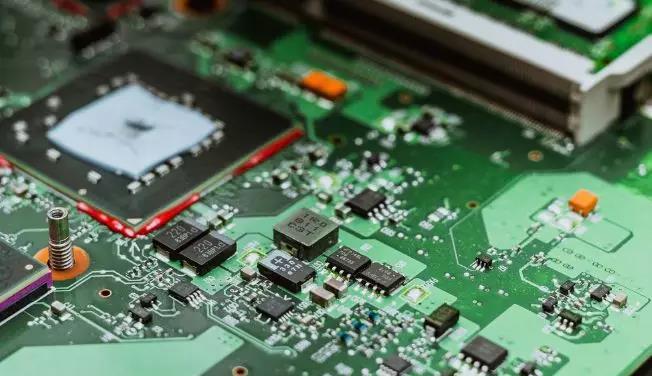
1. Precautions for PCB design
(1) The plate is covered with copper to increase the tension of the layout.
When the length of a plate is more than 80mm and there is no copper, the thickness of the plate is less than 1.0mm.
If the board can not be pressed together, and can not be thickened, use pressure warping.
(2) Hollow area covered with copper, plus the process
When the board hollow position is too much, the board is too big, easy to bend after reflow welding.
In the manufacturing process of printed circuit board, all dielectric layers are evenly distributed among each other. However, it is the uneven distribution of copper layers that causes PCB warping to occur. To prevent warping, design engineers must balance the copper pattern on each layer of the circuit board with the area of the circuit. Design engineers must also balance component layout, assembly distribution, and heat distribution to reduce warping.
For example, if the outermost top surface has a large copper surface, and the outermost bottom surface has very little copper trace line, then the PCB will have a greater tendency to warp after etching. The design engineer must ensure that the two outer line pattern areas match as closely as possible. If the copper area on either side differs greatly, it may be advisable for the designer to add a separate copper grid on the thin side to balance the two.
Suggestions: Copper plating in the hollow area to reduce the warpage of the board; In addition, if the inside of the board does not affect the function, also want to lay copper; The last suggestion is to add the process edge and lay copper along the process edge.
(3) The core board and PP board are the same brand
The core of the multilayer board and the PP board must be the same brand, otherwise the board will warp.
For example, 6-layer plate pp sheet asymmetry: 2-3 core board pp sheet thin, 4-5 core board pp sheet thick, so that a pressure is warped out. Therefore, the core plate and PP sheet must be the same brand, to ensure consistent thickness, to ensure the symmetry of multilayer PP sheet.
(4) The arrangement of layer prepreg should be symmetrical
The manufacturer must ensure that the arrangement of prepregs between layers remains symmetrical. For example, for six-ply slabs, it is best to have the same thickness between 1-2 layers and 5-6 layers, including the number of prepreg sheets. This will prevent warping after laminating.
Maintain symmetry
2. Matters needing attention during PCB processing
(1) PCB before cutting
The purpose of baking the PCB circuit board(150℃ for 8±2 hours) before cutting the copper clad plate is to remove the moisture in the board, while fully curing the resin in the board, further eliminating the residual stress in the board, which is useful for preventing the board from warping.
At present, many double-sided, multilayer plates still adhere to the baking steps before or after blanking. However, some plate factories also have exceptions. At present, the drying time of PCB factory is also inconsistent, ranging from 4 to 10 hours. It is recommended to decide according to the grade of printed board produced and the customer's warping requirements.
Either cut the whole piece into a jigsaw puzzle or cut it out and bake it, either way is possible. It is recommended to cut the back plate and bake the inner plate as well.
(2) longitude and latitude of prepreg
After prepreg laminating, the warp and weft shrinkage rate is different. When blanking and laminating, the warp and weft direction must be distinguished, otherwise it is easy to cause the warping of the finished plate after laminating, and it is difficult to correct even if the pressure is applied to the baking plate.
Many reasons for the warping of multilayer plates are due to the lamination of prepreg in the direction of longitude and latitude did not distinguish, piled up at will.
How do you tell latitude and longitude? The rolling direction of the prepreg is meridional and the width direction is zonal. For copper foil, the long side is zonal and the short side is meridional. Check with your manufacturer or supplier if you're not sure.
(3) Stress relief after fitting
After hot and cold pressing, the burrs are removed, cut or milled, and then placed flat in an oven at 150℃ for 4 hours to gradually release the stress in the plate and fully cure the resin. This step cannot be neglected.
