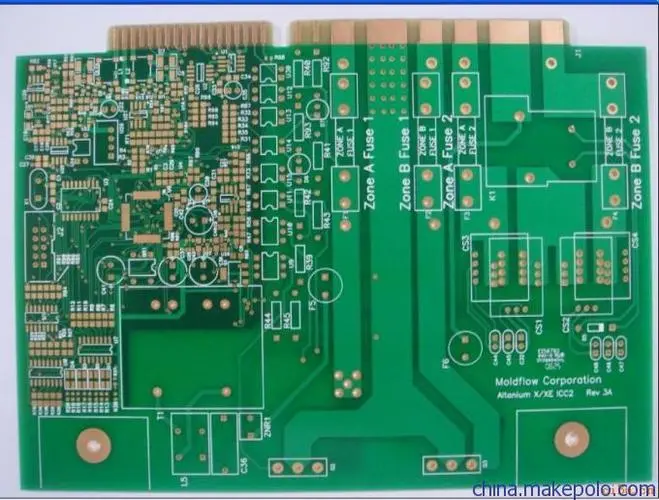
Looking at the current environmental protection situation, the recycling of PCB production wastewater is imperative, and the government supervision on the standard discharge of recycled residual water and sewage without recycling value is becoming increasingly strict. Combined with the current national environmental protection administration's outstanding attention to COD in the total amount control project. This paper mainly deals with the recovery and treatment of PCB high concentration organic waste liquid in PCB waste liquid.
Status quo of disposal of high concentration organic waste liquid
As for the high concentration organic waste liquid (non cleaning water) generated from PCB manufacturing, there is no authoritative statistical data on pollutants in China so far. The following table shows the investigation results of overseas environmental protection operators on the pollutant emission of PCB enterprises.
Mixed collection, acidification destabilization, solid-liquid separation. After the CODcr of the clear liquid is reduced to 10~20% of the original waste liquid, it is treated by chemical method together with the rinsing waste water of each process. Chemical treatment process will also remove part of it due to coagulation. The total drainage CODcr fluctuates above and below the 110mg/L mark line, and the fluctuation range varies with the treatment process, dilution water volume and specific operation.
Most of the fluffy waste liquid, degreasing waste liquid, copper settling waste liquid and OSP waste liquid are entrusted for disposal. There may also be individual cases of collaborative treatment and discharge with waste water.
Organic pollutants in high concentration organic waste liquid
Developing and film stripping waste liquid
The main organic pollutant of developing and film stripping waste liquid is photosensitive coating, and the main component of photosensitive coating is photosensitive resin. The photosensitive resin undergoes photocrosslinking or entanglement reaction after UV exposure, and the solubility of the reaction product is obviously different from that of the unreacted product.
Photosensitive coatings are made of a variety of functional raw materials. Generally, the combination includes adhesives, photopolymerization polymers, photopolymerization initiators, plasticizers, stabilizers, diluents, polymerization inhibitors and anti halo dyes. Among them, adhesives and photopolymerization polymers are the main parts of the film, accounting for about 80% of the film weight.
Photosensitive coatings can be divided into two categories: positive and negative. The supply of goods can be divided into two modes: photosensitive dry film and water-based coatings. Their applications can be divided into two types: anti etching and anti electroplating. The development operation can be divided into two types: solvent based and water based. At present, negative image, water developing dry film or wet film are mostly used in PCB production, especially in multi-layer PCB production. The representative PCB products are mostly acrylic unsaturated polyester, acrylic polyether, acrylic epoxy resin, acrylic polyurethane, etc.
The property of the matrix used in the photosensitive coating was initially developed as "alkali soluble resin". The functional groups in the alkali soluble resin can react with the alkaline cations in the treatment medium at different stages of use, resulting in saponification, dissolution, swelling, stripping, crushing and other phenomena, and then enter the treatment medium. The development and stripping of dry film or wet film are based on the above principles.
The photosensitive film that partially dissolves, swells, peels, and breaks into the developing or film stripping waste liquid is the main organic pollutant in the developing and film stripping waste liquid. The COD of the acidifiable and destabilizing separation part accounts for 80~90% of the total COD of the mixed waste liquid, so it is necessary to conduct acidification and destabilization separation in the environmental treatment of the developing and film stripping waste liquid.
In addition to the separable photosensitive resin, the organic pollutants in the development and film stripping waste liquid also contain defoamer which accounts for about 0.25% of the volume of the development and film stripping working solution. Common sense shows that a certain concentration of alkali solution is easy to produce foam under stirring conditions. The contact between the alkaline solution and the circuit board in the development and film removal operation is realized by pressure spraying, which creates an excellent condition for the alkaline foam. Under the requirement of increasingly fine PCB graphics, alkaline solution foam is an adverse factor for operation and must be eliminated, so it is necessary to add defoamer in the development and film removal working solution. The defoamer component that can play the role of defoaming under alkaline conditions is generally a water-soluble system uniformly prepared by hydrocarbons, higher fatty acid salts and emulsifiers (surfactants). The defoamer only changes the surface tension of the working solution during the working process, without chemical reaction, and its composition remains basically unchanged. It is not difficult to see that defoamers are another kind of soluble organic pollutants that cannot be avoided in the development and film stripping waste liquid and cannot be separated by acidification destabilization.
