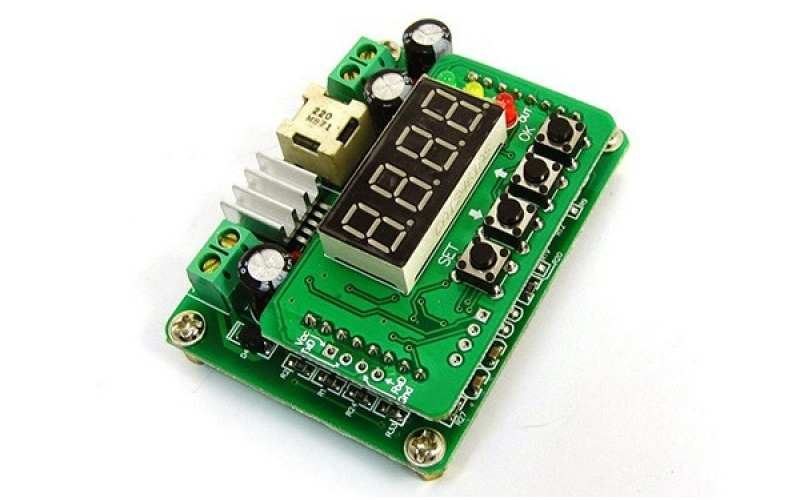
Denser PCB board, higher bus speeds, and analog RF circuits present an unprecedented challenge to testing, and functional testing in this environment requires careful design, thoughtful testing methods, and appropriate tools to provide reliable test results.
When dealing with fixture suppliers, it is important to keep these issues in mind as well as to think about where the product will be manufactured, which is an area that many test engineers overlook. For example, let's say the test engineer is in California and the product is manufactured in Thailand. The test engineer will think that the product needs an expensive automated fixture because the plant in California is expensive, requires as few testers as possible, and uses automated fixtures to reduce the need to employ highly skilled and highly paid operators. But in Thailand, where neither of these problems exist, it's cheaper to have people solve them because labor costs are so low, land is so cheap, and big factories aren't a problem. Therefore, sometimes first-class equipment may not be popular in other countries.
1. Technical level
In high-density UUT(Under Unit Test), if calibration or diagnosis is required, a manual probe is likely to be required, due to limited needle bed contact and faster testing (testing the UUT with a probe can quickly collect data rather than feed information back to the edge connector), which requires an operator to probe the test points on the UUT. Wherever you are, make sure the test site is clearly marked.
Probe types and ordinary operators should also be aware, issues to consider include:
1. Is the probe larger than the test point? Is the probe in danger of short-circuiting several test sites and damaging the UUT? Is there an electric shock hazard to the operator?
2. Can each operator quickly find out the test point and inspect it? Is the test site large and easy to identify?
3. How long does it take the operator to press the probe on the test point to get an accurate reading? If the time is too long, there will be some trouble in the small test area, such as the operator's hand will slide due to the long test time, so it is recommended to expand the test area to avoid this problem.
After considering the above issues, the test engineer should re-evaluate the type of test probe, modify the test file to better identify the test point location, or even change the operator requirements.
2. Automatic probe
Automated probes should be considered in situations where they are required, such as when printed circuit board are difficult to probe manually, or when the testing speed is greatly reduced by the operator's skill level.
Automated probe eliminates human error, reduces the likelihood of short circuits at several test sites, and speeds up test operations. However, be aware that automated probes may have some limitations, which vary depending on the vendor's design, including:
(1), the size of UUT
(2) The number of synchronous probes
(3) How close are the two test points?
(4) To test the positioning accuracy of the probe
(5) Can the system carry out two-sided detection of UUT?
(6), how fast does the probe move to the next test point?
(7) What is the actual interval required by the probe system? (It is generally larger than offline functional test systems)
Automated probes usually do not touch other test points with a needle bed fixture, and are generally slower than the production line, so two steps may be required: If the probes are used only for diagnosis, consider using a traditional functional test system on the production line and placing the probes as the diagnostic system at the edge of the production line; If the purpose of the probe is UUT calibration, then the only real solution is to use multiple systems, which is still much faster than manual operation.
How to integrate it into the production line is also a key issue that must be studied. Is there room on the production line? Can the system be connected to the conveyor belt? Fortunately, many of the new detection systems are compatible with the SMEMA standard, so they work in an online environment.
3. Boundary scanning
This technique should be discussed early in the product design phase, as it requires specialized components to perform this task. In a PCB circuit board dominated by digital circuits, devices can be purchased with IEEE 1194(boundary scanning) support, which solves most diagnostic problems with little or no probing. Boundary scanning reduces the overall functionality of the UUT because it increases the area of each compatible device (adding 4-5 pins per chip and some wiring), so this technique was chosen on the principle that the cost should improve the diagnostic results. It should be remembered that boundary scanning can be used to program flash memory and PLD devices on the UUT, which further increases the reason for choosing this test method.
How to deal with a limited design?
If the UUT design is complete and settled, the options are limited. Of course, you can also ask for changes in the next revision or new product, but it always takes time for the process to improve, and you still have to deal with the current situation.