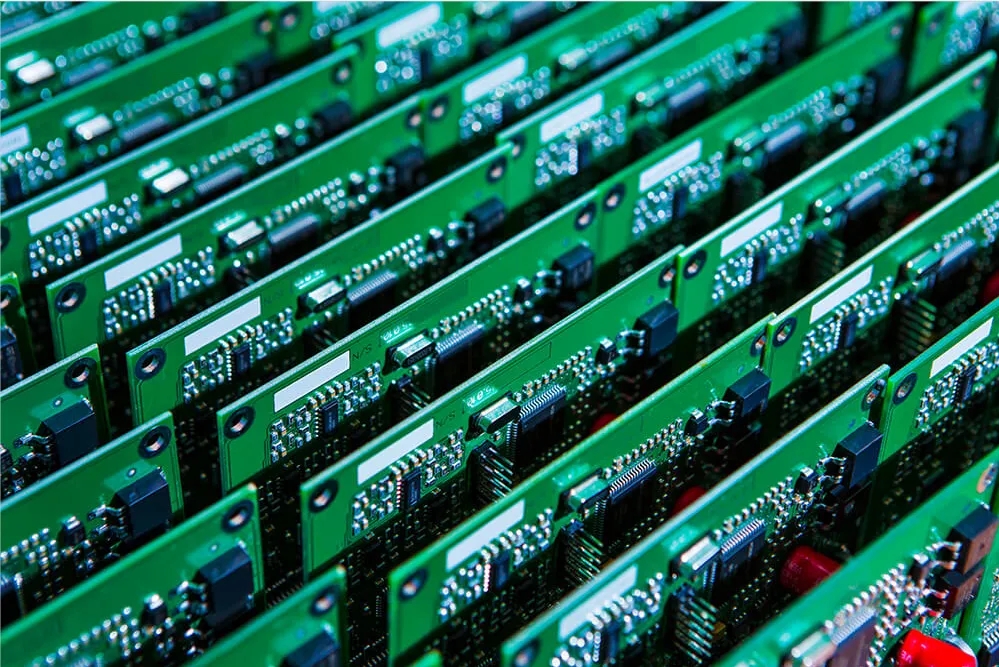
Current Situation and Development Trend of PCB Microhole Processing Technology
PCB manufacturing, PCB design and PCBA processing manufacturers will explain the status quo and development trend of PCB microporous processing technology
This paper introduces the characteristics, current situation and future development trend of the three most widely used PCB micro hole processing technologies (mechanical drilling, CO2 laser drilling, UV laser drilling).
Keywords | PCB; Micropore processing; Mechanical drilling; CO2 laser drilling; UV laser drilling
1、 Introduction
The main function of holes in PCB is to realize interconnection between layers or install components. PCB industry often divides holes into electroplated holes and non electroplated holes according to whether they are conductive or not; The holes are divided into through holes, blind holes and embedded holes according to whether the plate is drilled through or not.
The hole forming methods used in the PCB industry include: mechanical drilling, mechanical punching, laser drilling, photoinduced drilling, chemical etching, plasma etching, jet sand blasting, conductive column drilling, insulation replacement, conductive bonding sheet, etc. The relatively widely used and mature hole forming technologies include: mechanical drilling and laser drilling (CO2 laser and UV laser).
As far as the current technological development of PCB is concerned, it can be called microporous if the aperture is 0.25mm or less. For micro hole drilling, there are three commonly used methods: mechanical drilling, CO2 laser drilling and UV laser drilling (generally, mechanical drilling is used for through holes with an aperture of 0.1mm and above, and laser drilling is used for blind holes with an aperture of 0.1mm and below). This paper mainly introduces these three micro hole drilling technologies.
2、 Mechanical drilling micro hole technology
The main characteristics of mechanical drilling are: high-speed machining (the highest speed reaches 350000 rpm), and the hole shape (if the hole wall roughness is generally controlled at ≤ 30 μ m) Aperture (if the aperture tolerance is generally controlled at ≤+10 μ m/-40 μ m) And hole position (if the hole position accuracy is generally controlled within ≤± 50 μ m) High quality requirements. The schematic diagram of mechanical drilling is shown in the figure below.
