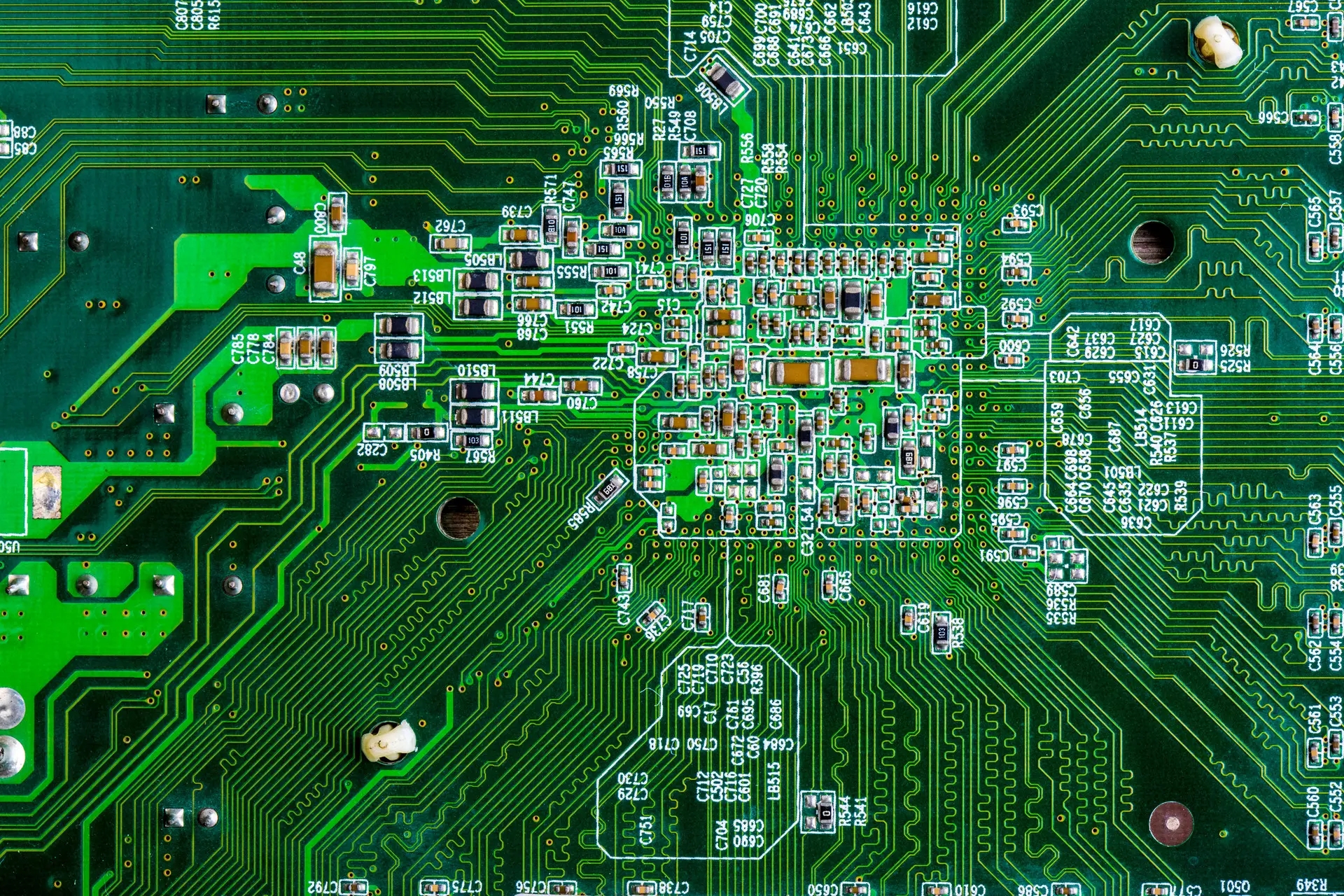
PCB Process PCB PCB Inspection Method and Its Introduction
The circuit board manufacturer and circuit board designer explain the circuit board inspection method
This paper describes that process monitoring can prevent PCB defects and improve overall quality.
Inspection can often remind you whether there are too many variables in your assembly process. Even after your manufacturing process can achieve continuous zero defect production, some form of inspection or monitoring is necessary to ensure the desired quality level. surface mount assembly is a series of very complex events with a large number of individual actions. Our trick is to establish a balanced inspection and monitoring strategy without 100% inspection. This article will discuss the inspection methods, techniques and manual inspection tools, as well as review the automatic inspection tools and use the inspection results (defect quantity and type) to improve the process and product quality.
