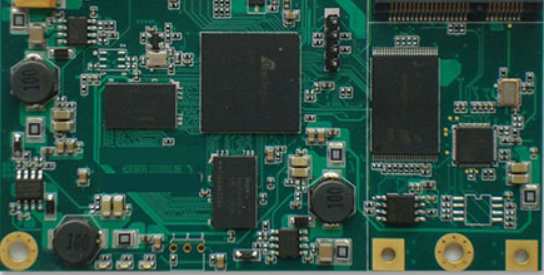
Not for nothing does today's mass-produced electronic hardware use the well-known surface mount technique or SMT manufacturing! SMT Surface Mount Technology plays an important role in speeding up PCBA processing speed. Next, Shenzhen SMT processing plant -kingford to introduce the advantages of SMT surface mounting technology.
Advantages of SMT surface mount technology
In essence, Surface Mount technology (SMT) takes the basic concept of through-hole manufacturing and continues to make significant improvements. When using SMT, the PCB does not need drilling. Instead, what they're going to do is use solder paste. In addition to increasing speed, this significantly simplifies the process. Although it is true that SMT mount-mounted components do not have the strength of through-hole mount-mounted components, they offer many other advantages that offset this problem.
SMT surface mounting technology goes through the following 5 steps:
1. PCB production - This is the actual production stage of PCB with solder points;
2. Deposit solder on the pad to fix the assembly to the plate;
3. With the help of the machine, the components are placed on the precise solder joint;
4. Bake PCB to harden flux;
5. Check the completed components.
The reasons that make SMT different from through hole include:
By using surface mount technology, the space problem widely encountered in through-hole installation can be solved. SMT also provides design flexibility because it gives PCB designers free control to create dedicated circuits. The reduced component size means that more components can fit on a board and fewer boards are needed.
Components in SMT mounting are lead-free. The lead length of surface-mounted components is shorter, reducing propagation delay and packaging noise.
The density of components per unit area is higher because it allows components to be mounted on both sides.
It is suitable for mass production, thus reducing costs.
The reduction in size results in an increase in circuit speed. In fact, this is one of the main reasons most manufacturers choose this approach.
The surface tension of the molten solder pulls the assembly into alignment with the pad. In turn, this automatically corrects any minor errors that may occur in component placement.
SMT has proved to be more stable in conditions where there is a lot of vibration or shaking.
SMT parts are usually cheaper than similar through hole parts.
Importantly, SMT can greatly reduce production time because drilling is not required. Moreover, SMT components can be placed in the thousands per hour, compared to less than a thousand for through-hole installations. In turn, this results in the product being produced at the desired rate, which further reduces time-to-market. So if you want to speed up PCBA processing times, SMT is the answer. By using manufacturing Design (DFM) software tools, the need to rework and redesign complex circuits can be greatly reduced, further increasing the speed and possibilities of complex design.
All this does not mean that SMT is without its own inherent drawbacks. SMT may not be reliable if it is used as the only fastening method for components facing a large amount of mechanical stress. Components that generate a lot of heat or withstand a high electrical load cannot be installed using SMT patches. This is because solder melts at high temperatures. Therefore, in cases where there are special mechanical, electrical and thermal factors that prevent SMT from working, it is likely that through-hole installation will continue. Similarly, SMT is not suitable for prototyping, as components may need to be added or replaced during the prototyping phase, and high-density boards may be difficult to support.
Choose Shenzhen kngford do PCBA processing four reasons
1. Strength guarantee
▪SMT workshop: We have imported SMT machines and several sets of optical inspection equipment, with a daily output of 4 million. Each process is equipped with QC personnel, who can keep an eye on product quality.
▪DIP production line: We have two wave-soldering machines, among which there are more than 10 old employees who have worked for more than three years. The skilled workers can weld all kinds of plug-in materials.
2. Quality assurance, cost-effective
▪ High-end equipment can stick precision shaped parts, BGA, QFN, 0201 materials. Can also template patch, loose material hand.
▪ Sample and size batch can be produced, proofing from 800 yuan, batch 0.008 yuan/point, no start-up fee.
3. Rich experience in SMT and welding of electronic products, stable delivery
▪ Accumulated SMT SMT processing services for thousands of electronic enterprises, involving many kinds of automotive equipment and industrial control motherboard. The products are often exported to Europe and the United States, and the quality can be affirmed by new and old customers.
▪ On time delivery, normal 3-5 days after complete materials, small batch can also be expedited on the same day shipment.
4. Strong maintenance ability and perfect after-sales service
▪ Experienced maintenance engineers can repair all kinds of patch welding caused by bad products, to ensure the connection rate of each piece of circuit board.
▪ 24-hour customer service staff at any time response, the fastest speed to solve your order problems.