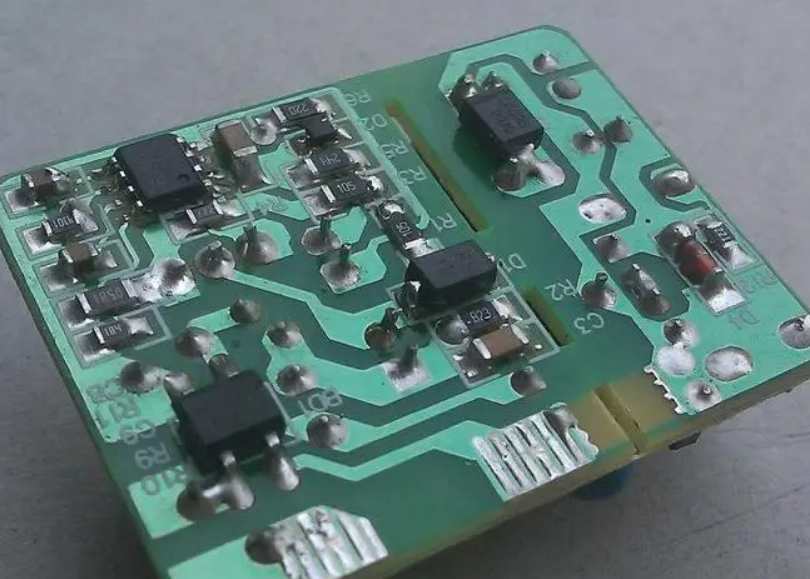
Conduction hole is also known as conduction hole. In order to meet customer requirements, the circuit board must be plugged. Through numerous practices, the traditional aluminum sheet plugging process is changed, and the circuit board surface welding and plugging are completed with white mesh.
The utility of Via hole conduction through the circuit, the progress of the electronic industry, but also enhance the progress of PCB, also put forward higher requirements for the printed board manufacturing process and surface mounting technology. The Via hole plugging process comes into being, and the following requirements should be satisfied:
(1) There is copper in the through hole, and welding resistance can be plugged or not plugged;
(2) through the hole internal tin lead, there is a certain thickness requirements (4 microns), can not have solder resistance ink into the hole, resulting in tin beads in the hole;
(3) the pass-through hole must have solder resistance ink plug hole, light proof, can not have tin ring, tin beads and flat requirements.
With the development of electronic products in the direction of "light, thin, short and small", PCB also advances to the high degree of density and high degree of difficulty. Because the PCB exposed in a large number of SMT and BGA, and customers require plug holes when mounting components, it has five main effects:
(1) Avoid short circuit caused by tin penetrating through the component surface from the passthrough hole during wave soldering of PCB board; Especially when we put the hole on the BGA pad, it is necessary to do the plug hole first, and then gold-plated disposal, easy to burn the BGA welding.
(2) Prevent the flux from remaining in the pass hole;
(3) After the external installation and component assembly of the electronics factory are completed, the PCB should be vacuated on the testing machine to form negative pressure:
(4) Avoid the appearance of solder paste into the hole leading to virtual welding, affecting the installation;
(5) Avoid over wave soldering tin bead pop out, resulting in short circuit.
For the external mounting plate, especially for the mounting of BGA and IC, the plug holes of the pilot holes must be smooth, convex and concave plus or minus 1mil, and the edge of the pilot holes should not be red and tinning; Through hole hiding tin beads, in order to meet customer requirements, through hole plugging process can be said to be various, long process, process control is difficult, from time to time in hot air leveling and green oil soldering resistance experiment oil loss; Problems such as oil explosion occur after curing. Based on the actual conditions of production, various PCB plugging processes are summarized, and a little comparison and discussion are made in the process and advantages and disadvantages:
Note: The office principle of hot air smoothing is to use hot air to remove the appearance of printed circuit board and the parallel wood solder in the hole, the rest of the solder average covered in the welding pad and does not hinder the solder line and appearance seal decoration, is one of the forms of the appearance of printed circuit board disposal.
