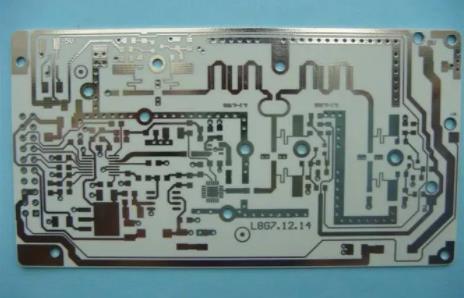
Skin effect of high frequency plate and dielectric thickness and high frequency structure
circuit board manufacturing, circuit board design and PCBA processing manufacturers will explain the skin effect of high-frequency boards, dielectric thickness and high-frequency structure
The conductor loss of the circuit will increase with the increase of frequency. At low frequency, the current on the conductor is almost uniformly distributed inside the conductor; But at high frequency, alternating current or alternating electromagnetic field appears in the conductor. At this time, the current distribution inside the conductor changes, and the current is mainly concentrated in the thin layer on the surface of the conductor. The closer to the conductor surface, the greater the current density, while the current inside the conductor is very small or even no current, as shown in the figure. As a result, the resistance of the conductor increases, and the conductor loss also increases. This phenomenon is called skin effect.
Generally, in the process of PCB substrate processing, in order to make the copper foil firmly stick to different dielectric materials, the copper foil surface will be roughened to improve its adhesion with PCB dielectric materials. Most PCB substrates will be laminated with several forms of copper foil conductors, including standard electrolytic copper, reverse treated copper and rolled copper. In brief, the standard ED copper is formed by electrolysis of copper ions in copper sulfate solution onto a slowly rolling drum of polished stainless steel. The surface roughness of copper in direct contact with polished stainless steel drum is smooth, but that of copper in direct contact with solution is much rougher. The calendered copper foil is obtained by rolling the copper block with a roller mill. Continuous rolling with a roller can obtain copper foil with good consistency in thickness and smooth surface. RT copper foil also belongs to electrolytic copper, which is formed by pressing the smooth surface of the copper foil with the substrate.
Different copper foils have different surface roughness, and there are many measurement methods and measurement units to characterize the surface roughness of copper foils. For RF microwave applications, Rq or RMS (root mean square) value is a more reasonable roughness characterization method. The surfaces of different copper foils show completely different particle and roughness characteristics. Figures a and b show the surface characteristics of the interface with the medium of two typical copper foil standard ED copper and calendered copper; C List the typical surface roughness values of several common copper foils. It can be seen that the surface roughness of standard electrolytic copper foil is relatively high, and the typical RMS value is 2.2um; However, the surface roughness of rolled copper foil is very small, and the typical RMS value is only 0.3um.
Different surface roughness of copper foil will produce different parasitic inductance, which will lead to the change of surface impedance of copper foil, resulting in different conductor losses. In general, when the skin depth corresponding to the circuit operating frequency is less than or equal to the surface roughness of copper foil, the influence of surface roughness will become very significant. As shown in the figure, a microstrip line is designed on the same circuit material of 5mil Rogers RO3003TM to test its insertion loss. When the frequency is<1GHz, the skin depth is 2.09um, which is greater than the standard electrolytic copper roughness of 1.6um and the calendered copper roughness of 0.3um. The insertion loss difference between the two copper foil circuits is not obvious; When the frequency increases gradually, the insertion loss of standard electrolytic copper and calendered copper shows a significant difference. Therefore, the selection of copper foil with low roughness is conducive to reducing insertion loss, especially in the microwave and millimeter wave band.
2. Dielectric thickness of high-frequency plate
The dielectric thickness of the circuit material also affects the conductor loss of the circuit. The data curve in the figure is simulated by MWI application software developed by Rogers based on Hammerstad and Jenson models. The software can accurately calculate the impedance and insertion loss of microstrip transmission lines, and the simulation results are in good agreement with the measured values.
It can be clearly seen from the figure that the 50 Ω microstrip line on RO4835TM thermosetting material based on Rogers with different thicknesses of 6.6mil, 10mil and 30mil has the maximum conductor loss at 6.6mil and the minimum conductor loss at 30mil; As a result, the total insertion loss of circuits with the same frequency decreases with the increase of the dielectric thickness.
On the one hand, this change in conductor loss due to different thicknesses is due to different linewidths of the same 50 Ω microstrip lines with different thicknesses. On the other hand, copper foil roughness has different effects on conductor loss on the same material with different thickness.
