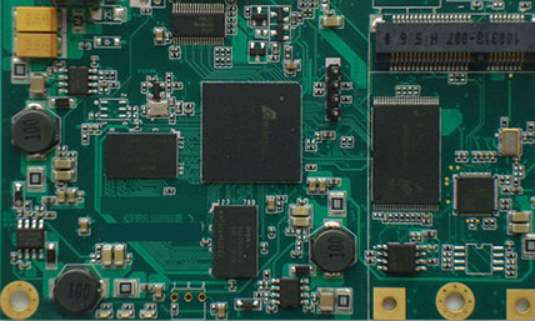
In the electronics industry, PCBA processing mostly adopts SMT processing, there are many common faults in the process of use. According to statistics, 60% of defects are caused by solder paste printing. Therefore, to ensure high quality solder paste printing is an important premise to ensure SMT patch processing quality. Next, Shenzhen SMT manufacturer will introduce how to avoid printing faults in SMT processing.
SMT patch processing printing fault solution
1. There is no gap between the mold and PCB printing mode, which is called "touch printing". All structures require high stability, suitable for printing high precision solder paste. After printing, the wire mesh board has good contact with the printed board and is separated from the PCB. Therefore, the printing precision of this method is high, especially suitable for fine gap and ultra-fine printing.
1. Printing speed.
When the scraper is pushed up, the paste rolls forward. Fast printing facilitates stencil printing.
The rebound also prevents solder paste from leaking. In addition, the slurry can not roll in the screen, resulting in the solder paste clarity is low, which is also the reason for the fast printing speed.
The scale is 10 × 20mm/s.
2. Printing Method:
Common printing methods include touch printing and non-contact printing, screen printing and blank printing on printed circuit boards. Printing method is "non-contact printing", generally 0.5 × 1.0mm, suitable for different viscosity of solder paste. Push the solder paste into the steel mesh with a scraper, punch holes, and contact the PCB board. After the scraper is gradually removed, the steel mesh is separated from the PCB, reducing the risk of vacuum leakage of the steel mesh.
3. Scraper type:
There are two kinds of scraper: plastic scraper and steel scraper. For PITCH≤0.5mm IC, the use of steel scraper should be used for printing, in order to facilitate the formation of solder paste after printing.
4. Adjustment of scraper.
In the welding process, the operating point of the scraper is printed in the direction of 45°, which can significantly improve the non-uniformity of the solder paste opening and reduce the damage of the perforated steel plate. The pressure of the scraper is generally 30N/mm.
Second, the installation should choose the IC installation height of no more than 0.5mm, 0mm or 0~ 0.1mm, so as to avoid the installation height is too low to lead to solder paste collapse, short circuit when reflux.
Three, heavy fusion welding.
The main reasons for assembly failure caused by reflow welding are as follows:
a. The temperature rises too fast;
b. The heating temperature is too high.
c. The heating speed of solder paste is faster than PCB;
d. Excessive water flow.
Therefore, all factors should be taken into full consideration when determining the process parameters of refusion welding to ensure that there is no problem in welding quality before batch assembly.
2. Necessary welding process in DIP plug-in processing
In the production link of SMT patch proofing processing, there is a procedure called DIP plug-in processing, which requires welding, and welding can be divided into soft brazing and hard brazing according to the melting point of the solder. Generally speaking, soft brazing is the welding of melting point below 450 degrees Celsius, and the solder used in the DIP plug-in processing soft brazing processing is naturally called soft brazing solder. At present, various welding methods commonly used in electronic processing plants are generally soft brazing.
DIP plug-in processing of soft brazing related technology
1. Characteristics of soft brazing
① The melting point of the solder is lower than the melting point of the solder.
② Heat until the filler metal melts and wets the welds.
③ Welding process welding parts do not melt.
(4) In order to remove the oxide layer on the metal surface, the welding process needs to add flux.
⑤ The welding process is reversible, can be welded, can be repaired.
2. Brazing process
Whether it is manual welding, dip welding, wave soldering or reflow welding, the welding process must go through several stages of surface cleaning, heating, wetting, diffusion and dissolution, cooling and solidification of the interface of the welding parts.
(1) Surface cleaning
Brazing Welding can only be done on clean metal surfaces.
The function of this stage is to clean up the welding interface of the welding parts, and clean up the oxide film and attached dirt on the interface. Surface cleaning is done by activating the solder with the oxide film on the surface of the solder during heating and before melting.
(2) Heating
Only at a certain temperature can metal molecules have kinetic energy, which can complete wetting, diffusion, dissolution and formation of binding layer in a very short time. So heating is a necessary condition for brazing welding.
For most alloys, the ideal brazing temperature is 15.5 ℃ to 71℃ above the liquidus of the filler metal.
(3) Wetting
Only when the molten liquid filler metal is diffused on the metal surface, the metal atoms can be freely close to each other, so the molten filler metal wetting the solder surface is the primary condition for diffusion, dissolution and formation of bonding layer.
(4) Capillary action, diffusion and dissolution, metallurgical combination to form a binding layer
After the molten filler metal wets the surface of the solder, the bonding layer (weld) is formed after a certain temperature and time under the action of capillary phenomenon, diffusion and dissolution. The tensile strength of the solder joint is related to the structure and thickness of the intermetallic bonding layer and other factors.
(5) Cooling, welding completed
Cooling to the solid phase temperature below, after solidification to form a certain tensile strength of the solder joint.
kingford has its own SMT processing plant, which can provide SMT processing services with minimum package 0201 components. The SMT plant is equipped with 3 Fuji high-speed SMT production lines, 2 DIP plug-in production lines, including AOI optical detector, automatic solder paste printing machine, semi-automatic solder paste printing machine, lead-free wave soldering, lead wave soldering, upper and lower 8 temperature zone reflow welding, PCBA functional testing frame, aging, plate loading machine, cleaning tools, etc., and a professional research and development laboratory is also set up. Five professional engineers cooperate with customers to conduct general function testing, test point testing, as well as channel, noise, waveform, drop and temperature testing.
kingford specializes in providing overall PCBA electronic manufacturing services, including upstream electronic component procurement to PCB production and processing, SMT patches, DIP plug-ins, PCBA testing, finished product assembly and other one-stop services.