edge of the solder joint.
(4) Evacuation of the tin wire: first evacuate the tin wire, after the evacuation of the iron, otherwise the tin wire will solidified on the solder joint.
(5) Stop heating: cooling, solidification, forming solder joints; Note that when the tin wire is not fully solidified, do not shake the components and pcb to avoid virtual welding.
Shenzhen kingford Co., Ltd. specializes in providing integrated PCBA electronic manufacturing services, including upstream electronic components procurement to PCB production and processing, SMT patches, DIP plug-ins, PCBA testing, finished product assembly and other one-stop services.