To further verify the influence of copper foil roughness on insertion loss in different thicknesses, Rogers RO3003TM circuit material was selected to design 50 Ω microstrip line for research and testing. The same circuit is made on standard ED copper and calendered copper of 5 mil and 20 mil RO3003TM materials. It can be seen that at 25GHz, the difference between the insertion loss of standard ED copper and calendered copper circuit based on 5mil thickness is 0.35dB/inch; The difference between the insertion loss of standard ED copper and calendered copper based on the thickness of 20mil is only 0.1dB/inch. Since 50 Ω microstrip lines on the same material thickness have the same conductor width, the conductor loss introduced by the line width is the same. Therefore, on the same material, the insertion loss effect of copper foil roughness on thin dielectric material is greater than that on thick material. In this example, 0.25dB/inch is increased.
Therefore, selecting thicker circuit materials can reduce the influence on insertion loss under the same copper foil roughness. However, the thicker the material is, the wider the line width will be. For microwave and millimeter wave circuit applications, the wider the line width is likely to generate unnecessary stray signals, which will affect the signal transmission. Therefore, it is necessary to balance the material thickness and copper foil roughness.
3. High frequency circuit design structure
RF circuit engineers often need to select some PCB circuit technology, such as microstrip line, stripline or grounded coplanar waveguide (GCPW) to transmit signals. Different circuit transmission technologies also have differences in the final insertion loss. Microstrip line is the simplest transmission technology, but in the high-frequency millimeter wave band, the insertion loss of microstrip line is significantly increased due to radiation loss. Stripline is an excellent choice for PCB transmission lines used in microwave and millimeter wave bands, but the circuit processing process is slightly complicated. GCPW transmission line technology is a circuit structure with intermediate conductor and ground on both sides. This structure makes it have less radiation loss in millimeter wave band than microstrip line, and the circuit processing is simpler than ribbon line.
The figure shows the insertion loss simulation results when both the microstrip line based on 20mil Rogers RO4835TM material and the GCPW tightly coupled circuit are bare copper. When the frequency is low, the radiation loss of the microstrip line and the GCPW is very small, while the GCPW tightly coupled circuit has higher conductor loss due to the narrower conductor linewidth, so the microstrip line has lower insertion loss than the GCPW; When the frequency is high, the radiation loss of the microstrip line increases significantly, while the radiation loss of the GCPW is still low, and the total insertion loss of the GCPW is lower.
For the selected circuit materials, the insertion loss of GCPW transmission lines varies with the copper thickness, which is due to the electromagnetic field distribution in the GCPW structure. In the GCPW circuit structure, the electric field not only points from the top central conductor to the bottom ground, but also points from the side wall of the central conductor to the top ground to form a return path. When the copper foil is thicker, the electric field path pointing to the side wall will reach the ground on both sides through more air. Compared with the medium, the air loss is very low, so the total loss of thick copper GCPW circuit is smaller than that of thin copper under the same circuit. Similarly, the grounding spacing s of GCPW also affects the insertion loss value of the circuit. Although more air is used when the grounding spacing is small, the conductor width will become narrower at this time, leading to increased conductor loss, resulting in increased total loss under the same circuit.
When the surface treatment process is applied to the conductor surface of GCPW circuit, the change of insertion loss is different from that of microstrip line. Taking ENIG surface treatment as an example, as described in the previous section, the insertion loss of microstrip lines will increase due to ENIG surface treatment. Based on 8mil RO4003C standard ED copper material, the insertion loss of 50 Ω microstrip line using ENIG at 50GHz is about 0.7dB higher than that of bare copper; For the 50 Ω GCPW circuit designed based on the same circuit material, the insertion loss of its ENIG circuit at 50GHz is 1.1 dB higher than that of bare copper, as shown in the figure. GCPW circuit with ENIG has higher insertion loss, which is not only due to the increase of conductor loss caused by the nickel layer on the conductor surface like microstrip line; At the same time, when the electric field return path from the central conductor to the top ground plane, it will pass through the nickel layer on the ground plane surface, which further leads to the increase of insertion loss.
In short: Insertion loss of high-frequency PCB is affected by many factors.
1. Selecting circuit materials with lower dielectric loss and low copper foil surface roughness is conducive to reducing the total insertion loss of the circuit
2. Selecting thicker circuit materials is conducive to reducing the influence on insertion loss under the condition of the same copper foil surface roughness
3. If the circuit is applied to the millimeter wave band, it is necessary to balance the effects of stray and radiation loss caused by wider linewidth due to the thickness of the medium
4. At the same time, in circuit design and processing, different circuit structures and different circuit surface treatment methods will affect the total insertion loss of the circuit. Considering the influence factors of the total insertion loss of the circuit, selecting the appropriate circuit materials, design and processing can minimize the insertion loss of the circuit. Comprehensively consider all aspects to achieve the optimal PCB design scheme. circuit board manufacturers, circuit board designers and PCBA processors will explain the skin effect of high-frequency boards, the thickness of media and high-frequency structures.