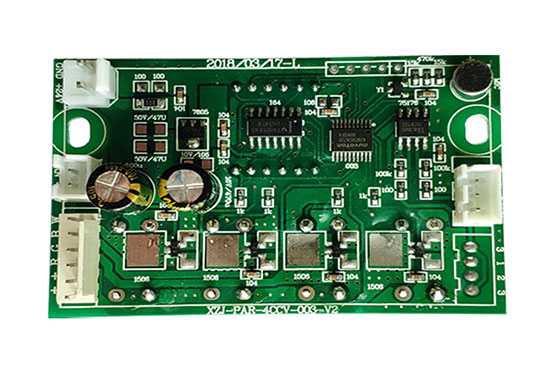
SMT processing is a process with many interactive links and processes, so a small mistake may cause a big impact. So what links will affect the quality of SMT processing? What do we need to pay attention to in the SMT process? Next, Shenzhen SMT patch processing manufacturer -kingford for you to introduce.
Factors affecting SMT machining quality
I. Equipment
The technological complexity of intelligent products has far exceeded our manual processing and welding degree, can only rely on machines and equipment for patch welding, testing and so on. Therefore, the equipment is the necessary means of SMT mass refined production. Such as whether the patch programming is well thought out.
Ii. Process
Hardware equipment in the market as long as the money can be bought, but it also needs someone to operate, and finally to realize the implementation of the process, so the equipment is only the means of the implementation of the process, the process is the real core. The difference of process will directly lead to the utilization rate of equipment, through rate, yield rate.
Three, PCB circuit board
The circuit board is the substrate of the whole SMT welding and the starting point of everything. The quality of the pad and the reasonable design of PCB are also important factors affecting the SMT process.
Four, steel mesh (template)
Half of SMT quality problems occur in solder paste printing. The setting of steel mesh thickness and window opening design are the key factors that directly affect the quality of SMT processing.
Five, the setting of furnace temperature curve
When PCB, components, solder paste printing, screen are completely OK, a furnace temperature curve according to product characteristics to accurately set becomes the last step of good product clearance.
Money can buy equipment, production lines and staff, but some process accumulation and technology precipitation often need to spend a long time to accumulate, form their own process specifications, improve their own process system, and finally form a summary of experience is the cornerstone of an enterprise quality.
2.PCBA manufacturer shall analyze SMT patch processing and repair process
In the production process of SMT patch processing, there will occasionally be some processing defects or undesirable phenomena that we do not want to see. For defective PCBA products, we cannot let them flow into the next processing link or even leave the factory. Next, kingford, PCBA manufacturer, will introduce SMT patch processing and repair process to you.
SMT patch processing and repair trilogy
1. PCBA welding and disassembly
1. Remove the PCBA coating layer first, and then remove the residue on the working surface.
2. Install the hot clip iron head with appropriate shape and size in the hot clip tool.
3, the temperature of the iron head is set at about 300℃, which can be changed appropriately according to needs.
4. Apply flux to the two solder joints of the chip element.
5. Remove oxides and residues on the tip of the iron with a wet sponge.
6. Place the soldering iron head above the SMT patch element, and clamp both ends of the element to contact the solder joint.
7. Lift the element when the solder joints at both ends are completely melted.
8. Place the removed component in a heat-resistant container.
Two, PCBA welding pad cleaning
1, the selection of chisel-shaped iron head, the temperature is set at about 300℃, can be appropriate to change according to the need.
2. Brush flux on the welding pad of the circuit board.
3. Remove oxides and residues on the tip of the iron with a wet sponge.
4. Put the soft tin-absorbing braided tape with good weldability on the pad.
5. Gently press the soldering iron head on the tin absorbing braid belt. When the solder on the pad is melted, slowly move the soldering iron head and braid belt to remove the residual solder on the pad.
3. PCBA assembly and welding
1, choose the right shape and size of the iron head.
2, the temperature of the iron head is set at about 280 ℃, which can be changed appropriately according to needs.
3. Brush the flux on the two pads of the circuit board.
4. Remove oxides and residues on the tip of the iron with a wet sponge.
5. Apply an appropriate amount of solder to a pad with an electric soldering iron.
6. Clamp the SMT patch element with insert, and connect one end of the element with the solder plate that has been tinned with electric iron to fix the element.
7. Weld the other end of the component with the pad with the electric iron and the soldering wire.
8. Weld both ends of the components and the pad respectively.
Shenzhen kingfordSMT processing capacity
1. Maximum board card: 310mm*410mm(SMT);
2. Maximum plate thickness: 3mm;
3. Minimum plate thickness: 0.5mm;
4. Minimum Chip parts: 0201 package or parts above 0.6mm*0.3mm;
5. Maximum weight of mounted parts: 150g;
6. Maximum parts height: 25mm;
7. Maximum parts size: 150mm*150mm;
8. Minimum spacing of pin parts: 0.3mm;
9. Minimum ball parts (BGA) spacing: 0.3mm;
10. Minimum ball parts (BGA) ball diameter: 0.3mm;
11. Maximum parts mounting accuracy (100QFP) : 25um@IPC;
12. Patch capacity: 3-4 million points/day.
Shenzhen kingfordSMT processing advantages
1. Strength guarantee
▪SMT workshop: We have imported SMT machines and several sets of optical inspection equipment, with a daily output of 4 million. Each process is equipped with QC personnel, who can keep an eye on product quality.
▪DIP production line: We have two wave-soldering machines, among which there are more than 10 old employees who have worked for more than three years. The skilled workers can weld all kinds of plug-in materials.
2. Quality assurance, cost-effective
▪ High-end equipment can stick precision shaped parts, BGA, QFN, 0201 materials. Can also template patch, loose material hand.
▪ Sample and size batch can be produced, proofing from 800 yuan, batch 0.008 yuan/point, no start-up fee.
3. Rich experience in SMT and welding of electronic products, stable delivery
▪ Accumulated SMT SMT processing services for thousands of electronic enterprises, involving many kinds of automotive equipment and industrial control motherboard. The products are often exported to Europe and the United States, and the quality can be affirmed by new and old customers.
▪ On time delivery, normal 3-5 days after complete materials, small batch can also be expedited on the same day shipment.
4. Strong maintenance ability and perfect after-sales service
▪ Experienced maintenance engineers can repair all kinds of patch welding caused by bad products, to ensure the connection rate of each piece of circuit board.
▪ 24-hour customer service staff at any time response, the fastest speed to solve your order problems.