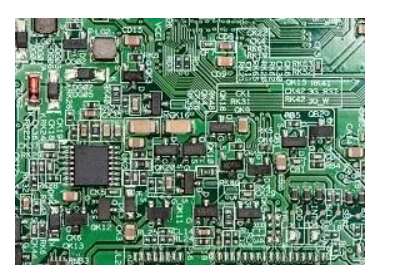
Welding quality detection is an important part of SMT patch processing. The quality of SMT welding is directly related to the quality of the whole electronic processing products. Next, Shenzhen SMT processing manufacturer kingford will introduce the common detection methods of SMT patch processing.
SMT patch processing common detection method
1. Optical detection method
With the decrease of SMT patch component package size and the increase of circuit board patch density, SMA inspection is more and more difficult, manual visual inspection is powerless, its stability and reliability can not meet the needs of production and quality control, so the use of optical detection is more and more important.
2. Manual visual detection method
This method has less input and does not require test program development. However, it is slow and subjective and requires visual observation of the tested area. Due to the lack of visual inspection, it is rarely used as the main welding quality inspection means in the current production line of SMT small batch patch processing plant, and most of it is used for repair and rework.
3. AOI detection method
The use of automatic optical detection as a defect reduction tool can be used to find and eliminate errors early in the patch processing process to achieve good process control. AOI uses advanced vision systems, new light feeding methods, high magnification and complex processing methods to achieve high defect capture rates at high test speeds.
2. How to quickly dismantle wide-body components?
Unlike welding, the key to removing the device from the circuit board is that all the pin solders need to melt at the same time. The most common method of maintenance diswelding is to use a heat gun to simultaneously weld all the pins of the heater. But for wider devices, the use of soldering iron and solder alone can not meet the need to heat all the pins at the same time, with the help of thermal conductive copper wire can play the role of widening the iron head.
For this kind of power MOS tube, the use of conductive copper wire can also achieve the purpose.
For larger SOP chips, longer conductive copper wires are used
What about a wider device? Use longer conductive copper wire. Of course, in addition to the conductive copper wire, it is necessary to apply more solder.
Use a soldering iron to heat the conductive copper wire to melt the IC pin solder
The disassembly process is the balance between the soldering iron heating and the circuit board heat dissipation. If the iron power is small, this heating process will be very long. So use a high power soldering iron to help shorten the disassembly process.
With a high power soldering iron, no matter how big the chip disassembly, is not a problem.
Patient heating, and finally remove the TQPF chip
Add a heat conductor wire around it, and then use solder to add a tin apron to the device. Finally, the device will leave the circuit board.
As long as the master of welding, to deal with any difficult parts of the welding.
kingfordSMT processing ability
1. Maximum board card: 310mm*410mm(SMT);
2. Maximum plate thickness: 3mm;
3. Minimum plate thickness: 0.5mm;
4. Minimum Chip parts: 0201 package or parts above 0.6mm*0.3mm;
5. Maximum weight of mounted parts: 150g;
6. Maximum parts height: 25mm;
7. Maximum parts size: 150mm*150mm;
8. Minimum spacing of pin parts: 0.3mm;
9. Minimum ball parts (BGA) spacing: 0.3mm;
10. Minimum ball parts (BGA) ball diameter: 0.3mm;
11. Maximum parts mounting accuracy (100QFP) : 25um@IPC;
12. Patch capacity: 3-4 million points/day.
kingford specializes in providing overall PCBA electronic manufacturing services, including upstream electronic component procurement to PCB productionand processing, SMT patches, DIP plug-ins, PCBA testing, finished product assembly and other one-stop services.