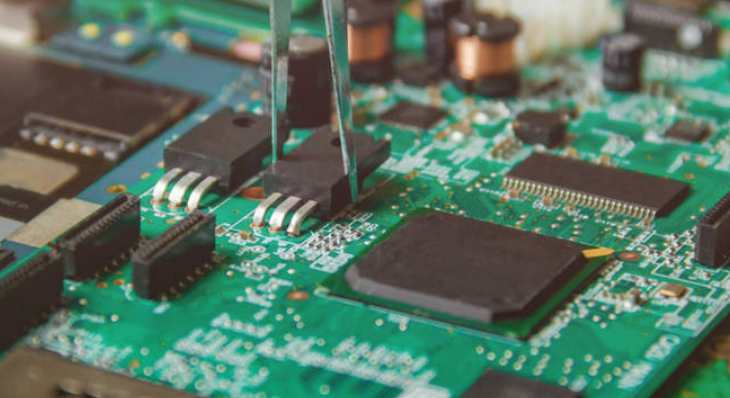
PCB circuit board with insulation board as the base material, cut into a certain size, it is at least attached with a conductive graphic, and cloth holes (such as component holes, fastening holes, metallization holes, etc.), used to replace the chassis of the previous device electronic components, and realize the mutual connection between electronic components.
PCB circuit board repair is a new repair industry. In recent years, the degree of automation of industrial equipment is getting higher and higher, so the number of industrial control board in various industries is also increasing. After the industrial control board is damaged, the high cost required to replace the PCB circuit board (at least thousands of yuan, more than tens of thousands or hundreds of thousands of yuan) has become a very headache for the enterprises. In fact, the vast majority of these damaged PCB circuit boards can be repaired in China, and the cost is only 20%-30% of the purchase of a new board, and the time used is much shorter than that of foreign fixed board. The following introduces the basic knowledge of PCB circuit board maintenance:
Almost all PCB circuit board maintenance without drawing materials, so many people are skeptical about PCB circuit board maintenance, although various circuit boards vary, but the same is that each PCB circuit board is composed of a variety of integrated blocks, resistors, capacitors and other devices, so the PCB circuit board damage must be one or some of the devices damaged, The idea of PCB circuit board maintenance is established based on the above factors. Circuit board maintenance is divided into two parts: inspection and maintenance, among which inspection occupies a very important position. Test the basic knowledge of each component on the PCB circuit board until the bad parts are found and replaced, then a PCB circuit board will be repaired.
PCB circuit board detection is the process of finding, determining and correcting the fault of each electronic component on the PCB circuit board. In fact, the whole testing process is a thinking process and a testing process that provides logical reasoning clues. Therefore, testing engineers must gradually accumulate experience and constantly improve their level in the process of maintenance, testing and overhaul of PCB circuit boards. General electronic equipment is composed of tens of thousands of components, in the maintenance, overhaul, if by direct test and check each component of the PCB circuit board to find the problem will be very time-consuming, implementation is also very difficult. So from the fault phenomenon to the fault cause of the type of check, is an important maintenance method. As long as the detection of the problem, then maintenance is easy.
When testing PCB board, we should pay attention to the following 9 tips to ensure the quality of the product.
01. It is strictly prohibited to test PCB board by using grounded test equipment to contact live TV, audio, video and other equipment on the bottom plate without isolating transformer
It is strictly prohibited to directly test TV, audio, video and other equipment without power isolation transformer with the instrument whose shell has been grounded. Although the general radio recorder has a power transformer, when exposed to the more special especially large output power or the nature of the power supply is not very familiar with the television or audio equipment, first of all to make clear whether the chassis of the machine is live, otherwise it is easy to and floor live TV, audio and other equipment caused by short circuit, ripple integrated circuit, resulting in further expansion of the fault.
02. Testing PCB board should pay attention to the insulation property of electric soldering iron
Do not allow the use of electric soldering iron welding, to confirm that the iron is not charged, it is best to ground the shell of the iron. MOS circuit should be more careful, can use 6~8V low voltage circuit iron is safer.
03. Understand the working principle of integrated circuits and related circuits before testing PCB boards
Before checking and repairing integrated circuit, we should be familiar with the function, internal circuit, main electrical parameters, the role of each pin and the normal voltage, waveform of the pin and the working principle of the circuit composed of peripheral components. If these conditions are in place, analysis and inspection are much easier.
04. Test PCB board do not cause short circuit between pins
When measuring voltage or testing waveform with oscilloscope probe, the stylus or probe should not be short-circuited between the pins of integrated circuit due to sliding. It is better to measure on the peripheral printed circuit directly connected with the pins. Any momentary short circuit can easily damage the IC, and extra care should be taken when testing CMOS integrated circuits in flat packages.
05. Test PCB board test instrument internal resistance should be large
When measuring the DC voltage of integrated circuit pins, use a multimeter with an internal resistance greater than 20 kω /V. Otherwise, there will be a large measurement error for some pins.
06. Testing PCB board should pay attention to the power integrated circuit heat dissipation
The heat dissipation of the power integrated circuit should be good. It is not allowed to work in a high power state without a radiator.
07. Test the PCB lead reasonably
If it is necessary to add peripheral components to replace the damaged part of the integrated circuit, small components should be selected, and the wiring should be reasonable to avoid unnecessary parasitic coupling, especially to deal with the audio power amplifier integrated circuit and the ground terminal between the circuit.
08. PCB board testing to ensure the quality of welding
Welding is really solid, the accumulation of solder, porosity is easy to cause virtual welding. Welding time is generally not more than 3 seconds, the power of the iron should be about 25W internal heat. The soldered integrated circuit should be carefully checked. It is best to use an ohmmeter to measure whether there is short circuit between the pins and confirm that there is no solder adhesion before switching on the power supply.
09. Detection PCB board do not easily determine the damage of integrated circuit
Do not easily judge the integrated circuit has been damaged, because the vast majority of integrated circuits are direct coupling, once a circuit is abnormal, may lead to multiple voltage changes, and these changes are not necessarily caused by the damage of the integrated circuit. In addition, in some cases, when the pin voltage is consistent with or close to the normal value, it may not be able to show that the integrated circuit is good, because some soft faults will not cause changes in DC voltage.