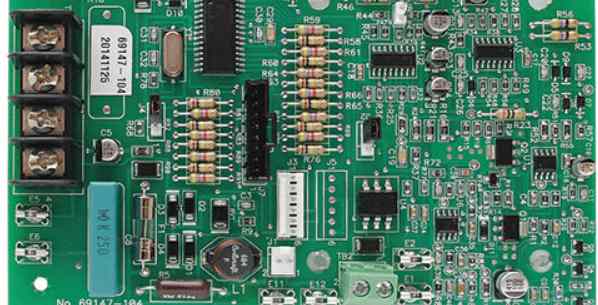
For a newly designed PCB board, it is often difficult to debug, especially when the board is large and there are many components, it is often difficult to get started. If we master a set of reasonable fault finding methods, debugging will get twice the result with half the effort. So, what are the new PCB fault finding methods? Next, Shenzhen PCBA processing manufacturer -kingford for you to introduce.
New design PCB board to find fault method
1. Measuring voltage method
First, confirm whether the power supply pin voltage of each chip is normal, and then check whether various reference voltages are normal, including whether the working voltage of each point is normal.
2. Signal injection method
Add the signal source to the input terminal, and then measure the waveform of each point in turn to see if it is normal, so as to find the fault point. Sometimes simpler methods can be used, such as touching each level of input terminal with tweezers to see if the output terminal responds. This is often used in audio, video and other amplifier circuits; However, it is important to note that this method should not be used on circuits with hot backboards or high voltage, or you may get electric shock. If there is no reaction at the upper level, but there is a reaction at the lower level, the problem is at the upper level, focus on inspection.
3. Look, hear, smell and touch
"Look" refers to whether the parts have obvious mechanical damage, such as cracking, blackening, deformation, etc. "To listen" means to hear if the working sound is normal, such as something that shouldn't be ringing, where it should be, or an abnormal sound. "Smell" means to check whether there is an odor, such as burning or capacitor electrolyte smell. "Touch" means to test whether the temperature of the device is normal by hand; Part of the power device will be hot working, if you feel cold, you can judge that there is no work; It's also problematic if it's hot where it shouldn't be or too hot where it should be. In addition, you should be careful when you touch, try to touch first, not hot.
2. What are the conditions for SMT placing machines to meet the requirements of the production line?
How do I ensure that SMT patches are good and fast? In fact, both the human factor and the material factor account for a part. The human part is the coordination and cooperation of engineers, technicians and operators; The material factor is the SMT mounter. This must take into account the requirements of the production line for the SMT machine. Then what are the conditions for SMT SMT to meet the requirements of the production line? Next SMT patch processing factory in Shenzhen for you to introduce.
What are the conditions for SMT mounters to meet the production line requirements?
SMT mounters meet the requirements of the production line
1. Component mounting accuracy: High-precision mounting plays a decisive role in controlling the precision of components, PCB circuit boards and Z-axis control, avoiding damage to components and PCB circuit boards, and improving production efficiency.
2, appropriate pressure: patch pressure is very critical to the quality of the patch. If the pressure is too low, the solder end or pin of the small component will float on the solder paste, causing the solder paste to not fit the component, resulting in the device and pad offset through the automatic production line or reflow welding; High pressure will squeeze the solder paste, forming solder paste adhesion, damage the structure of components.
3. Patch speed: Different patch machines need to adjust to the corresponding Settings due to different parameters. If not adjusted in time, it may lead to poor component mounting function.
kingford PCBA processing advantages
1. Strength assurance
▪ SMT workshop: We have imported SMT machines and a variety of optical testing equipment, capable of producing 4 million pieces per day. Every process is equipped with QC personnel who can keep a close eye on product quality.
▪ DIP production line: There are two wave welding machines. Among them, there are more than ten old employees who have worked for more than three years. Skilled workers can weld all kinds of insert materials.
2. Quality assurance, high cost-effective
▪ High-end equipment can mount precision heterosexual parts, BGA, QFN, 0201 materials. Proofing can be machine paste, also can be hand pendulum.
▪ Samples and large and small batches can be produced. Proofing starting price 800 yuan, batch starting price 0.008 yuan/point, no start-up fee.
3. Rich experience in SMT and welding of electronic products, stable delivery time
▪ Has served thousands of home appliance subsidiaries, involving various kinds of automotive equipment and industrial control motherboard SMT SMT processing services. Products are often exported to Europe and the United States, the quality of new and old customers affirmed.
▪ On time delivery, usually within 3-5 days after the board is assembled, small batch expedited can also be shipped on the same day.
4. Strong maintenance ability and perfect after-sales service
▪ Experienced maintenance engineers are able to repair defective products caused by various welding problems and ensure the connectivity rate of each circuit board.
▪ 24-hour customer service staff will be ready to respond and resolve your order as soon as possible.