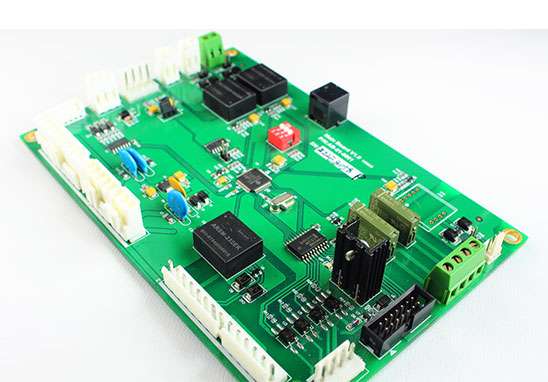
In the production process of DIP plug-in, wave soldering is generally used for welding, which can improve the welding efficiency and realize mass production. However, we know that there is also a post-welding process, requiring employees to use electric soldering iron for welding. This welding speed is relatively slow, but it is also a very important form of welding. In the case of the continuous improvement of PCBA processing automation, why do we need post-welding process? Next, Shenzhen PCBA manufacturer kingford will tell you.
First, what is post-welding processing
Post-welding processing refers to the circuit board after wave soldering, for some components not suitable for wave soldering, through manual welding with electric iron.
Second, the reason for the need for post-welding processing
1. Components are not resistant to high temperature
Today, lead-free technology is becoming more and more popular. The temperature in the furnace is higher than that of the lead when soldering through the wave crest. Therefore, some components that are not resistant to high temperature cannot pass wave soldering.
2. The components are too high
Wave crest welding to the height of the components is also limited, the components will be too high to lead to the wave crest welding.
3. There are a few plug-ins on the side of the wave crest
In a circuit board, there will be some plugins on the over-wave-soldering side, and if it is a small number of plugins, you can use the post-welding finish to improve efficiency.
4. Component plug-in is close to the process edge
The position of the component plug-in near the edge of the plate will encounter the assembly line, which will affect the normal welding.
5. Special components
For customers have special requirements of high sensitivity components, also can not wave soldering. Post welding is a very important welding method in PCBA processing, which can make up for the shortcomings of wave soldering and improve the welding efficiency.
The above is about the need for post-welding processing in PCBA processing.
kingford is a professional PCBA OEM manufacturer, which can provide one-stop services from upstream electronic component procurement to PCB production and processing, SMT patches, DIP plug-ins, PCBA testing, finished product assembly, etc.
Service advantage
1. Strength guarantee
▪SMT workshop: We have imported SMT machines and several sets of optical inspection equipment, with a daily output of 4 million. Each process is equipped with QC personnel, who can keep an eye on product quality.
▪DIP production line: We have two wave-soldering machines, among which there are more than 10 old employees who have worked for more than three years. The skilled workers can weld all kinds of plug-in materials.
2. Quality assurance, cost-effective
▪ High-end equipment can stick precision shaped parts, BGA, QFN, 0201 materials. Can also template patch, loose material hand.
▪ Sample and size batch can be produced, proofing from 800 yuan, batch 0.008 yuan/point, no start-up fee.
3. Rich experience in SMT and welding of electronic products, stable delivery
▪ Accumulated SMT SMT processing services for thousands of electronic enterprises, involving many kinds of automotive equipment and industrial control motherboard. The products are often exported to Europe and the United States, and the quality can be affirmed by new and old customers.
▪ On time delivery, normal 3-5 days after complete materials, small batch can also be expedited on the same day shipment.
4. Strong maintenance ability and perfect after-sales service
▪ Experienced maintenance engineers can repair all kinds of patch welding caused by bad products, to ensure the connection rate of each piece of circuit board