(4) The sheet shall be straightened during electroplating
When 0.4 ~ 0.6mm ultra-thin multilayer plate is used for surface plating and pattern plating, special clamping roller should be made. After clamping the sheet to the clamping roll on the automatic plating line, the whole clamping roll is clamped with a round rod. String the rollers together and straighten all the plates on the rollers so that the plates will not deform after plating.
Without this measure, after plating 20 to 30um of copper, the plate will bend and be difficult to remedy.
(5) Cooling of the board after hot air leveling
PCB with hot air leveling, will be affected by the high temperature of the solder groove (about 250℃). After removal, it should be placed on the flat marble or steel plate for natural cooling, and then sent to the afterprocessor for cleaning, which is conducive to prevent the warping of the circuit board.
In order to improve the brightness of the lead tin surface, some factories put the board into cold water immediately after hot air leveling, and take it out after a few seconds for post-treatment. This hot and cold shock can cause certain types of circuit boards to warp. Twist, layer, or blister.
In addition, an air float bed can be installed on the equipment for cooling.
PCB warping repair method
1. PCB warping repair in PCB process
In the PCB process, the board with large warpage is picked out and levelled by the roller leveler and then proceeded to the next process. Many PCB manufacturers consider this practice to be effective in reducing the warpage rate of PCB finished boards.
2, PCB finished board warping repair
As for the finished product, the warping is obviously out of tolerance and cannot be levelled by roller leveler. Some PCB factories put it into a small press (or similar fixture) to press the warped PCB board and leave it for a few hours to ten hours for cold pressing and flattening. In practical terms, the effect of this practice is not very obvious. One is that the leveling effect is not large, and the second is that the flattened board is easy to bounce back (i.e. warpage recovery).
Some PCB factories will heat the small press to a certain temperature, and then press the flat PCB board hot, the effect will be better than cold pressing, but too much pressure will lead to wire deformation; If the temperature is too high, it will produce defects such as rosin discoloration and discoloration. Moreover, whether it is cold or hot pressing, it takes a long time (several hours to more than ten hours) to see the effect, and the PCB board after flattening has a high percentage of warpage rebound.
The hot stamping and flattening method of the bow die is recommended here. Use a simple bow mold according to the PCB area to be leveled.
(1) Clamp the warped PCB board into the bow mold and put it into the oven for baking and leveling:
The curved PCB board is bent facing the curved surface of the mold, and the fixture screws are adjusted to make the PCB board deformed and warped in the opposite direction. Then the mold with the PCB board is heated in the oven to a certain temperature for baking, baking for a while. Under the heating condition, the stress of the substrate gradually relaxes and the deformed PCB board returns to the flat state. But the baking temperature should not be too high, so as to avoid rosin discoloration or substrate yellow. However, the temperature should not be too low, and it takes a long time to completely relax the stress at a low temperature.
Generally, the glass transition temperature of the substrate can be used as a reference temperature for baking. The glass transition temperature is the phase transition point of the resin. At this temperature, the polymer chain segments can be rearranged so that the stress of the substrate is fully relaxed.
Because the flattening effect is obvious, the advantage of flattening with a bow mold is that the investment is small. Ovens are available at PCB factories. Leveling is very simple. If the number of warps is large, make a few bow molds is enough. You can put them in the oven once. Fewer molds, short drying time (dozens of minutes), so the leveling efficiency is relatively high.
(2) The PCB board is softened and then clamped into the bow mold for flattening:
For the PCB board with small warping deformation, the PCB board to be levelled can be placed in the oven which has been heated to a certain temperature (that is, the temperature setting can be determined by referring to the glass transition temperature of the substrate, the substrate is baked in the oven for a certain time, and the softening situation is determined by observation. General glass fiber cloth substrate baking temperature is higher, the baking temperature of paper substrate can be lower; The baking temperature can be slightly higher for thick plates and slightly lower for thin plates.
PCB board sprayed with rosin, baking temperature should not be too high. Bake for a certain time, and then take a few to a dozen pieces, clip into the bow mold, adjust the pressure screws, and make the PCB board slightly warped, the opposite direction deformation. After the board is cooled and shaped, the mold can be removed and the flattened PCB board can be taken out.
Low warpage of PCB board after bow molding; Even after wave soldering can basically maintain the smooth state; It also has little influence on the appearance color of PCB board.
PCB board warping is a headache for PCB manufacturers. It not only reduces production, but also affects delivery time. If the curved die is used for hot leveling, and the leveling process is reasonable and appropriate, the warped PCB board can be leveled and the delivery time problem can be solved.