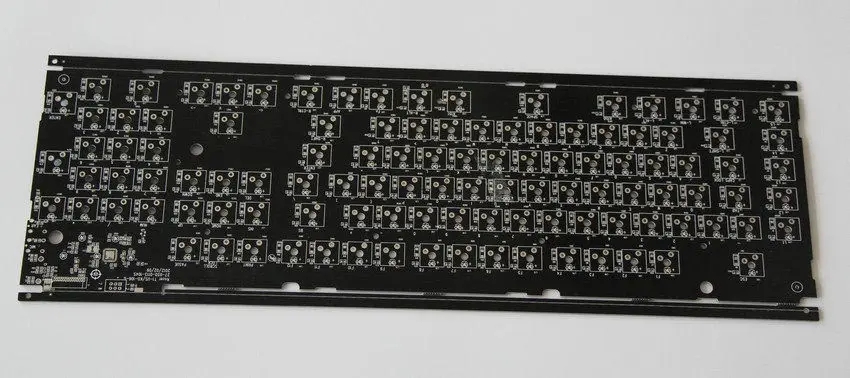
The second half of the common knowledge of SMT technology
58. The capacity value of 100NF component is the same as 0.10uf;
60. The electronic parts with the largest SMT usage are made of ceramics;
61. The maximum temperature of the temperature curve of the reflow furnace is 215C;
62. During tin furnace inspection, the temperature of the tin furnace is 245 ℃;
63. The opening type of steel plate is square, triangular, round, star shaped, and epitaxial;
64. Whether there is directivity in the SMT section;
65. Solder pastes sold on the market actually have only 4 hours of adhesive time;
66. Generally, the rated air pressure of SMT equipment is 5KG/cm2;
67. Tools for SMT parts maintenance include soldering iron, hot air extractor, tin suction gun and tweezers;
68. QC is divided into IQC, IPQC, FQC and OQC;
69. High speed mounter can mount resistors, capacitors, ICs and transistors; The packaging methods are Reel and Tray. Tube is not suitable for high-speed mounters;
70. Characteristics of static electricity: small current, greatly affected by humidity;
71. Which welding method is used when PTH on the front and SMT on the back pass through the tin furnace;
72. Common inspection methods of SMT: visual inspection, X-ray inspection, machine vision inspection, AOI optical instrument inspection;
73. The heat conduction mode of ferrochrome repair parts is conduction convection;
74. The main components of tin ball of BGA material are Sn90 Pb10, SAC305, SAC405;
75. Fabrication methods of steel plate: laser cutting, electroforming and chemical etching;
76. The temperature of the welding furnace shall be as follows: measure the applicable temperature with a thermometer;
77. When the SMT semi-finished products of the welding furnace are exported, the welding condition is that the parts are fixed on the PCB;
78. History of Modern Quality Management TQC-TQA-TQM;
79.ICT test is needle bed test;
80. ICT test can test electronic parts by static test;
81. The characteristics of soldering tin are that the melting point is lower than other metals, the physical properties meet the welding conditions, and the fluidity is better than other metals at low temperatures;
82. The measurement curve shall be re measured when the process conditions for parts replacement of the welding furnace are changed;
83. Siemens 80F/S belongs to electronic control drive;
84. The solder paste thickness gauge uses Laser light to measure: solder paste degree, solder paste thickness, and solder paste printing width;
85. The feeding methods of SMT parts include vibrating feeder, disc feeder, and coiled belt feeder;
86. Which mechanisms SMT equipment uses: cam mechanism, side bar mechanism, screw mechanism, sliding mechanism;
87. If the visual inspection section cannot be confirmed, what operation BOM, manufacturer confirmation and sample board should be followed;
88. If the part packaging method is 12w8P, the size of the counter Pinth must be adjusted to 8mm each time;
89. Type of welding machine: hot air welding furnace, nitrogen welding furnace, laser welding furnace, infrared welding furnace;
90. The methods that can be used for sample trial of SMT parts: streamline production, hand print machine mounting, hand print hand mounting;
91. Common MARK shapes are: round, cross, square, diamond, triangle, ten thousand;
92. Due to improper Reflow Profile setting in SMT section, the preheating area and cooling area may cause part microcracks;
93. The uneven heating at both ends of SMT section parts is easy to cause: empty welding, deflection, tombstone;
94. Cycle time of high-speed machine and universal machine shall be balanced as far as possible;
95. The true meaning of quality is to do well the first time;
96. The mounter shall paste small parts first and then large parts;
97. BIOS is a basic input/output system;
98. SMT parts can be divided into LEAD and LEADLESS according to whether there is a part pin;
99. There are three basic types of common automatic placers: continuous placers, continuous placers and mass transfer placers;
100. SMT can be produced without LOADER;
101. The SMT process is plate feeding system - solder paste printing machine - high-speed machine - universal machine - circular flow welding - plate receiving machine;
102. When the temperature and humidity sensitive parts are unsealed, the color displayed in the humidity card circle is blue, and then the parts can be used;
103. The size of 20mm is not the width of the tape;
104. Causes of short circuit caused by poor printing in the process: a The metal content of solder paste is not enough, resulting in collapse b. The steel plate has too many holes, resulting in too much tin content c The quality of the steel plate is poor, and the tin is poor. Replace the laser cutting template. There is solder paste left on the back of the d. Stencil, reduce the pressure of the scraper, and use appropriate VACUUM and SOLVENT;
105. Main engineering purposes of each area of the general reflow furnace profile: a. preheating area; Engineering purpose: The solvent in the solder paste volatilizes. b. Temperature equalization zone; Engineering purpose: activating flux to remove oxides; Evaporate excess water. C. Weld back area; Engineering purpose: Solder melting. d. Cooling area; Engineering purpose: forming alloy solder joints, and connecting part feet and pads as a whole;
106. In the SMT process, the main causes of solder beads are: poor PCB PAD design, poor steel plate opening design, excessive placement depth or pressure, excessive slope of profile curve, solder paste collapse, and low solder paste viscosity.
PCB manufacturers, PCB designers and PCBA manufacturers will explain the second half of the common knowledge of SMT technology.