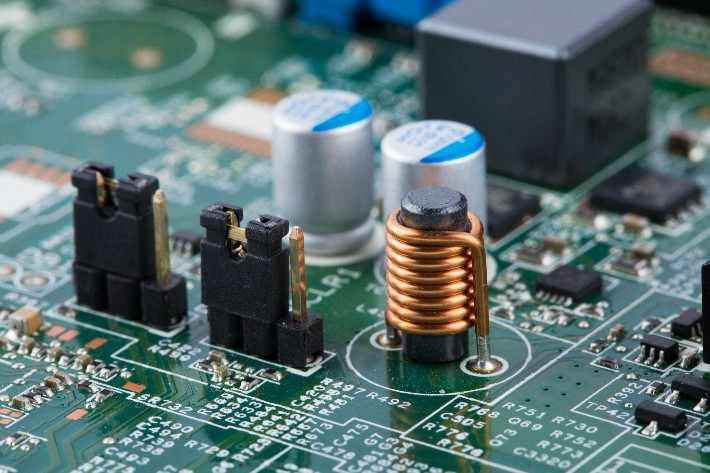
Common PCB circuit board line is protruded in the substrate, but also some customers require the line and substrate media as much as possible, to reduce the degree of exposure of the line. The unique place of this kind of product is generally thick copper, and the line width and line distance are larger, the need for the line media supplement. In this paper, we will introduce a production process of PCB circuit board and substrate successfully in the form of natural resin supplement, which can make the circuit of this kind of thick copper products stand out from the substrate. 15um, the line gap filling is full, and the common use needs such as satisfactory reliability.
If the contact or line on the circuit board needs to contact with the parts over and over again, with the passage of the product office hours, the appearance of the metal will reveal a certain wear, so the contact is not good. Therefore, some customers put forward the PCB circuit board manufacturing needs of line and substrate level, to prevent excessive wear of the metal layer exposed on the board surface. This kind of product generally has thicker copper surface and larger line width and line distance. Because this relatively simple manufacturing scheme is to supplement natural resin as the medium between lines, this paper uses Shaojie natural resin as the medium material to supplement the plate making scheme of lines.
Circuit and substrate flush PCB circuit board manufacturing essentials
Line and substrate level PCB circuit board products, the surface copper is thicker, generally greater than 3oz, and line width line distance is also looser, generally greater than 8mil/8mil, more conducive to filling operation. Filling customers generally require that the line edge of the pointed rubber layer should not be higher than 15um, and the core of the filling part should not be lower than 10um. In addition to satisfying the requirements of common PCB, in the aspect of reliability, thermal shock test can not reveal the layered burst board, cracks in the rubber layer and other things.
From the above board making requirements, this kind of PCB circuit board requires that the lines are filled with natural resin, and the core of the filling part can not be too large to sink into, and by increasing the glue content to make the natural resin overflow can better prevent the initiation of the problem of sinking into, but it poses a greater challenge to the removal of glue. In the form of glue removal generally laser glue and grinding plate glue, but for large plane or object surface size line and thicker glue layer, it is more appropriate to choose grinding plate glue removal, but in the process of grinding plate glue removal, it is possible to reveal the copper layer is worn too thin. In addition to this, the filling process may be due to the line distance and copper thickness and the special nature of natural resin exposed in the situation of bubbles or insufficient filling, resulting in the reliability of the product suffered.
Line and substrate flush PCB board line filling and removing glue
First, line filling glue
As one of the places that is not easy to solve for the board of this product, the operation quality is related to the types of natural resin, copper thickness height and line spacing. Generally, the lower the viscosity of natural resin, the thinner the appearance of copper, the wider the line spacing, the more fully filled and easily exposed bubbles. Because this in the vote to use a natural resin before filling, to try to find out the filling properties of this kind of natural resin.
Using a 4oz copper thickness as an example, the filling effect of a natural resin was tested on a trial board with a preset different line spacing, increasing the line spacing layer by layer from 8mil.
It can be seen that the test is still relatively ideal, in 8mil line distance above the successful achievement of full filling, but the demand points out that when the copper thickness of the product increases or the line distance changes from large to small, or the natural resin to change the type of product, the need to re-calibrate its filling experience, in order to ensure that the labor ability satisfied with the filling needs.
Two, board surface removal glue
Although the natural resin overflow in the process of filling can prevent the core area of filling to sink into, but too much overflow will increase the difficulty of the glue removal process. If it is appropriate to use the grinding board for gumming removal processing, the whole board can be polished with the abrasive belt grinder first, and then the residual glue can be polished with manual grinding facilities. The clue of processing thinking lies in cutting the glue layer thickness of the whole board until the copper skin of the outer line is exposed. The subsequent manual grinding of part of the residual glue can clean up the thicker residual glue and reduce the abrasion degree of the copper surface.
In addition to the actual grinding plate glue process, the worst thing is the board surface exposed in the situation of copper exposed, and the size of the surface of the large plane or object residual glue needs manual disposal, obviously a great deal of doing so. In order to reduce such a situation, the filling process should manage and control the thickness of the overflow glue and the average of its appearance, such as optimizing the scraping process or the static period after filling glue, and then implement the post-processing after the smooth rubber layer.
Circuit and substrate flush PCB circuit board process preset
The preset difference between this process and conventional PCB product manufacturing is that the base copper of the outer copper thick is almost the finished copper thick. Based on this unique place, the outer line and hole processing process is probably the first line of thick bottom copper corrosion carving, and then the line implementation of natural resin supplement, continue to drill through the hole and hole metallization, and then separate plating holes to improve the thickness of the hole copper, and finally etching the thin copper layer of the filling position. Therefore, it is satisfied with the common PCB manufacturing requirements and the requirement that the circuit is flush with the substrate.
In addition, when the customer's requirements for product smoothness include external treatment, the processing process of copper surface height should be properly adjusted to satisfy the smoothness requirements after external treatment.
Machining effect
Manufacture the sample according to the above process, and make sample slices, so that how many samples together the base material and line top drop.
It can be seen that the PCB sample of the line flush with the substrate is satisfied with the drop. In fact, if the grinding process and hole metallization process are further optimized, it will help to obtain a smaller drop, so as to achieve better flatness.
To sum up, the key point of this kind of line and substrate flush printed circuit boardis to make the line and substrate processing out of flush effect, and the processing key is to affect the product reliability of the filling and removal of glue processing process, in addition to this product processing flatness also depends on the outer line and the appearance of the disposal process of emergency appropriate.
At present, there are few literatures about this kind of products. Some assumptions and tests made by this subject to solve the problems in the manufacturing process of this kind of products have some shortcomings. But in the product differentiation of the number of increasing today, the needs of customers is our research office inspiration and power, new search never stop.