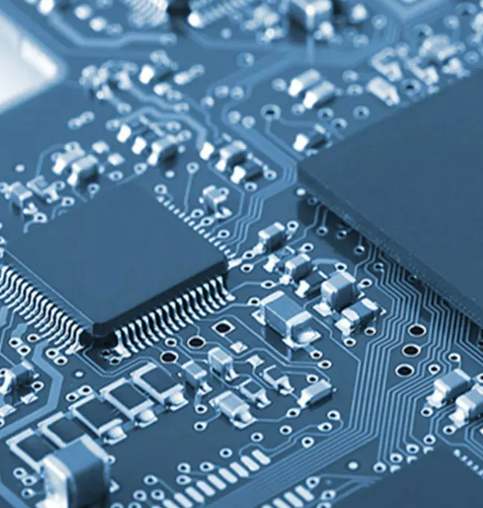
The main purpose of solder paste printing technology is to solve the problem of incompatibility with solder paste printing quantity (solder paste filling amount and transfer amount). According to professional statistics, in the case of correctly designed PCB, 60% of the reworked PCB is due to poor solder paste printing. Three important "S" must be kept in mind in solder paste printing: solder paste, steel mesh and scraper. If selected correctly, excellent printing results can be obtained.
1. The quality of solder paste
As a necessary material for reflow welding, welding paste is a kind of welding paste composed of alloy powder and flux (rosin, thinner, stabilizer, etc.) uniformly mixed, in which alloy powder is a key element to form solder joint. Flux is the key material to eliminate surface oxidation, improve wettability and ensure the quality of solder paste. In terms of mass, generally speaking, 80% to 90% of the solder paste belongs to metal alloys, while accounting for 50% of its volume. Solder paste quality assurance mainly comes from two aspects: storage and application. Solder paste is usually stored between 0 and 10℃, or according to manufacturer's requirements. For its application, the temperature of the SMT shop must be 25 ° C ±3 ° C and the humidity must be 50% ± 10%. Moreover, its recovery time must be more than 4 hours, and must be fully stirred before use, so that the viscosity has excellent printability and release deformation. The solder cap must be placed correctly after the solder paste is applied, and the solder paste coated circuit board must be reflow welded within two hours.
2, steel mesh design
The key function of the steel mesh is to evenly coat the solder paste on the PCB circuit board pad. Steel mesh is essential in printing technology, and its quality directly affects the quality of solder paste printing. So far, there are three ways to make steel mesh: chemical etching, laser cutting and electroplating. Mold design will not be assured until the following aspects are fully considered and properly addressed.
3, the thickness of the steel plate
In order to ensure the quantity and quality of the solder paste, the surface of the steel mesh must be smooth and flat, and the selection of the thickness of the steel plate should be determined by the components with the minimum spacing between the pins.
4. Aperture design
The opening is trapezoidal cut face, and the opening is trumpet shape. Their walls are smooth without burrs. Width/thickness ratio = hole width/thickness of steel mesh (for small spacing QFP, IC); Area ratio = base area of hole/wall area of hole (for 0201, BGA, CSP parts). (1) welding ball processing. Solder ball treatment applied to steel mesh of 0603 or above CHIP components can effectively avoid the formation of solder balls after reflux. For components with too large pads, mesh partitioning is recommended to prevent excessive tin formation.
(2) Mark. At least 3 MARK points should be generated on the B side of the steel mesh, and the steel mesh should be compatible with the MARK on the PCB board. To increase printing accuracy, there should be a pair of MARK points with the longest diagonal distance.
(3) printing direction. Printing direction is also a key control point. Components that are slightly spaced from each other should not be too close to the guide rail during the process of determining the printing direction. Otherwise, too much tin may lead to bridging.
5. Scraper
The scraper is based on its different hardness materials and shapes, which will affect the printing quality to some extent. Usually, a steel scraper with nickel plating is used, usually a 60° scraper. If there is a through-hole component, a 45° scraper is recommended to increase the tin content on the through-hole component.
6. Printing parameters
Printing parameters mainly include scraper speed, scraper pressure, steel mesh downward release speed, steel mesh cleaning mode and frequency. There is indeed a limiting relationship between the Angle of the scraper and the steel mesh and the viscosity of the solder paste, so only by correctly controlling these parameters can we ensure the printing quality of the solder paste. In general, the low speed of the scraper results in relatively high print quality, and the shape of the paste can be blurred. In addition, the extremely low speed even reduces manufacturing efficiency. Conversely, a high speed scraper may result in an underfilling of solder paste in the mesh. Too high a scraper pressure may result in insufficient tin, which increases wear between the scraper and the steel mesh, while very low pressure will result in incomplete solder paste printing. Therefore, when rolling the solder paste normally, the speed should be increased as much as possible. In addition, the scraper pressure should be adjusted for high printing quality. A very high downward release speed may cause the solder paste to ice or form undesirable phenomena, while a low release speed will affect the manufacturing efficiency. Improper cleaning mode and frequency of steel mesh will lead to incomplete cleaning of steel mesh, continuous tin electrodeposition or insufficient tin in steel mesh will lead to narrow space products. A very high downward release speed may cause the solder paste to ice or form undesirable phenomena, while a low release speed will affect the PCB manufacturing efficiency. Improper cleaning mode and frequency of steel mesh will result in incomplete cleaning of steel mesh, continuous tin electrodeposition or insufficient tin in steel mesh will result in narrow space products. A very high downward release speed may cause the solder paste to ice or form undesirable phenomena, while a low release speed will affect the manufacturing efficiency. Improper cleaning mode and frequency of steel mesh will result in incomplete cleaning of steel mesh, continuous tin electrodeposition or insufficient tin in steel mesh will result in narrow space products.
7. Equipment accuracy
In high density and small space printing products, printing accuracy and repeat printing accuracy will affect the stability of solder paste printing.
8. PCB support
PCB support is an important adjustment content of solder paste printing. If the PCB lacks effective support or is improperly supported, thick or uneven solder paste should be used. The PCB support shall be arranged flat and evenly to ensure the tightness between the steel mesh and the printed circuit board.