2.1 Materials
The main materials used for mechanical drilling of micro holes are: drill bits (also known as drill bits, drill needles, drill nozzles), cover plates (also known as panels), and base plates (also known as baseplates).
2.1.1 Drill bit
The drill is a cutting tool used in the process of mechanical drilling. Drill bits for PCB are generally made of tungsten cobalt alloy (hard alloy material). The alloy is made of tungsten carbide (WC) powder (90~94%) as the matrix, cobalt (Co) (6~10%) as the binder, and sintered at high temperature and high pressure. It has high hardness (mainly from WC) and high wear resistance.
The development trend of microporous bit is that WC particle size changes from 0.3~0.2 μ The m direction is reduced to nanometer level, the structure is changed from double chip discharge to single chip discharge, and the drill point angle is increased to improve the torque resistance, improve the toughness and ensure the requirements of rigidity.
At present, the diameter specifications of commonly used microporous drills for PCB are generally 0.1, 0.15, 0.2 and 0.25mm (there are also 0.05mm and 0.075mm, but there are few actual mass production applications, as shown in Figure 3); Bit shank diameter is generally adopted Φ 2.0mm, also used Φ 3.175mm (conventional drill shank diameter is generally Φ 3.175mm); The bit edge is mostly UC type (the bit edge is grinded to reduce the friction between the edge and the hole wall); In order to disperse the stress concentration phenomenon of the micro hole drill bit, a buffer section is generally added between the drill handle and the cutting edge to form a stepped type, as shown in Figure 4.
The following five parameters should be paid attention to when machining micro holes:
(1) Speed/cutting speed
Speed: the number of revolutions of the spindle per minute; Cutting speed: cutting distance per minute
(2) Feed speed/feed quantity
Feed speed: the distance of spindle descending per minute; Feed amount: the drilling distance for each rotation of the spindle
(3) RETURN SPEED RETURN SPEED: The distance that the spindle lifts per minute
(4) Number of laminated plates
The factors affecting the number of laminated plates are: number of layers, thickness, minimum hole diameter, hole location tolerance requirements, inner copper thickness, hole ring, etc. The number of layers, thickness and minimum hole diameter of the plate shall be mainly concerned.
(5) Bit status
The bit status includes the number of grinding times and the number of holes drilled. With the increase of the grinding times of the microporous bit, the drilling quality will gradually become worse, so the number of drilling holes needs to be reduced. Because microporous bits are difficult to grind (especially 0.1 and 0.15 mm bits), PCB manufacturers generally scrap them once they use them (you can increase the number of holes drilled by adjusting the drilling parameters).
3、 Laser drilling micro hole technology
The main reasons for the rise of laser drilling are: the development trend of dense, thin and flat PCBs (reducing through holes and increasing blind holes is the most effective way to improve the density); The machining of micro blind holes cannot be rapidly and stably mass produced by mechanical drilling.
The main characteristics of laser drilling are: optical processing (CO2 laser or UV laser), hole shape (such as hole wall roughness is generally controlled at ≤ 18 μ m) Hole diameter (if the hole diameter tolerance is generally controlled within ≤± 20 μ m) And hole position (if the hole position accuracy is generally controlled at ≤± 20 μ m) High quality requirements.
In fact, the term "laser drilling" is not accurate. The exact term should be "laser drilling" (mainly optical processing). Since the industry is generally called "laser drilling", this article is also called "laser drilling".
At present, there are two types of laser drilling rigs commonly used in PCB industry: CO2 and UV laser drilling rigs. Most of the CO2 laser drilling rigs are double axis and double table type (using time-sharing or light splitting method to transform one laser beam into two lasers to process two boards at the same time to improve processing efficiency).
The main processing parameters of CO2 laser drilling are: beam diameter, pulse width and pulse number; The main processing parameters of UV laser drilling include: beam moving speed and walking track, number of turns, laser frequency and laser power (relatively complex). PCB manufacturing, PCB design and PCBA processing manufacturers will explain the current situation and development trend of PCB microporous processing technology.