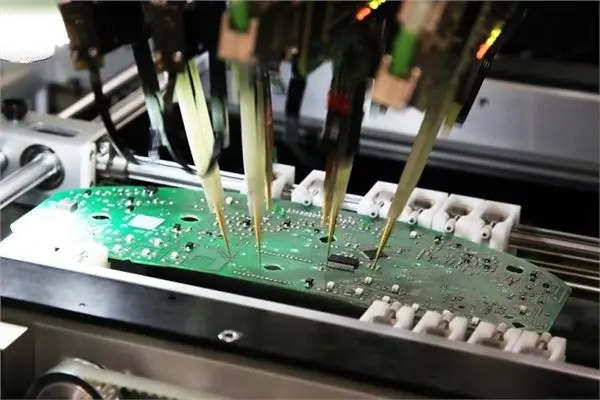
printed circuit boards base metal layers on separate wiring layers, so slave connections between layers are essential. In order to achieve the purpose of interlayer connection, it is necessary to use the wrong hole method to form a pathway and make a reliable conductor on the hole wall, in order to complete the electrical or signal connection. Since the introduction of through-hole plating, almost all multilayer circuit boards have been produced in this way.
The high-density circuit board is made by the layered production mode, forming small holes in the dielectric material by mechanical, laser or light induction, and then electroplating conductive means to make the electrical path. Of course, there are some producers who conduct holes by filling the connections with conductive glue, but the basic concept is similar.
Through-hole plating has been used in multilayer printed circuit boards for decades, and all holes are classified as guide general holes except for plug-in holes for plug-on components and tool holes for holding. In Chinese, the distinction is not obvious, but in English, the hole used by plug-ins and tools is called hole, which has a clear taste of hole. But in the pure guide general hole is called via, its meaning has a taste of reaching another place through one place, so pure means pathway.
As circuit board density increases, you can basically expect more VIAs and fewer holes. There will be more SMD components installed and fewer DIP components. Of course, the line can be closer, and the distance density of the contact points can be improved. The same product can be completed with a smaller occupation area.
In order to achieve the realistic goal of no-burdensome mobility, some of the advanced japanese electronics manufacturers have divided the general electronic products into ten categories, from the small wrist and wearable products, to the characteristics of the notebook computer. Among them, it is worth mentioning that all products must do one thing in order to be really convenient and portable, that is, they must be able to be placed in the front chest pocket when they are stored, but they do not feel burdened. If such a standard is broadly estimated, the total thickness can not exceed 5mm, or a more rigorous point that 3mm is a more ideal number. Nowadays, most electronic products must include a simple display and basic functional components around it.
These requirements not only compress the available geometry of the board, but also force all components to be careful in their thickness control. At present a lot of electronic products not only connect with high density PCB as matrix, at the same time in the aspects of electronic packaging also toward the stack model, type of packaging to save baidu and space occupancy rate, which makes the circuit board can no longer be independent of the development of electronic packaging, a variety of different construct module are also with high density structure collocation of loading plate.
As the board moves toward higher density, there are actually several fundamental changes in characteristics that occur from a geometric point of view. One is that the stack structure of the holes changes. The three-dimensional structure of the hole will change from the traditional pure through-hole structure to the sequential platen structure, and then to the microporous high-density circuit board structure or hybrid structure. The development trend is shown in Figure 1.3.
From the geometric structure can be easily understood, if the traditional circuit board in a coordinate to make a through-hole structure, even if the connection between two layers of the line, but in fact the hole has occupied a position, which not only waste space and can not be assembled in this position. However, if the sequential pressing method is adopted, more than two connections can be made in the same position, and the use of space is obviously improved.
But this method is not ideal in practice because it must face the test of thin plate manufacturing process.
As for the use of high-density circuit board technology, because The use of blind hole structure and the introduction of effective microhole formation technology, can improve the connection density without facing the problem of sheet manufacturing process. In the aspect of assembly, because the pin welding can be carried out directly above the blind hole, so it can save a lot of geometric space. These advantages make the high-density circuit board become a new favorite in the design of a new generation of electronic products.
However, due to the consideration of electrical requirements, some telecom product manufacturers still require to retain part of the serial pressing structure for the sake of electromagnetic radiation and design structure, which makes the phenomenon of the mixture of the two technologies more and more common. In addition, because of the convenience of product storage, some foldable product design is popular. Because of this, the soft board and hard board are assembled together or directly with the soft and hard board to produce high-density circuit boards, which also plays a certain important role in the emerging electronic market.