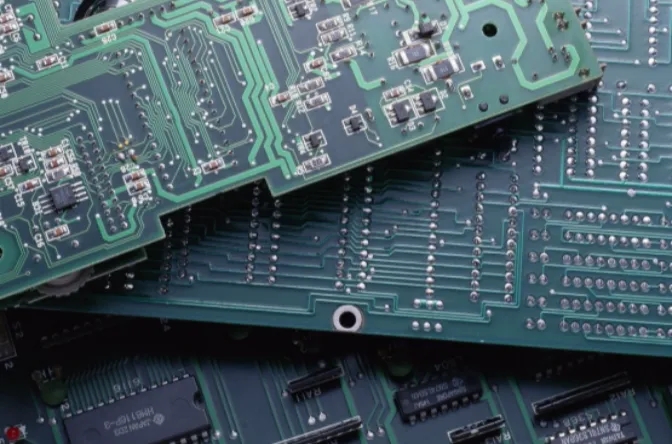
PCB process OSP surface treatment
1、 OSP PCB production requirements
1. PCB incoming materials shall be vacuum packed and attached with desiccant and humidity display card. During transportation and storage, isolation paper shall be used between PCBs with OSP to prevent friction damage to OSP surface.
2. It shall not be exposed to direct sunlight, and shall be kept in a good warehouse storage environment. The relative humidity is 30~70%, the temperature is 15~30 ℃, and the storage life is less than 6 months.
3. When unpacking at the SMT site, the vacuum packaging, desiccant, humidity display card, etc. must be checked. The unqualified plates shall be returned to the manufacturer for rework and reuse, and shall be online within 8 hours. Do not disassemble more than one package at a time, and follow the principle of "produce as much as you dismantle, and produce as much as you dismantle". Otherwise, too long exposure time will easily lead to poor quality accidents of batch welding.
4. Do not stay in the furnace as soon as possible after printing (the longest time is not more than 1 hour), because the flux in the solder paste has strong corrosion on the OSP film.
5. Keep a good workshop environment: relative humidity 40~60%, temperature 18~27 ℃.
6. In the production process, it is necessary to avoid directly touching the PCB surface with hands, so as to prevent its surface from being polluted by sweat and oxidation.
7. After the SMT single side mounting is completed, the SMT part mounting assembly of the second side must be completed within 12 hours.
8. After the SMT, the DIP hand plug-in should be completed in the shortest possible time (24 hours at most).
9. The OSP PCB can not be baked when it is damp, and it is easy to deteriorate the color of the OSP when it is baked at high temperature.
10. Overdue empty boards not used in production, wet empty boards, and empty boards cleaned with batch printing defects shall be returned to the Circuit board manufacturer for OSP rework and reuse, but the same board shall not be reworked more than three times, otherwise it shall be scrapped.
2、 SMT Solder Paste Steel Mesh Design Requirements for OSP PCB
1. OSP is flat, which is good for solder paste forming, and PAD can not provide some solder, so the opening should be appropriately increased to ensure that the solder can cover the entire pad. When the PCB is changed from tin spraying to OSP, the steel mesh needs to be reopened.
2. After the opening is appropriately enlarged, in order to solve the problem of exposed copper of solder beads, tombstones and OSP PCBs of SMT CHIP pieces, the design method of solder paste printing steel mesh opening can be changed to concave design, and special attention should be paid to tin bead prevention.
3. If parts are not placed on PCB for some reason, solder paste should also cover the bonding pad as much as possible.
4. In order to prevent the oxidation of bare copper foil and cause reliability problems, it is necessary to consider printing solder paste on the front of ICT test points, mounting screw holes, bare through holes, etc.
3、 Processing Requirements for OSP PCB Printing Solder Paste Defective Board
1. Try to avoid printing errors, as cleaning will damage the OSP protective layer.
2. When PCB printing solder paste is poor, because OSP protective film is easily eroded by organic solvent, all OSP PCBs cannot be soaked or cleaned with highly volatile solvent, non-woven cloth can be used to wipe solder paste with 75% alcohol, and air gun can be used to dry the solder paste in time. Do not use isopropyl alcohol (IPA) to clean, and do not use a stirring knife to scrape the solder paste on the poor printing board.
3. The SMT chip soldering operation on the PCB surface of the current rework should be completed within 1 hour after the PCB with bad printing is cleaned.
4. In case of printing defects in batches (such as 20PCS and above), they can be returned to the manufacturer for rework.
4、 Requirements for setting reflow furnace temperature curve of OSP PCB
The setting requirements for reflow soldering temperature curve of OSP PCB are basically the same as those of tin spraying board, and the maximum peak temperature can be appropriately lowered by 2-5 ℃.
5、 Notes:
1. OSP process introduction: OSP is the abbreviation of Organic Solidability Preservatives, which in Chinese means: organic protective film, also known as copper protector. It is a process technology to coat a layer of OSP film (usually controlled at 0.2-0.5um) on the (double-sided/multi-layer/two-layer) bare copper pad for protection, replacing the original tin spraying and other protective treatment on the pad surface. Advantages of OSP PCB: low PCB production cost, high pad surface flatness, meeting the lead-free process requirements.
Disadvantages of OSP PCB: high requirements for use (limited time use after opening, limited time completion of front and back side, plug-in wave soldering production), high requirements for storage environment, PCB surface is easy to oxidize, it is usually not allowed to bake and reuse when wet, and poorly printed boards cannot be cleaned and reused at will.