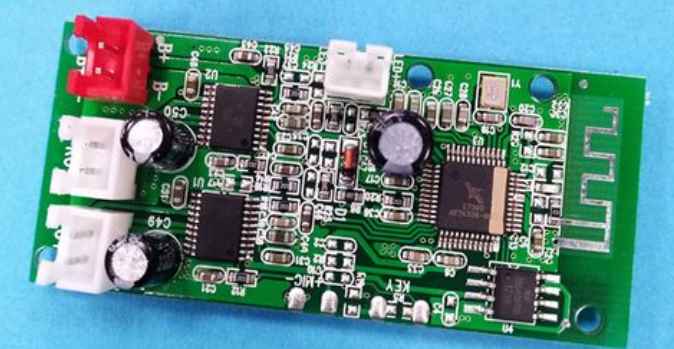
Fake welding and fake welding processed by PCBA will seriously affect the use quality of products. Therefore, fake welding and fake welding should be reduced to a minimum in PCBA processing. Next, let kingford introduce the causes and solutions of fake welding and fake welding processed by PCBA.
What is virtual welding? Virtual welding refers to the existence of an isolation layer between the solder and the pin, that is, the contact between the element and the pad is bad, they are not fully in contact with each other, the naked eye can not be seen, but its electrical characteristics and no conduction or conduction is bad, affecting the circuit characteristics.
What is false welding? False welding is similar to virtual welding, is the initial circuit work normally, later gradually appear open circuit phenomenon.
First, the cause of virtual welding/false welding?
1. Oxidation of pad and pin of components
It is easy to cause that in reflow welding, the solder paste in the state of liquefaction can not be fully infiltrated into the pad, and tin climbing, resulting in virtual welding.
2. Less tin
In the process of solder paste printing, the opening of the steel mesh is too small or the pressure of the scraper is too small, which leads to less tin. As a result, the amount of solder paste is not enough during welding and the components cannot be fully welded.
3. The temperature is too high or too low
The temperature is too high, not only the solder flow, but also aggravate the surface oxidation rate, may also produce virtual welding.
4. Low melting point of solder paste
Low temperature solder paste, the melting point is relatively low, and the pin of the component and the plate material of the fixed component are different, the coefficient of thermal expansion is different, with the change of the working temperature of the component for a long time, under the force of thermal expansion and cold contraction, there will be virtual welding phenomenon.
5. Quality problem of tin paste
The solder paste quality is not good, the solder paste is easy to oxidize, the loss of flux, will directly affect the solder paste welding performance, from causing virtual welding/false welding.
Two, the solution to the virtual welding/false welding method
1. Moisture-proof storage of components:
PCBA processing plants are equipped with ovens that can bake moisture components during the welding process to replace oxidized components.
2, choose well-known brand solder paste:
In the process of PCBA welding, the defects of false welding and false welding have a great relationship with the quality of solder paste.
3. Adjust printing parameters:
In the printing process, the pressure of the scraper should be adjusted, the appropriate steel mesh should be selected, and the steel network port should not be too small to avoid the situation of too little tin.
4, adjust the reflow welding temperature curve:
In the reflow welding process, we should control the welding time. If the time is not enough in the preheating zone, the flux can not be fully activated and the surface oxide of the welding can be removed. If the time is too long or too short in the welding zone, it will cause virtual welding and false welding.
5, choose the right detection equipment:
AOI testing equipment or X-ray testing equipment is selected to detect welding quality and reduce the outflow of fake welding defective products.
The above is about the "PCBA processing welding and false welding causes and solutions" introduction, hope to have some help to you, more PCBA information please pay attention to the content of the site update! Shenzhen kin SMT production gford is a professional PCBA processing enterprise, with fully automatic SMT production line and wave soldering, for you to open the whole production and quality testing process