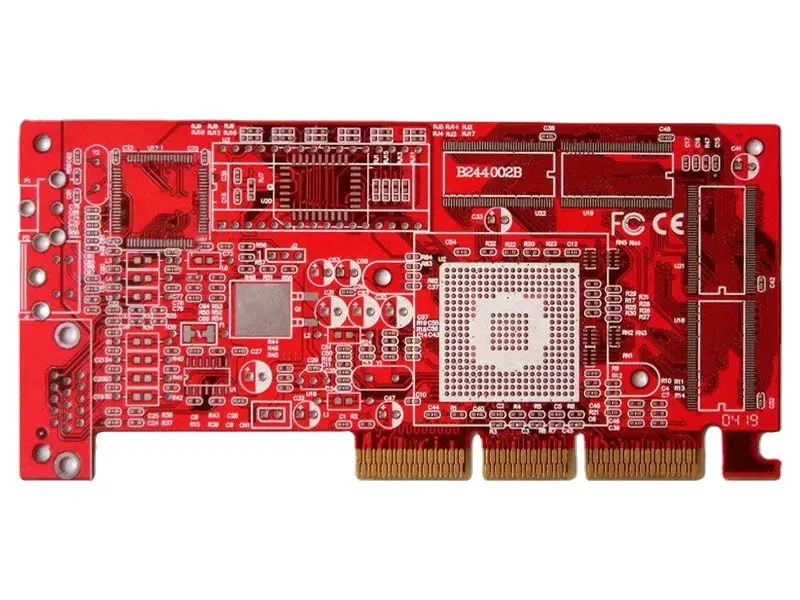
Electronic Factory Explains Surface Mount Technology of PCB
SMT is surface mount technology (SMT) (abbreviation of Surface Mount Technology), which is called surface mount or surface mount technology. It is currently the most popular technology and process in the electronic assembly industry.
It is a circuit assembly technology that installs surface mounted components without pins or short leads (SMC/SMD, referred to as chip element device in Chinese) on the surface of printed circuit board (PCB) or other substrates, and then solder and assemble them by reflow soldering or dip soldering.
Edit Material Loss
1. The suction nozzle is deformed, blocked, damaged, the vacuum pressure is insufficient, and the air leaks, resulting in the failure of material suction, improper material taking, and the failure of identification and material throwing. Solution: The technician must check the equipment every day, test the NOZZLE center, clean the suction nozzle, and maintain the equipment regularly as scheduled.
2. Poor reclaiming due to insufficient spring tension, uncoordinated suction nozzle and HOLD, and unsmooth up and down; Solution: Maintain the equipment regularly as scheduled, check and replace vulnerable parts.
3. Poor reclaiming due to deformation of HOLD/SHAFT or PISTON, bending of suction nozzle, and wear of suction nozzle; Solution: Maintain the equipment regularly as scheduled, check and replace vulnerable parts.
4. The reclaiming is not in the center of the material, and the reclaiming height is incorrect (generally subject to pressing 0.05mm after touching the parts), which causes deviation, incorrect reclaiming, and deviation. When identifying, it is inconsistent with the corresponding data parameters and is discarded as invalid material by the identification system; Solution: Maintain the equipment regularly according to the plan, check and replace vulnerable parts, and correct the machine origin.
5. The vacuum valve and vacuum filter core are dirty, and there are foreign matters blocking the vacuum gas pipe channel, which is not smooth, and the instant vacuum is not enough for the running speed of the equipment during suction, causing poor material taking; Solution: The technician must clean the suction nozzle every day and maintain the equipment regularly as scheduled.
6. The machine is not positioned horizontally, the vibration is large, and the resonance between the machine and FEEDER causes poor reclaiming; Solution: Maintain the equipment regularly as scheduled, and check the horizontal fixing support nuts of the equipment.
7. Worn and loose screw rod and bearing cause vibration and stroke change during operation, resulting in poor reclaiming; Solution: It is forbidden to blow the machine inside with an air gun to prevent dust, debris and components from adhering to the screw rod. Maintain the equipment regularly as scheduled, check and replace vulnerable parts.
8. Motor bearing wear, code reader and amplifier aging cause machine origin change, inaccurate operation data and poor reclaiming; Solution: Maintain the equipment regularly according to the plan, check and replace vulnerable parts, and correct the machine origin.
9. The vision, laser lens and suction nozzle reflector are not clean, and there are sundries interfering with the camera identification, resulting in poor handling; Solution: The technician must check the equipment every day, test the NOZZLE center, clean the suction nozzle, and maintain the equipment regularly as scheduled.
10. Poor treatment due to improper selection of identification light source, aging light intensity and insufficient gray scale; Solution: Regularly maintain the equipment according to the plan, test the brightness of the camera and the brightness of the lamp tube, and check and replace vulnerable parts.
11. Poor treatment due to aging, carbon deposition, abrasion and scratching of reflective prism; Solution: Maintain the equipment regularly as scheduled, check and replace vulnerable parts.
12. Inadequate air pressure and vacuum leakage cause insufficient air pressure and unable to pick up the material, or it falls on the way to the patch after picking up; Solution: Maintain the equipment regularly as scheduled, check and replace vulnerable parts.
13. The feeder deforms and extrudes each other, resulting in the change of feeding position and poor reclaiming; Solution: Operate as required.
14. The feeder gland is deformed and the spring tension is not enough to cause the belt not to be stuck on the ratchet gear of the feeder, not to roll the belt and throw the material. Check and replace the vulnerable parts.
15. Defective throwing caused by camera looseness and aging; Solution: Maintain the equipment regularly as scheduled, check and replace vulnerable parts.
16. The feeder's ratchet gear, drive pawl and locating pawl are worn, and the feeder's feeding is not smooth due to poor electrical and feeding motor, or the feeder is thrown due to poor reclaiming; Check and replace wearing parts
17. The feed platform of the machine was worn, which caused the FEEDER to become loose after installation, resulting in poor reclaiming; Solution: Maintain the equipment regularly as scheduled, check and replace vulnerable parts.
18. Other special parts that need to be decelerated for mounting without decelerating will also cause the underground absorption rate. Countermeasures: feed is decelerated, X/Y/H axis is decelerated or each action is adjusted to cooperate with the timing control.
brief introduction
Complex technology
As long as we pay attention to the themes of various professional conferences held around the world today, we can easily know which latest skills are used in electronic products. CSP, 0201 passive components, lead-free soldering and optoelectronics are the advanced skills that many companies should show off in PCB manufacturing and SMT processing recently. For example, how to deal with the common problem of super small opening (250um) in CSP and 0201 assembly is the fundamental physical problem never existed in solder paste printing. Board level optoelectronic assembly, as a major category developed in communication and network skills, has a very sophisticated process. Typical packaging is expensive and easy to damage, especially after the equipment leads are formed. The description guidance rules of these messy skills are also very different from the general SMT process, because the board description plays a more important role in ensuring the assembly productivity and product reliability; For example, for CSP welded interconnects, the reliability can be significantly improved only by changing the board bonding disk size.
circuit board manufacturing, circuit board design and PCBA processing manufacturers will explain the circuit board surface mounting technology to you in detail in the electronic factory.