The process flow is: plate welding resistance →HAL→ plug → curing. Think it is appropriate to use non-plug hole process production, hot air smoothing with aluminum plate or ink screen to complete the customer requirements of all points of the through hole plug hole. Plug hole ink can be photosensitive ink or thermosetting ink, in order to ensure that the wet film color is exactly the same thing, plug hole ink is best considered appropriate and use the same ink with plate expression. This process can ensure that the hot air leveling through the hole does not drop oil, but easily lead to plug hole ink pollution, uneven surface. It is easy for the customer to cause virtual welding when mounting (especially in BGA). So many customers refuse this method.
1. Pattern transfer after plugging, curing and grinding aluminum sheet
This process uses a digital controlled drilling machine to drill out the aluminum sheet that must be plugged, make a screen version, implement the plug hole, ensure that the plug hole through the hole fullness, plug hole ink, plug hole ink can also be used thermosetting ink, its unique place must be hard, natural resin shrinkage change is small, and the hole wall joint force is good. The process flow is as follows: pretreatment → plug → grinding plate → pattern transfer → etching → plate surface welding resistance
This method can ensure that the through-hole plug hole is smooth, and there will be no quality problems such as oil explosion and hole edge oil in hot air leveling. However, this process requires one-time thickening of copper to make the copper thickness of the hole wall meet the customer's standard, because this requires the copper plating of the whole plate to be long, and the performance of the grinding machine to be long, so as to ensure that the natural resin on the copper surface is completely removed and the copper surface is clean and not polluted. Many PCB factories do not have a one-time copper thickening process, and the performance of the facility is not up to the requirements, resulting in the use of this process in PCB factories.
2. Plug the holes with the aluminum sheet and solder the screen face directly
This process uses a digital control drilling machine to drill out the aluminum sheet to plug holes, made of screen plate, installed in the screen printing machine upward plug holes, after the completion of the plug hole parking can not be more than 30 minutes, with 36T screen directly screen face welding, the process is: pre treatment - plug hole - screen printing - pre drying - exposure - development - curing
This process can ensure that the oil cover through the hole is good, the plug hole is smooth, and the wet film color is exactly the same. After hot air leveling, it can ensure that the through hole is not tin, and there is no tin bead in the hole, but it is easy to lead to the solder plate on the ink in the hole after curing, resulting in poor weldability; After hot air leveling, the oil bubbles off the edge of the through hole. It is difficult to produce the choke using this process method when it is considered appropriate. It is necessary for the process engineer to use the special process and parameter ability to ensure the quality of the plug hole when it is considered appropriate.
3. Aluminum sheet plug hole, development, precuring, grinding plate after the plate face welding.
With the digital control drilling machine, drill out the requirements of the plug hole aluminum sheet, made of screen plate, installed in the shift screen printing machine upward plug hole, plug hole must be plump, both sides of the edge is better, and then through curing, grinding plate surface treatment, its process is: pre-treatment - plug hole a pre-drying - development - pre-curing - plate surface welding
Because this process is considered appropriate and the use of plug curing can ensure that HAL hole after the oil off, oil explosion, but HAL, hole hidden tin beads and through the hole on the tin is difficult to absolutely solve, so many customers do not collect.
4.PCB board surface solder and plug holes are completed at the same time.
This method considers appropriate and use 36T (43T) screen, installed on the screen printing machine, consider appropriate and use the plate or nail bed, in the completion of the surface at the same time, will all the through hole plug, its process is: pre treatment - screen printing - pre drying - exposure - development - curing.
This process time is short and the utilization rate of facilities is high, which can ensure that the oil does not drop through the hole after the hot air leveling and the through-hole does not get tin. However, because it is considered appropriate, the silk screen is used to plug the hole. There is a lot of air in the through-hole memory, and during curing, the air expands and breaks through the welding resistance film, resulting in emptiness and ununiformity.