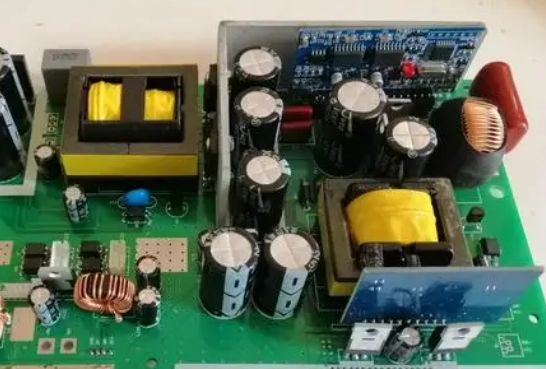
First, the final porcelain pottery supplement thermosetting materials
Processing method:
And epoxy gas natural resin/glass woven cloth (FR4) is roughly similar to the processing process, but the circuit boardis brittle, easy to break the plate, drilling and gong plate drilling and gong knife survival years to reduce 20 percent.
Two, PTFE (polytetrafluoroethylene) material
Processing method:
1. Opening: be sure to save and try to take care of the film opening, avoid scratches, indentation
2. Drilling:
(1) With a new drill nozzle (standard 130), one piece in a stack is the best, the presser foot pressure is 40psi
(2) The aluminum sheet is the cover plate, and then the PTFE plate is pressed with 1mm dense amine plate
(3) After drilling, blow out the dust in the hole with an air gun
(4) With the most stable drilling machine, drilling parameters (basically, the smaller the hole, the faster the drilling rate, the smaller the Chip load, the smaller the return rate)
3. Hole disposal
Plasma treatment or sodium naphthalene activation treatment is conducive to hole metallization
4.PTH copper sinking
(1) After micro-etching (with a micro-etching rate of 20 microinch choke), pull into the plate from the de-oil cylinder at the PTH
(2) If there is a need, the second PTH will be performed. Cylinder hand into the plate
5. Welding resistance
(1) Before disposal: consider appropriate and use acid washing plate, can not use mechanical grinding plate
(2) After pretreatment, the baking plate (90℃, 30min) was brushed with green oil for curing
(3) Three sections of baking plate: a section of 80℃, 100℃, 150℃, each time 30min (if found the substrate surface oil, can be reworked: wash off the green oil, new activation disposal)
6. Gong boards
The white paper is laid on the PTFE board line surface, and the FR-4 substrate board or phenolic bottom board is clamped with a thickness of 1.0MM.
When selecting the substrate used for PCB of high frequency circuit, we should especially investigate the special nature of the material DK, which changes under different frequencies. DF and its performance under the conditions of frequency, temperature and humidity are mainly investigated for the requirements of high-speed transmission of signals, or the requirements of impedance suppression with special properties.
Under the condition of frequency change, the DK and DF values of the ordinary base plate can be changed greatly. Especially in the l MHz to l GHz frequency, their DK, DF value changes are more superficial. For example, the DK value of ordinary epoxy gas natural resin and glass fiber cloth based substrate material (ordinary FR-4) is 4.7 at lMHz frequency, and the DK value varies to 4.19 at lGHz frequency. When the DK value exceeds lGHz, the change direction is gentle. Its change direction is to increase the frequency, and become smaller (but the change range is half large), for example, in l0GHz, the DK value of ordinary FR 1 4 is 4.15, with high speed, high frequency special properties of the substrate material in the frequency change situation, DK value change is small, from lMHz to lGHz change frequency, DK mostly maintained a range of 0.02. Under the condition of different frequency from low to high, the DK value has a slightly decreasing tendency.
The media loss factor (DF) of ordinary substrate materials, under the influence of frequency variation (especially in the high frequency range), the variation of DF value is larger than DK. Its change law is tending to increase, because this, in the reputation of a high frequency of a substrate material, the focus of the investigation is its DF value changes. With high speed and high frequency special properties of the substrate material, in high frequency change special properties, there are two types of ordinary substrate material surface is not the same as the two types: one is with the change of frequency, its (DF) value changes very small. There is also a class in the range of change with the ordinary type of substrate material although similar, but its own (DF) value is low.
