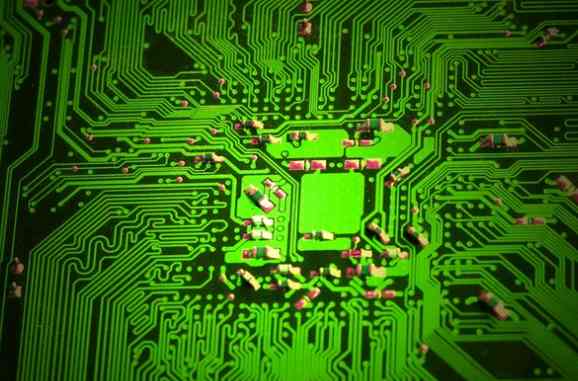
The IC sealing plate also needs to solve the problem of inconsistent coefficient of thermal expansion with semiconductor chip. The thermal expansion coefficient of insulating substrate is generally too large (generally at 60ppm/℃), even if the laminated multilayer board is suitable for the fabrication of microcircuits. The thermal expansion coefficient of the substrate is about 6ppm, which is close to that of the semiconductor chip. It is indeed a "difficult challenge" for the manufacturing technology of the substrate.
In order to adapt to the development of high speed, the dielectric constant of the substrate should reach 2.0, and the dielectric loss factor should be close to 0.001. To this end, a new generation of printed circuit boards beyond the boundaries of traditional substrate materials and traditional manufacturing processes is expected to appear in the world around 2005. The technological breakthrough, first of all, is the breakthrough in the use of new substrate materials.
To predict the future development of IC packaging design and manufacturing technology, there are more strict requirements for the substrate materials used. This is mainly manifested in the following aspects:
1. High Tg property corresponding to lead-free flux.
2. Achieve a low dielectric loss factor matching the characteristic impedance.
3. The low dielectric constant (ε should be close to 2) corresponding to high speed.
4. Low warpage (improvement of flatness of substrate surface).
5. Low moisture absorption rate.
6. Low thermal expansion coefficient, so that the coefficient of thermal expansion is close to 6ppm.
7. The low cost nature of IC sealing loading plate.
8. Substrate materials containing components of low cost nature.
9. In order to improve the heat resistance impact, the basic mechanical strength is improved. Substrate material suitable for temperature change from high to low cycle without degradation of performance.
10. Green substrate material with low yield and suitable for high regenerative welding temperature.
Four, with special functions of copper coated plate
The copper clad plates with special functions referred to here mainly refer to metal base (core) copper clad plates, ceramic base copper clad plates, high dielectric constant plates, copper clad plates (or substrate materials) for embedded passive component type multilayer plates, copper clad plates for light-wire subgrade boards, etc. To develop and produce this kind of copper clad plate is required not only for the development of new technology of electronic information products, but also for the development of aerospace and military industry.
Five, high performance flexible copper clad plate
flexible printed circuit board (FPC) has experienced more than 30 years of development since its industrial production. In the 1970s, the FPC began to enter truly industrial mass production. In the late 1980s, due to the emergence and application of a new polyimide film material, FPC appeared non-adhesive type FPC(generally referred to as "two-layer FPC"). In the 1990s, the world developed the sensitive covering film corresponding to the high density circuit, so that the design of FPC has a great change. Due to the opening up of new application areas, the concept of its product form has changed a little, which extends it to include TAB, COB with a larger range of substrate. In the second half of the 1990s, the high density FPC began to enter large-scale industrial production. Its circuit pattern, the rapid development to a finer degree. Demand for high-density FPCS is also growing rapidly.
The current output value of FPC production in the world last year reached about $3 billion - $3.5 billion. In recent years, the world's production of FPCS has been growing. Its proportion in PCBS is also increasing year by year. In the United States and other countries, FPC accounts for the total output value of printed circuit boards has reached 13%-16%, FPC is becoming a very important and indispensable variety of PCB.
In terms of flexible copper cladding plate, there is a great gap between advanced countries and regions in terms of production scale, manufacturing technology level and raw material manufacturing technology. This gap is even greater than rigid copper cladding plate.
The development of the technology and production of copper clad plate and the electronic information industry, especially the development of PCB industry is synchronous and inseparable. This is a process of continuous innovation and pursuit. The progress and development of copper clad plate is also driven by the innovation and development of electronic machine products, semiconductor manufacturing technology, electronic installation technology and PCB manufacturing technology. In this case, common progress and synchronous development are particularly important.