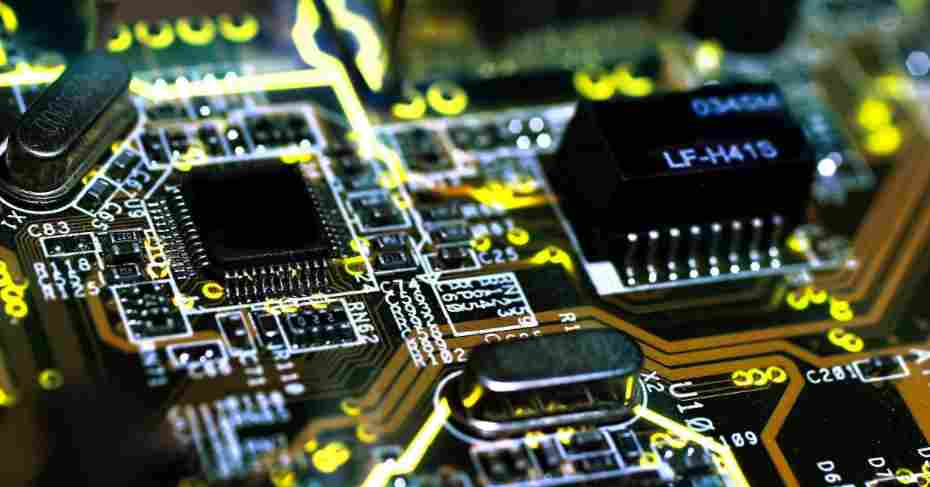
What is reliability?
Reliability refers to "reliable", "trustworthy", refers to the product under the specified conditions and within the specified time, the ability to complete the specified function. For the end product, the higher the reliability, the higher the use guarantee.
PCB reliability refers to the ability of "bare board" to meet the production conditions of subsequent PCBA assembly, and to maintain normal operation function in a certain period of time under specific working environment and operating conditions.
How does reliability develop into a social focus?
In the 1950s, during the Korean War, 50 percent of American electronic equipment failed in storage, and 60 percent of airborne electronic equipment became unusable after being shipped to the Far East. The United States found that unreliable electronic equipment interfered with the conduct of war, and that annual maintenance costs were twice as high as equipment purchases.
In 1949, the American Society of Radio Engineers established the Reliability Technology Group, the first professional academic organization of reliability. In December 1950, the United States set up the "Electronic Equipment Reliability Committee", the military, weapon manufacturing companies and academia began to intervene in the reliability research, by March 1952 put forward far-reaching recommendations; The research results were first applied to aerospace, military, electronics and other military industries, and then gradually expanded to civil industry.
In the 1960s, with the rapid development of the aerospace industry, reliability design and test methods were accepted and applied to avionics systems, and reliability engineering developed rapidly! In 1965, the United States issued the "System and Equipment reliability Outline Requirements", reliability engineering activities combined with the traditional design, development and production, and obtained better benefits. ROM Aviation Development Center has set up a reliability analysis center, which is engaged in the reliability research of electronic and electromechanical, mechanical parts and electronic systems related to electronic equipment, including reliability prediction, reliability distribution, reliability testing, reliability physics, reliability data acquisition, analysis, etc.
In the 1970s, the problem of life cycle cost of American defense weapon systems became prominent, and people more deeply realized that reliability engineering was an important tool to reduce life cost. Reliability factory was further developed, and more strict, more practical and more effective design and test methods were adopted, which led to the rapid development of failure research and analysis technology.
After 1990s, reliability engineering developed from military enterprises to civil electronic information industry, transportation, service, energy and other industries, from a professional to a "general industry". ISO9001 quality management system reliability management is included in the review of the important content, the reliability of the professional technical standards have been incorporated into the quality management system documents, become "said to be done" management provisions.
Today, reliability management has been widely accepted by all walks of life in the society, and the business philosophy is generally changed from the past "want me to attach importance to product reliability" into the present "I want to attach great importance to product reliability"!
Why is reliability more important?
When the space shuttle Challenger exploded 76 seconds after takeoff in 1986, killing seven astronauts and causing $1.3 billion in damage, it was because of a failed seal.
In the 1990s, UL published an article saying that PCB made in China caused a number of equipment fires in the United States. The reason was that PCB factories in China used non-flame retardant boards, but they were UL marked.
According to official statistics, the compensation caused by the reliability failure of PCBA accounts for more than 90% of the external failure cost!
GE analyzed that even a 1 percent increase in reliability and a 10 percent increase in cost for equipment that operates continuously, such as energy, transportation, mining, communications, industrial control and medical services. High reliability of PCBA, maintenance costs, downtime losses can be significantly reduced, assets and life safety more guaranteed!
Today, looking at the world, the competition between countries has evolved into the competition between enterprises. Reliability engineering is the threshold for enterprises to carry out global competition, but also the magic weapon for enterprises to stand out in the increasingly fierce market.
3) Quality control management: standardize the quality monitoring standards, improve the quality assurance system, and assist the production process to improve quality;
02 Process Management
1) Quality and product safety system: IATF16949, ISO9001, GJB9001, UL, CQC, RoHS;
2) Engineering design: DFM specifications for laminated structure, impedance, minimum linewidth, minimum spacing, minimum aperture, copper thickness, etc.; Production process design, material selection, manufacturability document design, etc.
3) Production materials: supplier review, material evaluation, raw material inspection, raw material storage, etc.;
4) Process technology: process capacity, production parameters, liquid use, first FA, etc.;
5) Equipment and facilities: evaluation, daily spot inspection, progress testing, predictive maintenance, preventive maintenance, periodic overhaul, etc.;
6) Working environment: dust-free, constant temperature, humidity, illumination, etc.;
7) Quality control: incoming IQC, process IPQC, process IPQA, final inspection FQC, outgoing OQC, reliability test, etc.;
8) Management team: operation norms, risk identification, problem analysis, strategy analysis, etc.;
03 Quality assurance inspection
1) Quality yield: real-time monitoring;
2) Quality reliability: real-time/regular verification;
3) Quality consistency: real-time/on-demand audit;
4) Average failure-free service time: regular/on-demand verification;
04 Test and Verification
1) Signal performance: impedance test, signal loss;
2) Heat resistance: thermal stress, Tg test, TMA test;
3) Interconnection performance: IST test, current resistance, cold and hot shock;
4) Mechanical properties: peeling strength, tensile strength, welding resistance hardness, adhesion;
5) Insulation performance: voltage resistance test, wet heat insulation resistance, CAF resistance test;
6) Welding performance: cleanliness test, weldability test;
7) Corrosion resistance: welding resistance to chemical agents, gold finger porosity.