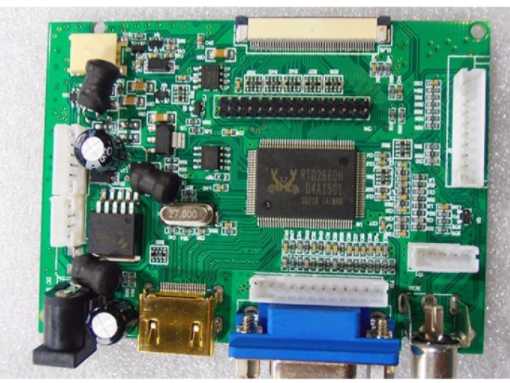
Defect definition
1. Serious shortcoming (CR) : any shortcoming that is enough to cause injury to human body or machine or endanger life safety, such as: inconsistent safety rules/machine burning/electric shock, etc.
2. Main defects (MA) : defects that may cause product damage, functional abnormalities or affect the service life of the product due to materials.
3. Minor shortcomings (expressed by MI) : it does not affect the function and service life of the product. Some defects on the appearance and slight defects or differences on the assembly of the mechanism can still achieve the desired purpose, which are generally differences on the appearance or assembly of the mechanism.
Analysis of solder nouns
1. Tin: The solder is coated on the surface of the solder, the smaller the tin Angle, the better the solder property.
2. Tin-stained Angle: The Angle surrounded by the welding surface and the contact of the fused solder wire, generally for the liquid surface and other welded body or liquid interface, the smaller the Angle on behalf of the solder better.
3. No tin: the surface of the solder can not be well attached to the solder, at this time, the tin Angle is greater than 90 degrees
4. Tin shrinkage: Originally stained with tin solder back, sometimes residual extremely thin solder film, with the shrinkage of solder, tin Angle increases.
5. Solderability: the surface characteristics of molten solder attached to the solder.
Inspection condition of PCBA board
1. In order to prevent contamination of parts or components, gloves or finger covers with full EOS/ESD protection and electrostatic rings must be selected for operation. The light source should be white fluorescent lamp with light intensity above 100 lux and can be clearly seen within 10 seconds.
2. Inspection method: Place the product to be tested about 40cm away from the two eyes, about 45º up and down, and inspect it visually or with a triple magnifying glass.
3. Inspection criteria: (sampling according to QS9000 C=0 AQL=0.4% sampling level; If the customer has special requirements, according to the customer acceptance standards)
4. Sampling plan: MIL-STD-105E LEVEL Ⅱ Normal type single sampling
5. Criterion: Serious Defect (CR) AQL 0%
6. Major disadvantages (MA) AQL 0.4%
7. Minor Weakness (MI) AQL 0.65%
2. How to deal with tail cleaning in PCBA OEM production?
PCBA OEM production and material production manufacturing tail cleaning actually means that the processing line produced by the product settlement order. Many PCBA OEM factories are very slow in the important link of tail cleaning and the delivery quality is poor, which affects the delivery cycle of customers and leaves a bad impression on customers. In fact, PCBA production and processing of tail cleaning is a very important link.
In the case of late tail cleaning in PCBA OEM production, many drawbacks will be caused. For example, it wastes a lot of time to carry out frequent replenishment when carrying out tail cleaning, which leads to the increase of manufacturing costs. Every time you fill, you have to stop the line. The value of the time you stop the line far exceeds the value of the fill. It will also increase the product delivery cycle and bring some troubles to customers. In fact, some measures can be taken to clean the tail of PCBA production and processing to improve work efficiency.
1. About 40pcs of PCB board shall be taken off the line before the product comes off the line. The line operator shall quickly clean out the loose material inside the machine and equipment and the material belt bin.
2. The operator or inform the line following technician to carry out manual repair by QC inspection in the machine and equipment program skip, mark and paste the raw material position number on the board, and pass the furnace only after the quality engineer checks.
3. If the loss of raw materials is caused by the manual pasting of raw materials, the intermediate inspection shall count out the quantity of missing raw materials to the line operator or team leader in time, and the operator and the intermediate inspection QC shall check the raw materials again. Finally, according to the loss of raw material to issue a supplement.
4. Nuclear supplement loss of raw materials must be accurate, avoid doing frequent unnecessary work.
The speed and quality of PCBA tail cleaning can reflect the management level of a PCBA factory.