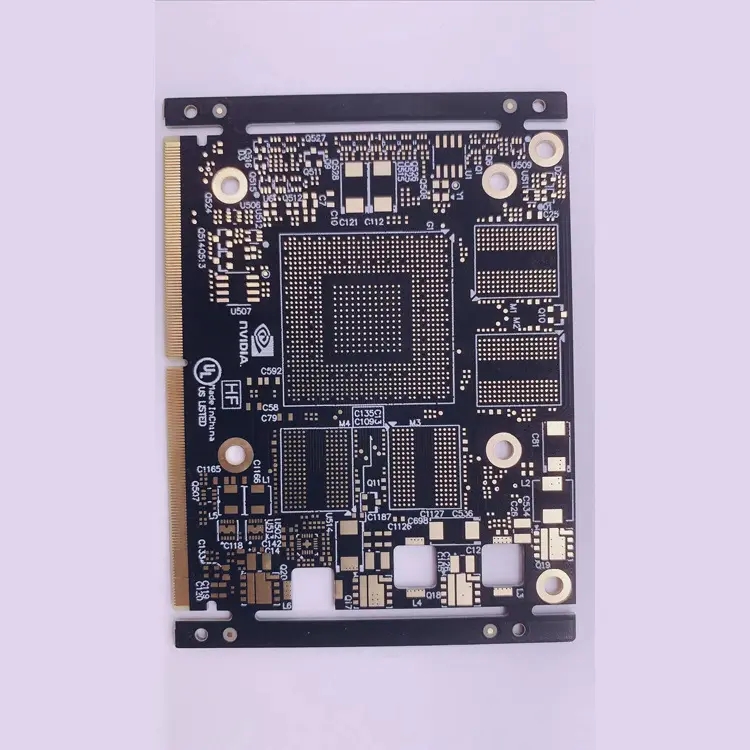
Explain the basic structure of the pcb horizontal electroplating system
According to the characteristics of horizontal electroplating, it is a electroplating method that changes the placement mode of printed circuit board from vertical to parallel liquid level. At this time, the printed circuit board is cathode, and some horizontal electroplating systems use conductive clips and conductive rollers to supply current. In terms of the convenience of the operating system, it is common to adopt the roller conductive supply mode. The conductive roller in the horizontal electroplating system not only acts as the cathode, but also has the function of transmitting the printed circuit board. Each conductive roller is equipped with a spring device, which can meet the needs of electroplating of printed circuit boards (0.10-5.00mm) of different thicknesses. However, when electroplating, the parts contacting with the plating solution may be coated with copper, and the system will not work for a long time.
Therefore, most of the current horizontal electroplating systems are designed to switch the cathode into an anode, and then use a group of auxiliary cathodes to electrolyze the copper on the plated roller. For the sake of maintenance or replacement, the new electroplating design also considers that the parts easy to wear are easy to remove or replace. The anode is an array adjustable size insoluble titanium basket, which is placed at the upper and lower positions of the printed circuit board respectively. It is filled with a 25 mm diameter spherical copper with a phosphorus content of 0.004-0.006%. The distance between the cathode and the anode is 40 mm.
The flow of the plating solution is a system composed of a pump and a nozzle, which enables the plating solution to flow rapidly in a closed plating bath alternately from front to back, up and down, and ensures the uniformity of the plating solution flow. The plating solution is sprayed vertically to the printed circuit board, forming a wall impinging jet vortex on the printed circuit board surface. The final goal is to achieve rapid flow of the plating solution on both sides of the printed circuit board and through holes to form eddy currents.
In addition, the tank is equipped with a filtering system, in which the adopted filter screen has a mesh of 1.2 microns to filter out the particulate impurities generated in the electroplating process, so as to ensure that the plating solution is clean and free of pollution.
When manufacturing horizontal electroplating system, easy operation and automatic control of process parameters should also be considered. Because in actual electroplating, with the size of the printed circuit board, the size of the through-hole aperture and the required copper thickness, the transmission speed, the distance between the printed circuit boards, the size of the pump horsepower, the direction of the nozzle and the height of the current density and other process parameters, actual testing, adjustment and control are required to obtain the copper layer thickness that meets the technical requirements. A computer must be used for control. In order to improve the production efficiency and the consistency and reliability of the quality of high-grade products, the pre and post processing of the through-hole of the printed circuit board (including the plating hole) according to the process procedures constitutes a complete horizontal electroplating system, which is to meet the needs of new product development and marketing.
PCB manufacturers, PCB designers and PCBA processors will explain the basic structure of the PCB horizontal electroplating system.