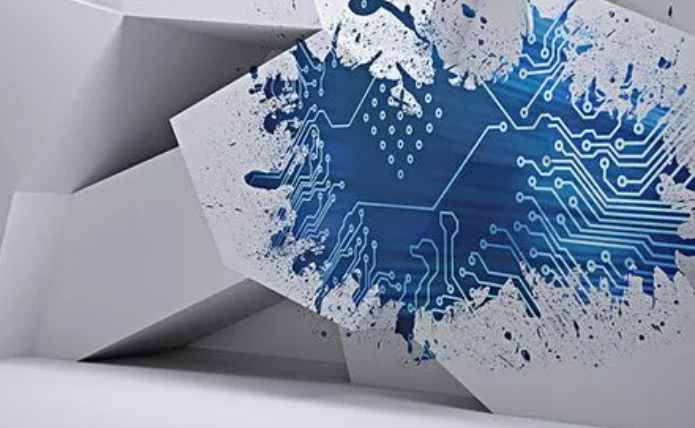
PCBA proofing refers to the trial production of printed circuit boards before batch production. The main application is the process of small batch trial production to the Circuit board factory after the electronic engineer has planned the circuit and completed the production of PCBA, that is, PCBA proofing. The following is to introduce what preparatory work needs to be done before PCBA proofing.
PCBA board is simple and messy, simple PCB board since it is not necessary to say that proofing is very easy, but if it is messy circuit board proofing should be careful, if in the process of PCBA proofing without relevant detection tools detection, if there is a problem, such as PCB board is found to be late. Therefore, we must do a good job of preparation before proofing.
PCBA needs to do preparatory work before making samples
1. Physical border production
The closed physical frame is a basic channel for the future component layout and PCBA proofing. We must pay attention to accuracy. Moreover, it is best to use the arc in the corner, which can not only avoid being scratched by sharp corners, but also reduce the stress effect.
2. Introduce components and networks, and lay out components
When PCBA proofing the components and network to draw a good border must be carefully according to the prompts to operate, including the packaging form of components, component network problems. Because of the contrast, it is not easy to produce problems. In PCBA proofing layout components and wiring on product life, stability, electromagnetic compatibility have a great impact, should be paid special attention to the local. Generally speaking, there should be the following principles: placing order, pay attention to heat dissipation.
3. PCBA planning and wiring, adjustment and improvement
In PCBA planning wiring, it is best to pay attention to the requirements of processing parameters, or to the trusted PCBA proofing manufacturers, the defective rate will be greatly reduced. After the end of PCB planning and wiring, what to do is to make some adjustments to the text, individual components, wiring and copper (this operation should not be too early, otherwise it will affect the speed, and bring trouble to PCB planning and wiring), also in order to facilitate production, debugging, maintenance.
4. Check the network
Sometimes, due to misoperation or neglect, the network connection of the PCB board drawn is different from the schematic diagram, so it is necessary to check. So after the drawing should be done first check, and then carry out the follow-up work.
Electronic equipment is now more and more, a lot of things are developing towards the direction of intelligence, which requires more circuit boards to accept the control system of these devices, and the quality of PCBA determines the service life of the equipment. Each stage in the process of PCBA processing and assembly, including the printing of solder paste on the circuit board, the installation of components, welding, inspection and testing. All of these processes are required for requirements monitoring to ensure the highest quality PCBA products are produced. Now almost all PCBA processing and assembly use appearance mounting skills, the following is to introduce the PCBA processing and assembly process.
PCBA processing and assembly process
1. Solder paste printing
Before adding a component to the board, solder paste needs to be added to the board where solder paste is needed. These areas are generally component pads. This is achieved through the solder screen.
Solder paste is a paste made of small tin particles mixed with flux. This can be piled into place in a process, which is very similar to some printing processes.
Using solder screen, placed directly on the circuit board, and registered in the correct orientation, a runner through the screen to move, squeeze a small piece of solder paste through the screen hole, and onto the circuit board. Since the tin plate is taken from the printed circuit board file, the tin plate has holes in the orientation of the tin pad so that the solder only accumulates on the tin pad.
It is necessary to control the amount of solder buildup to ensure that the joint has the correct amount of solder.
In this part of the PCBA processing and assembly process, the solder paste board is added and then enter the SMT patch process. Here, a machine loaded with reels of components picks them from a reel or other dispenser and places them in the correct orientation on the board.
The tension of the solder paste holds the components placed on the circuit board in place. That's enough to keep them in position, provided the board doesn't vibrate.
In some PCBA processing and assembly process, take and place the machine will add a small glue, the components fixed on the board. However, this is generally only done when the plate is wave-welded. The downside to this process is that any correction is made more difficult by the glue, although some glue is programmed to degrade during the welding process.
The position and component information required for planning the machine is derived from the printed circuit board planning information. This makes pick and place programming much simpler.
Step 3 Weld
Once the component is added to the circuit board, the next stage of PCBA machining assembly, the production process is through it's welding machine. Although some plates may pass through wave soldering machines, this process is not widely used for external mount components these days. If wave welding is selected, then the plate does not add solder paste, because the solder is supplied by the wave welding machine. Reflow skills are more widely used than wave soldering skills.
View: After the circuit board through the welding process, generally to view. Manual viewing is not an option for exterior mounting boards that use 100 or more components. Instead, active optical detection is a more viable solution. Existing machines are able to look at the board and find bad joints, misaligned components, and in some cases, faulty components.
4. PCBA test
It is necessary to test electronic PCBA products before they leave the factory. There are several ways to check them.
In order to ensure the smooth running of PCBA manufacturing process, it is necessary to test the quality of the output products. This is done by studying any faults detected. The ideal place is in the optical viewing stage, as this generally occurs immediately after the welding stage. This means that process shortcomings can be detected quickly and corrected before too many boards with the same problem are manufactured.