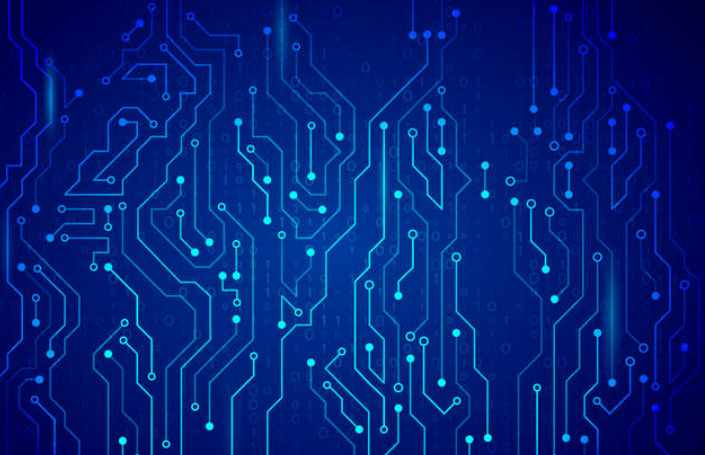
Yes, PCB circuit boards must be impedance. Here are four reasons:
1, pcb line (bottom of the board) to consider plug installation of electronic components, plug into the electrical performance and signal transmission performance, so it will require the lower the impedance, the better, resistivity is lower than 1&TImes per square centimeter; Below 10-6.
2, pcb circuit board in the production process to experience copper sinking, electroplating tin (or electroless plating, or hot spray tin), solder joints and other processes, and the materials used in these links must ensure the resistivity bottom, in order to ensure that the overall impedance of the circuit board is low to meet the product quality requirements, can operate normally.
3, the tin plating of pcb circuit board is the most prone to problems in the production of the whole circuit board, is the key link affecting the impedance. The biggest defect of electroless tin layer is easy to change color (easy oxidation or delixing), poor brazing, which will lead to the welding of the circuit board, high impedance leading to poor conductivity or instability of the whole board performance.
4, pcb circuit board in the conductor will have a variety of signal transmission, when to improve its transmission rate and must improve its frequency, the line itself if the etching, laminated thickness, wire width and other factors are different, will cause impedance value change, so that the signal distortion, resulting in circuit board performance decline, so it is necessary to control the impedance value in a certain range.
The above general information provided by Suzhou Weya, detailed information can be called letter consultation. Weya - Suzhou professional pcb intelligent manufacturing factory.
The harm of finger contact PCB is briefly introduced
As a pcb engineer, it is inevitable to touch the PCB board with hands in the process of work, which may bring serious consequences, resulting in bad scrap of pcb and reduced reliability of end users. Therefore, staff should develop the habit of wearing gloves, which can reduce the harm of direct contact with pcb board. The following is a brief introduction of a hand printing will lead to bad pcb board reasons, hazards, and how to avoid.
1, finger print with hand sweat stains, its main components are water, inorganic salts, fats, oils and cosmetics and skin care products and other pollutants.
2. Harm of finger printing in PCB manufacturing process
A. The bare object touching the plate causes chemical reactions on the copper surface in A very short time, resulting in oxidation of the copper surface. After a little longer, there are obvious fingerprints after electroplating, uneven coating, causing serious bad appearance of the product.
B. Bare hand contact plate before welding resistance will lead to poor adhesion of green oil under welding resistance, which will bubble and fall off during hot air conditioning.
C. In the process of gold plate from welding resistance to packaging, touching the surface with bare hands will lead to unclean surface, resulting in poor weldability or poor bonding.
D, printing wet film or silk screen line and the board surface before pressing film with fingerprint grease, easy to cause dry/wet film adhesion decline, resulting in plating and plating separation, gold plate is easy to cause the board pattern, after the completion of the solder resistance production, the board surface oxidation, Yin and Yang color.
If the above phenomenon is not eliminated, it will damage the qualified rate and one-time pass rate of products, resulting in long production and processing cycle, high rework and replenishment rate, and low on-time delivery rate.
3. Put an end to bare hand contact plate
A. Take gloves and finger covers with you, and develop a good habit of taking and putting pcb board
B. Wear gloves (such as cloth gloves, rubber gloves, finger gloves, etc.) when gloves can be worn.
A lot of people who are new to impedance have this question, why is it that the common single-ended in-board wiring is controlled by default at 50 ohm instead of 40 ohm or 60 ohm? This is a deceptively simple question that is difficult to answer. Before writing this article, we have also looked up a lot of materials, among which the most well-known is Howard Johnson, PhD's reply on this question, which I believe many people have read.
Why is it so hard to answer? Signal integrity itself is a trade-off, so the best known is "It depends..." This is a question for which there is no right answer and which varies from person to person. Today, Mr. Gao Speed also summarizes the various responses to this question. Here, he also throws out the jade, hoping that more people can summarize more relevant factors from their own perspectives.
First of all, 50 ohms has some history, starting with standard cables. As we all know, a large part of modern electronic technology originated in the military, which gradually became civilian. In the early days of microwave application, during World War II, impedance selection was completely dependent on the needs of use. As technology advances, impedance standards need to be given in order to strike a balance between economy and convenience. In the United States, the most commonly used guides are made from existing measuring rods and pipes. 51.5 ohms are common, but adapters/converters are seen and used from 50 ohms to 51.5 ohms; To unite the Army and Navy in solving these problems, an organization called JAN, later DESC, developed by MIL, took into account the choice of 50 ohm, and a special conduit was created that became the standard for various cables. At this point the European standard was 60 ohms, and before long, under the influence of dominant companies like Hewlett-Packard, the Europeans were forced to change, so that 50 ohms eventually became a standard in the industry, and it became the norm, and pcb's connected to various cables, in order to match impedance, Finally, the 50 ohm impedance standard is required.
Secondly, from the point of view of circuit board production can be realized, 50 ohm is more convenient to realize. As can be seen from the previous impedance calculation formula, low impedance requires a wide line width and thin medium (or large dielectric constant), which is difficult to meet in space for the current high-density plate. Too high impedance and need a thin line width and thicker medium (or small dielectric constant), is not conducive to EMI and crosstalk suppression, at the same time for multilayer plate and from the point of view of mass production processing reliability will be relatively poor; The common line width and medium thickness of 50 ohm in the environment of common materials (4~6mil) is in line with the design requirements (as shown in the figure 1 impedance calculation), and convenient processing, slowly become the default choice is not surprising.