The development and film stripping waste liquid discharged from PCB production is a suspension liquid. This suspension liquid will deposit suspended solids at the corner of the working solution tank body of the rectangular section. This sediment needs to be removed before the development and film stripping working solution is updated. At present, the industry mostly uses the so-called tank washing water for this operation. The tank washing water is generally 2~5% hydrochloric acid or 5~10% EDTA tetrasodium salt, which may also be used in combination. The tank washing liquid is discarded together with the developing and film stripping waste liquid along the same pipeline. If the tank washing water is the latter or a mixture of the two, there is no doubt that EDTA is also an organic pollutant in the high concentration organic waste liquid.
Fluffy waste liquid
The pre-treatment process of hole metallization in PCB production includes bulking treatment. The object of bulking treatment is the hole wall of rigid board epoxy glass substrate or flexible board polyimide and other film materials. The essence of this operation is a slight swelling process of cured epoxy resin or polyimide. The media used in the data report is alkaline alcohol ether or amide organic solvent. The fluffy working medium needs to be discarded and replaced regularly. The CODcr of the discarded fluffy working medium is up to 200g/L. It should be collected separately and entrusted for disposal. Do not mix it with the high concentration organic waste liquid system.
Copper waste liquid
The working solution of copper precipitation in the hole metallization process produced by PCB also has the problem of waste and renewal. The Cu2+in the waste mother liquor is about 1.4~4.5g/L, and the CODcr is about 30~100g/L. The COD comes from the complex ligand EDTA and the reducing agent formaldehyde in the autocatalytic system. At present, most wastewater treatment processes use complexing wastewater for dilution and collaborative treatment. There is basically no technical difficulty for copper to reach the standard, but the COD standard depends on the process arrangement.
In the early wastewater treatment diversion, the wastewater is basically divided according to the production line, and the amount of complex wastewater obtained is relatively large, which has obvious dilution effect on COD standard. Under the new situation of sewage recycling, the traditional sewage diversion mode is worth reviewing. If we go deep into the investigation of the workshop process production line, we will find that the whole PTH operation line generally includes the removal of glue residue and copper deposition operations, including nine links: bulking, oxidation, reduction, hole finishing, micro etching, pre activation, activation, acceleration and copper deposition. Only one of them really discharges complex wastewater, and the cleaning water from the four links of micro etching, pre activation, activation and acceleration can be used as the water source for sewage recycling. Therefore, in the new situation, the collection of dilution water will be greatly reduced during the treatment of copper plating waste liquid, which will force PCB manufacturers and environmental protection industry to face up to the organic pollution problem in the treatment of copper plating waste liquid and seek a new treatment mode.
Degreasing waste liquid
There are many degreasing operations in PCB production with water. The degreasing agents are divided into alkaline and acidic ones. The CODcr of waste working solution is about 3000 ~ 5000mg/L. In addition, the whole hole waste liquid, which is also regarded as the oil removal working solution, contains a small amount of organic solvent in addition to the surfactant, and the CODcr of the waste liquid is about 100000 ~ 150000mg/L. It can be seen that after most of the original dilution water is collected and reused, a new way to dispose of the degreasing waste liquid also needs to be found.
OSP waste liquid
Anti oxidation treatment unit is arranged in PCB production process. The anti oxidation treatment solution contains imidazole organics and corresponding solvents, and the waste solution may also contain copper complexes. It can be seen that the waste liquid should also be identified and properly disposed of organic pollutants and copper pollutants.
other
PCB production is a combination of technical means, and the raw materials used are complex and changeable. For example, there are indications that the CODcr test value of some micro etching solutions is quite high, which is believed to be the cause of the additives such as stabilizers and accelerators in the micro etching system through inquiry, which is really thought-provoking. The use and safe disposal of these solutions depend on the joint efforts of PCB manufacturers and environmentalists to achieve a safe and environmentally friendly state.
Problems to be faced by the discharge of high concentration organic waste liquid
According to the current severe environmental situation, it is imperative for pcb manufacturing enterprises to implement sewage recycling.
The main way for PCB manufacturing enterprises to implement sewage recycling is to use membrane separation technology to recover and treat relatively clean general rinsing water in each process. At present, the recovery rate can be stabilized at about 80%. The remaining 20% of residual water will be sent to the original sewage treatment plant for treatment and discharge.
At present, the design goal of most PCB enterprises' wastewater treatment plants is to meet the copper standard. The COD standard of enterprises' wastewater with double-sided boards as the main product depends on dilution. After implementing the requirements of sewage recycling, 60~65% of the workshop drainage will be returned to the workshop as recycled water. This leads to the situation that the amount of water entering the sewage treatment system is only 35~40% of the original design amount, while the total amount of pollutants entering the sewage treatment system is basically unchanged. Under the new situation, the metal pollutants in the sewage can still be separated and purified according to the solubility product principle, but it is impossible to achieve the COD standard by water dilution.