Inspection is a product centered activity, while monitoring is a process centered activity. Both are necessary for a quality plan, but the long-term goal should be less product inspection and more process monitoring. Product inspection is passive (defects have occurred), while process monitoring is active (defects can be prevented) - obviously, prevention is more valuable than passive response to existing defects.
Inspection is actually a screening process, because it attempts to find unacceptable products to repair. It is clear that a large number of inspections do not necessarily improve or guarantee product quality. The third of Deming's fourteen points said,% 26ldquo; Don't expect mass inspections of% 26rdquo;. Deming emphasized that a strong process should focus on establishing stable, repeatable and statistically monitored process objectives, rather than mass inspection. Inspection is a subjective activity, and even with considerable training, it is also a difficult task. In many cases, you can ask a group of inspectors to evaluate a weld, but get several different opinions.
Operator fatigue is the reason why 100% inspection usually fails to find every manufacturing defect. In addition, this is an operation with high cost and no value added. It rarely achieves the desired goal of higher product quality and customer satisfaction.
A few years ago, we started using% 26ldquo; Process monitoring% 26rdquo; This term, not inspector, is used because we want to change the ideology of the production place from passive reaction to active prevention. An inspector usually sits at the end of the assembly line and checks the product. In an ideal situation, process monitoring activities are a balance between product inspection and process monitoring - for example, confirming that correct process parameters are being used, measuring machine performance, and establishing and analyzing control charts. Process monitoring assumes a leading role in these activities; They help the machine operator accomplish these tasks. Training is a key factor. Process monitors and machine operators must understand process standards (e.g., IPC-A-610), process monitoring concepts and related tools (e.g., control charts, Pareto charts, etc.). Process monitors in circuit board manufacturers also improve product quality and process monitoring. As a key member of the manufacturing team, the monitor encourages a defect prevention method rather than a search and repair method.
Overchecking is also a common problem. In many cases, the over inspection is only caused by the misplaced understanding of IPC-A-610 process standard. For example, for components inserted and installed, many inspectors also want perfect welding round legs on both sides of the plate, and the through-hole is completely filled. However, this is not required by IPC-A-610. The inspection quality fluctuates with the inspector's attention tension and concentration. For example, fear (management pressure) may improve the concentration of the production site, and the quality may improve over time. However, if mass inspection is the main inspection method, defective products may still be produced and may go out of the factory.
Another term we should avoid is touch up. In this industry, many employees believe that repair welding is a normal and acceptable part of the assembly process. This is very unfortunate, because any form of rework and repair should be regarded as undesirable. Rework is usually regarded as undesirable, but it is necessary information instilled in the entire manufacturing organization. It is important to establish a manufacturing environment that regards defects and rework as avoidable and least desirable.
For most companies, manual inspection is the first line of defense. Inspectors use a variety of magnification tools to view components and welds more closely. IPC-A-610 establishes some basic magnification guidelines based on the pad width of the inspection element. The main reason for these guidelines is to avoid excessive inspection due to excessive amplification. For example, if the pad width is 0.25~0.50 mm, the desired magnification is 10X. If necessary, 20X can also be used as a reference.
Every inspector has a favorite inspection tool; It is better to have a three lens folding pocket magnifying glass used by a mechanic. It can be carried with a maximum magnification of 12X, which is just suitable for close spacing welding points. Perhaps the most common inspection tool is a microscope with a magnification of 10-40X. However, the fatigue caused by the continuous use of the microscope usually leads to excessive inspection, because the magnification usually exceeds the guidelines of IPC-A-610. Of course, it is useful when you need to carefully examine possible defects.
For general inspection, a video system equipped with a zoom lens (4-30X) and a high-definition color monitor is preferred. These systems are easy to use and, more importantly, less fatigued than microscopes. High quality video systems cost less than $2000, and good microscopes cost less than $2000. The additional benefit of the video system is that more than one person can see objects, which is helpful in training or when inspectors need a second opinion. Edmund Scientific (edmundscientific. com) has a large number of magnification tools, ranging from hand-held magnifiers to microscopes to video systems.
To sum up, it is a challenge to establish a balanced monitoring strategy between 0-100% inspection. From this point, the key checkpoint, we will discuss the inspection equipment
Automation is wonderful; In many cases, it is more accurate, faster and more efficient than inspectors. But it may be quite expensive, depending on its complexity. Automatic inspection equipment may weaken people's consciousness and give people an illusion of safety.
Solder paste printing is a complex process, and it is easy to deviate from the desired results. A clearly defined and properly implemented process monitoring strategy is required to keep the process under control. At least the coverage area and thickness measurement shall be manually checked, but it is better to use automatic coverage, thickness and volume measurement. Use the range control chart (X-bar R chart) to record the results.
