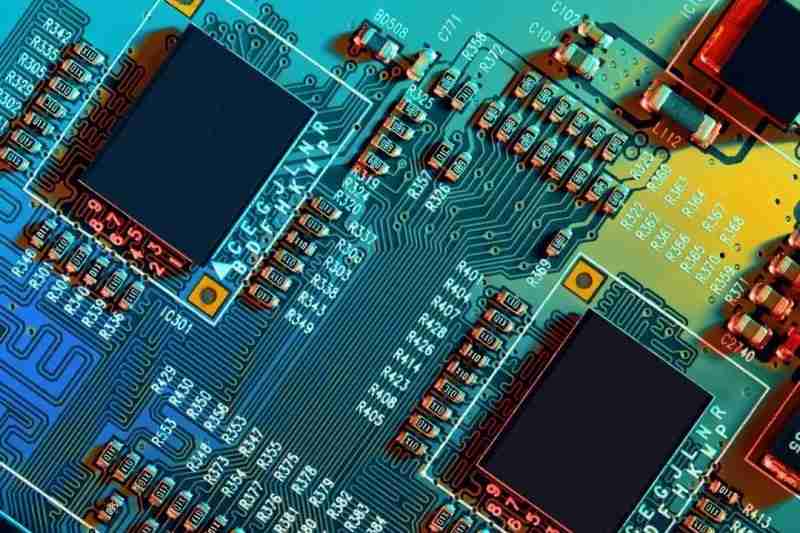
(1) double-head ultraviolet drilling system;
(2) double-ended CO2 laser drilling system;
(3) Stick laser drilling system (CO2 and UV).
All of these types of drilling systems have their own advantages and disadvantages. Laser drilling systems can be simply divided into two types, two bit single wavelength system and two bit dual wavelength system. Regardless of the type, there are two main components that affect the ability to drill:
(1) laser energy/pulse energy;
(2) Beam positioning system.
The energy of the laser pulse and the transmission efficiency of the beam determine the drilling time, which refers to the time for the laser drilling machine to drill a micro-through hole, and the beam positioning system determines the speed of movement between the two holes. These factors together determine the velocity of the laser drilling mechanism for the given requirements of the microhole. The dual-head UV laser system is most suitable for drilling holes smaller than 90μm in integrated circuits and has a high aspect ratio.
The double-ended CO2 laser system uses Q-switched RF excited CO2 laser. The main advantages of this system are high repeatability up to 100kHz, short drilling time, wide operating surface, and few shots required to drill a blind hole, but with lower drilling quality.
The most commonly used two-head laser drilling system is the hybrid laser drilling system, which consists of an ultraviolet laser head and a CO2 laser head. This integrated hybrid laser drilling method can be used to drill copper and dielectric simultaneously. The copper is drilled with ultraviolet light to generate the size and shape of the desired hole, followed by an unmasked dielectric drilled with a CO 2 laser. The drilling process is accomplished by drilling a 2in X 2in block called a domain.
The CO2 laser effectively removes dielectric, even non-uniform glass reinforced dielectric. However, a single CO2 laser cannot create small holes (less than 75μm) and remove copper, with a few exceptions, it can remove thin pretreated copper foils below 5μm. Uv lasers can create very small holes and remove all ordinary copper street (3-36μm, 1oz, even electroplated copper foil). Ultraviolet lasers can also remove dielectric materials alone, though at a slower rate. Also, for non-uniform materials, such as reinforced glass FR-4, the results are often poor. This is because the glass can only be removed if the energy density is raised to a certain extent, which will also destroy the inner pad. Because the stick laser system includes ultraviolet laser and CO 2 laser, so it can achieve the best in both areas, with ultraviolet laser can complete all the copper foil and small holes, with CO 2 laser can quickly drill the dielectric. The structure diagram of a dual-head laser drilling system with programmable drilling spacing is presented. The spacing between the two bits can be adjusted according to the layout of the components, which ensures maximum laser drilling capability.
Today, most dual-head laser drilling systems have a fixed distance between the two bits and step-repeat beam positioning technology. The advantage of the step-repeat laser remote regulator itself is that the modulation range of the domain is large (50 X 50)μm. The disadvantage is that the laser remote regulator must be moved in steps in a fixed field, and the spacing between the two bits is fixed. A typical two-headed laser remote regulator has a fixed distance between the two bits (approximately 150μm). For different panel sizes, fixed-distance bits do not operate as optimally as programmable spacing bits.
Today, dual-head laser drilling systems are available in a variety of specifications and are suitable for both small PCB manufacturers and high volume printed circuit board manufacturers.