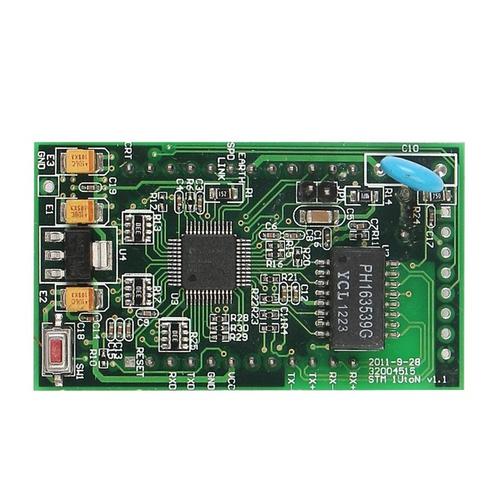
How to avoid electromagnetic interference effectively in the process of PCB processing and design? Anti-interference is a very important part of modern PCB design, which directly reflects the performance and reliability of the whole system. For PCB design engineer, anti-interference design is the key and difficult point that we must master.
One, the existence of interference in PCB board
In the actual study, it is found that there are four main interference in PCB board design: power supply noise, transmission line interference, coupling and electromagnetic interference (EMI).
1. Power supply noise
In high frequency circuit, power supply noise has obvious influence on high frequency signal. So, first of all, the power supply requires low noise. A clean floor is just as important here as a clean power source.
2. Transmission lines
There are only two types of transmission lines in printed circuit board: strip line, microwave line and transmission line. The big problem is reflexes, which can cause a lot of problems. For example, the load signal will be the superposition of the original signal and the echo signal, which will increase the difficulty of signal analysis; Reflection can cause return loss, which affects the signal as seriously as additive noise interference.
3. Coupling
The interference signal generated by the interference source causes electromagnetic interference to the electronic control system through a certain coupling channel.
The coupling mode of interference is nothing more than through wires, space, public lines, etc. acting on the electronic control system. The analysis mainly includes the following types: direct coupling, common impedance coupling, capacitance coupling, electromagnetic induction coupling, radiation coupling, etc.
4. Electromagnetic interference
Electromagnetic interference EMI includes conduction interference and radiation interference. Conducted interference is when signals are coupled (interfered) from one grid to another through conducting media.
Radiative interference means that the interference source couplings (interferes) its signal through space to another grid.
In the design of high-speed PCBS and systems, high-frequency signal lines, pins of integrated circuits and various connectors may become radiation interference sources with antenna characteristics, which will emit electromagnetic waves and affect the normal work of other systems or subsystems in the system.
Two, PCB design anti-interference measures
The anti-jamming design of printed circuit board is closely related to specific circuit. Next, we only explain some common PCB anti-interference design measures.
1. Power line design
According to the current of the printed circuit board, try to rent the width of the power cord, reduce the circuit resistance. Meanwhile, the direction of the power cable and ground cable is consistent with the direction of data transmission, which helps to enhance the anti-noise capability.
2.PCB design ground wire design principle
(1) digital and analog separation. If there are both logical and linear circuits on the circuit board, they should be separated as far as possible. Low-frequency circuits should be grounded in single parallel as far as possible. If the actual connection is difficult, it can be grounded in series and then in parallel. The high-frequency circuit should be grounded in series by multiple points, the grounding wire should be short and rented, and the grid large area grounding foil should be used around the high-frequency components as far as possible.
(2) The ground cable should be as thick as possible. If the grounding wire is made of very thin wire, the grounding potential will change as the current changes, reducing the noise resistance. Therefore, the ground wire should be thickened to allow it to pass through three times the allowable current on the printed circuit board. If possible, the ground cable should be more than 2 to 3 mm.
(3) The ground wire forms a closed loop. For printed boards consisting only of digital circuits, the noise resistance can be improved by arranging the ground circuits of the digital circuits into group loops.
3. Configure the decoupling capacitor
One of the common practices of PCB design is to configure appropriate decoupling capacitors in all key parts of the PCB. The general configuration principles of decoupling capacitors are:
(1) The power input terminal is connected with a 10 ~100uf electrolytic capacitor. If possible, connect over 100uF.
(2) In principle, each IC chip should be equipped with a 0.01pF ceramic chip capacitor. When the PCB gap is insufficient, every 4-8 chips can be equipped with a tantalum capacitor of 1-10pf.
(3) For devices with weak anti-noise ability and large power change during shutdown, such as RAM and ROM memory devices, the decoupling capacitor should be directly connected between the power cord and ground wire of the chip.
(4) The capacitor lead should not be too long, especially the high-frequency bypass capacitor should not have a lead.
4. Methods of eliminating electromagnetic interference in PCB design
(1) Reduce loops: Each loop is equivalent to an antenna, so we need to minimize the number of loops, the area of loops and the antenna effect of loops. The guarantee signal has only one loop... At any two points, avoid artificial cycling and use the power layer as much as possible.
(2) Filtering: EMI can be reduced by filtering the power line and signal line in three ways: decoupling capacitor, EMI filter and magnetic element.
(3) Shielding.
(4) Reduce the speed of high-frequency devices as much as possible.
(5) Increasing the dielectric constant of PCB board can prevent high-frequency parts such as the transmission line near the board from radiating outward; Increasing the thickness of the PCB board and minimizing the thickness of the microstrip line can prevent the leakage and radiation of the electromagnetic line