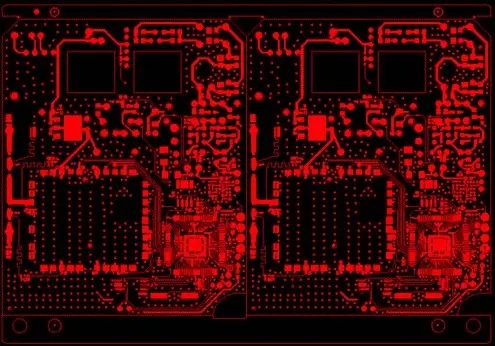
Processing Technology of PCB Board with Carbon Dioxide (CO2) Laser Equipment
Laser equipment
With the high-density interconnection design of PCB boards and the progress of electronic science and technology, carbon dioxide (CO2) laser processing equipment has become an important tool for PCB manufacturers to process PCB micropores. Carbon dioxide (CO2) lasers and UV fiber lasers are commonly used laser processing equipment for PCB manufacturers. The development of laser processing technology for PCB micropores is also rapid.
At present, in some large domestic printed circuit board manufacturers, the carbon dioxide (CO2) laser and UV laser hole forming process technology is gradually used to process multilayer PCB boards with higher density interconnection. With the continuous progress of copper carving handicraft technology, the carbon dioxide (CO2) laser hole forming method has been rapidly popularized and widely applied in PCB multilayer circuit boards. And further promote the multilayer board to the field of inverted chip packaging, so as to promote the development of multilayer board to higher density. As a result, the number of blind hole machining holes in multilayer PCB is increasing. Generally, the number of holes on a single side is about 20000 to 70000, or even 100000 or more.: For such a large number of blind holes to be processed, in addition to using the photoinduced method and plasma method to manufacture blind holes, especially with the smaller and smaller diameter of blind through holes, using carbon dioxide (CO2) laser and UV laser processing to manufacture blind through holes is one of the low-cost and high-speed processing methods that Circuit board manufacturers can achieve.
Development of laser processing through hole
At the end of the 1980s, AT&T Circuit Board Research and Development Department had developed CO2 laser processing equipment to process micro holes in the FR-4 PCB made of epoxy glass. As 10.60um infrared wavelength is used, the copper skin on the surface of the circuit board cannot be ablated (because the infrared absorption rate of the metal copper is very low), and organic carbide will be left on the copper (bottom copper) surface of the inner layer, while the glass fiber cloth (wire) in the medium layer is not easy to burn off or leave a molten state (the infrared absorption rate of the glass is also very low), so careful treatment must be carried out before coating holes, otherwise, it will cause difficulties in porous electroplating, Or the hole wall roughness is large, so it has not been promoted and applied in PCB industry. Then IBM and Simens developed gas lasers, such as argon lasers, krypton lasers, xenon lasers and other excimer lasers, with laser wavelengths ranging from 193 nm to 308 nm (nanometers). Although it can effectively avoid the carbonization of rabbit organics and the problem of glass protrusion, it has not been widely promoted and applied in the PCB industry due to the special inert gas, slow processing speed, instability and low output (energy). However, it can be used to effectively remove the carbonization residues caused by carbon dioxide laser, so it can be used to form holes in carbon dioxide laser, and then the residues can be removed by excited excimer laser to ensure the quality of laser forming holes.
The method of laser processing PCB boards has been applied in circuit board manufacturers so far. Due to the sharp increase in requirements for micro holes in multilayer PCB boards and the continuous improvement and perfection of carbon dioxide laser equipment and processing technology, carbon dioxide lasers have been rapidly promoted and applied. At the same time, more stable solid-state (bulk) laser equipment has been developed. After multiple harmonics, the laser can reach the ultraviolet light level. Because the peak value can reach 12kw and the repetition power can reach 50, it is also suitable for various PCB materials (including copper foil and glass fiber cloth). Therefore, for processing micro holes smaller than 0.1 μ m, Undoubtedly, it is one of the most promising processing methods for circuit board manufacturers to produce multilayer PCB boards with high-density interconnection.
The laser processing equipment that is really applied to PCB production by PCB manufacturers is mainly carbon dioxide laser and UV laser. The role of the laser source of these two lasers is different. One is for burning copper skin, and the other is for burning substrate. Therefore, CO2 laser and UV laser are used in PCB laser processing.