Solder paste inspection equipment has simple 3X magnifying glass to expensive automatic online machine. The primary tool uses optics or lasers to measure thickness, while the secondary tool uses lasers to measure coverage, thickness, and volume. Both tools are used offline. The third level tools also measure the coverage area, thickness and volume, but are installed online. The speed, accuracy and repeatability of these systems are different, depending on the price. The more expensive the tool, the better the performance.
For most assembly lines, especially for highly mixed production, the medium level performance is preferred. It is an offline tool for installing worktops to measure coverage, thickness and volume. These tools are flexible, cost less than $50000, and generally provide the desired amount of feedback. Obviously, automation tools are much more expensive ($75,000 - $200,000). However, they are faster and more convenient because they are installed online. It is most suitable for assembly lines with large batch and low mixing.
Check the glue.
Glue distribution is another complex process that easily deviates from the desired results. As with solder paste printing, a clearly defined and properly implemented process monitoring strategy is required to keep the process under control. It is recommended to check the glue point diameter manually. Use the range control chart (X-bar R chart) to record the results.
Before and after a glue dropping cycle, it is a good idea to drop at least two isolated glue points on the board to represent the diameter of each point. This allows the operator to compare the glue spot quality during the glue cycle. These points can also be used to measure the diameter of glue points. Glue point inspection tools are relatively inexpensive, and basically there are portable or desktop measuring microscopes. It is not known whether there is any automatic equipment specially designed for glue spot inspection. Some automatic optical inspection (AOI) machines can be adjusted to complete this task, but they may be overqualified.
Confirmation of the first article.
The company usually carries out a detailed inspection of the first plate coming off the assembly line to verify the setting of the machine. This method is slow, passive and inaccurate. It is common to see that a complex board contains at least 1000 components, many of which are not marked (value, part number, etc.). This makes inspection difficult. It is a positive method to verify the machine settings (elements, machine parameters, etc.). AOI can be effectively used for the inspection of the first plate. Some hardware and software suppliers also provide feeder setting confirmation software.
Coordinating the verification of machine settings is an ideal role for a process monitor, who leads the machine operator to confirm the process through the production line with the help of a checklist. In addition to verifying the settings of the feeder, the process monitor should carefully check the first two plates using existing tools. After reflow soldering, the process monitor should conduct a quick but detailed inspection of key components (closely spaced components, BGA, polar capacitors, etc.). At the same time, the production line continues to assemble the plates. To reduce downtime, the production line should fill the plates before reflow while the process monitor checks the first two plates after reflow. This may be dangerous, but you can gain confidence in doing so by verifying the machine settings.
X-ray inspection. Based on experience, X-ray is not mandatory for BGA assembly. However, it is certainly a good tool to have on hand, if you can afford it. It should be recommended for CSP assemblies. X-ray is very good for checking welding short circuit, but it is less effective for finding welding open circuit. The low-cost X-ray machine can only look down, and the inspection of welding short circuit is sufficient. The X-ray machine that can tilt the object under inspection is better for open circuit inspection.
Automatic Optical Inspection (AOI). Ten years ago, optical inspection was used as a tool to solve everyone's quality problems. Later, this technology was stopped because it could not keep up with the pace of assembly technology. In the past five years, it has reappeared as a desirable technology. A good process monitoring strategy should include some overlapping tools, such as online testing (ICT), optical inspection, functional testing and visual inspection. These processes overlap and complement each other, and cannot provide sufficient coverage separately.
A two-dimensional (2-D) AOI machine can check for missing components, misalignment errors, incorrect part numbers, and reverse polarity. In addition, the three-dimensional (3-D) machine can evaluate the quality of welding points. Some suppliers provide desktop, 2-D AOI machines at a price lower than $50000. These machines are ideal for initial product inspection and small batch sample planning. In the higher performance category, 2-D standalone or online machines cost $75000-125000, while 3-D machines cost $15000-250000. AOI technology has a bright future, but processing speed and programming time are still a limiting factor.
Data collection is one thing, but using this data to improve performance and reduce defects is the ultimate goal. Unfortunately, many companies collect a lot of data without using it effectively. It may be laborious to review and analyze data. It is often seen that this work is only carried out by engineering pcb designers, not including production activities. Without accurate feedback, production proceeded blindly. Weekly quality meeting may be an effective method for engineering design and production department to communicate key information and promote necessary improvement. These meetings require a leader to be well organized, especially in a short time (30 minutes or less). The data presented at these meetings must be user-friendly and meaningful (e.g. Pareto charts). When a question is confirmed, an investigator must be assigned immediately. In order to ensure a successful conclusion, the leaders of the meeting must make accurate records. Ending means root cause and corrective action.