Select PCB board material must be satisfied with the preset needs, mass production, cost in the middle of the balance point. In short, the presets need to contain both electrical and structural reliability. Generally in the preset very high speed PCB wrench (greater than GHz frequency) this board problem will be relatively tight. For example, today's commonly used FR-4 material, the media loss Df (Dielectricloss) at a few GHz frequency will be very large, it may not be comfortable to use.
For example, a high-speed digital signal of 10Gb/S is a square wave, which can be viewed as a superposition of sine-wave signals of different frequencies. Because this 10Gb/S contains a lot of different frequency signals: 5Ghz fundamental signal, 3 order 15GHz, 5 order 25GHz, 7 order 35GHz signal. Maintaining the integrity and abruptness of the digital signal and the low loss and distortion of the RF microwave transmission (the high frequency harmonics of the digital signal locally reaching the microwave band). Because of this, the PCB selection requirements for high speed digital circuits are similar to those for RF and microwave circuits in all respects.
In the actual engineering operation, the selection of high-frequency board materials seems simple, but there are still too many factors to consider. Through the introduction of this paper, as a PCB board preset engineer and a person in charge of high-speed project, I have a certain understanding of the special nature and selection of board materials. Understand electrical properties, thermal properties, reliability, etc. And reasonable use of overlap, preset a piece of reliable high, good processing products, various factors considered to achieve the optimal.
The main factors to consider in selecting appropriate board materials are:
1. Manufacturability:
For example, how many times pressing performance, temperature performance, CAF/ heat resistance and mechanical toughness (viscosity) (reliable), fire rating;
2. Various properties (electrical, performance stability, etc.) compatible with the product:
Low damage, solid Dk/Df reference, low dispersion of color light, small variation coefficient with frequency and background, small material thickness and adhesive content tolerance (good impedance choke), if the line is long, consider the problem of low finish copper foil. In addition, the previous stage of the preset high-speed circuit needs to be simulated, and the final simulation result is the reference standard of the preset. "Xingsen Science and Technology - Agilent (High Speed/RF) Joint Laboratory" has solved the difficult problem that the final simulation results are not exactly the same as the test results. It has done a large number of simulation and actual test closed-loop verification, and can achieve the simulation and measurement are exactly the same through the unique method.
3. Early availability of materials:
Many high-frequency board acquisition and purchase cycle is very long, even 2-3 months; In addition to common high frequency board RO4350 storage, many high frequency board demand customer supply. Because of this, high-frequency plate needs and manufacturers early communication, as soon as possible to prepare materials;
4. Cost factor
Look at the price sensitivity of the product, is consumer products, still communication, medical, industrial, military applications;
5, the suitable use of laws and regulations, etc. : to be integrated with different national environmental protection laws and regulations, satisfied with RoHS and halogen-free requirements.
Among the above factors, the speed of high-speed digital circuit is the main factor of PCB selection. The higher the efficiency of the circuit, the smaller the Df value of the selected PCB should be. With medium, low damage circuit board will adapt to 10Gb/S digital circuit; The board with lower damage is suitable for 25Gb/s digital circuit; The ultra-low loss of the board will be suitable for faster high speed digital circuits, the efficiency can be 50Gb/s or more.
Seen from the material Df:
Df between 0.01 and 0.005 circuit plate ADAPTS to a maximum of 10Gb/S digital circuit;
Df between 0.005 and 0.003 circuit plate ADAPTS to a maximum of 25Gb/S digital circuit;
Df not more than 0.0015 circuit plate suitable for 50Gb/S or higher speed digital circuits.
The above summary of how to select PCB high-speed board material and preset attention to things of the project, the actual application also has to be analyzed according to the specific case examples.