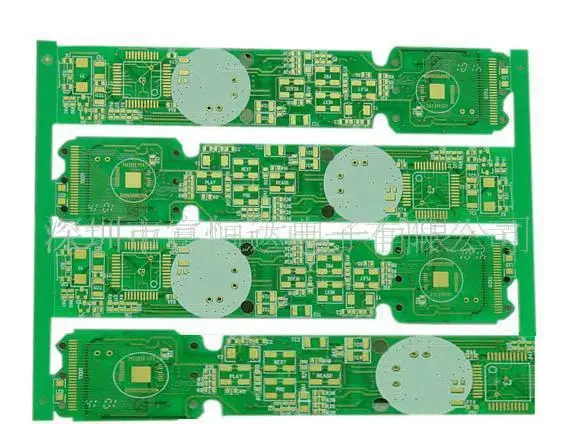
The etching process is one of the basic steps in the process. In a simple way, the base copper is covered by an anti-corrosive layer, and the copper not protected by the anti-corrosive layer reacts with the etchant, thus being bitten off, and finally forming the design circuit pattern and bonding pad. Of course, the etching principle can be easily described in a few words, but in fact, the implementation of the etching technology is still quite challenging, especially in the production of micro lines, there are very small line width tolerance requirements, and no errors are allowed in the etching process. Therefore, the etching results should be just right, and neither widening nor over etching is allowed.
Detailed analysis, principle and advantages of PCB vacuum etching technology
To further explain the etching process, PCB manufacturers are more willing to use horizontal etching lines for production to achieve maximum production automation and reduce production costs. However, horizontal etching is not perfect. The "pool effect" that cannot be eliminated causes different etching effects on the upper and lower surfaces of the board. The etching rate of the board edge is faster than that of the center of the board. Sometimes, This phenomenon will make a large difference in the etching results on the board.
That is to say, the "pool effect" will make the line erosion on the board edge larger than the line erosion on the center of the board. Even careful line correction (appropriately widening the line width on the board edge) will fail to compensate for different etching rates, because the etching tolerance must be controlled very carefully to obtain ultra-fine lines.
This situation leads to significant changes in the etching rate. For the part on the circuit board near the board edge, the etching solution is easier to flow out of the board, and the new and old etching solutions are easier to exchange, thus maintaining a good etching rate. In the center of the board, it is easy to form a "pool", so the flow of etchant is limited. It is relatively difficult for the solution rich in copper ions to flow out of the board. As a result, the etching efficiency is reduced and the etching effect is worse compared with the edge or the bottom of the board. In fact, it is unlikely to avoid the "pool effect" in practice, because the chain type horizontal drive roller will prevent the discharge of the etching solution, resulting in the accumulation of the etching solution between the rollers. This phenomenon is more obvious in the production of large plates or ultra-fine lines, even if more special production process control and compensation methods are used, such as the spray system Add oscillating spray pipes and corrective re etching sections. Without huge technical investment, this problem cannot be solved. Therefore, to achieve the goal of avoiding "pool effect", we do not have to go back to the starting point and start again.
At the end of last year, PILL e.K. released a new PCB process technology, which can improve the fluidity of the etching solution in the upper part of the board by only absorbing the used etching solution through the water pump, thus preventing the generation of the puddle effect. This method is called vacuum etching.
The first vacuum etching line was demonstrated to the public in Productronica in November 2001. At the same time, the tests conducted by the circuit board manufacturers also confirmed that the vacuum etching process can achieve excellent results only with less effort to control the engineering conditions.
After vacuum etching, the etching effect on both sides of the board is very uniform.
The principle of technology is very simple. In the etching section, not only the nozzle is installed, but also the air extraction unit is installed at the position where the nozzle is relatively close to the PCB surface. These pumping units suck the used etching solution and return it to the liquid tank of the module through a closed circuit.
Here, vacuum refers to the negative pressure in the operating area of the system and the low suction that is just enough to prevent the etching solution from producing a puddle effect. Even the thinnest inner laminates cannot be sucked up by the air extraction unit, and the production accuracy needs to be guaranteed. By connecting the track of the air exhauster with the upper fixed roller in the conveying system, the designer ensures that the distance between the air extraction process and the plate surface is the best value, no matter whether the plate is thin or thick, it can be processed. This point means that no matter what type of PCB, uniform etching solution extraction rate can be obtained. On the surface of the entire 24 "X24" large board, the upward side of the circuit board only found 1 micron copper thickness fluctuation. By comparison, the etching effect of the upper part and the lower part of the plate is basically the same.
The circuit quality of boards produced by vacuum etching technology is also very good. Detailed tests with different PCB manufacturers have shown that the new vacuum etching technology can produce a straighter conductor profile, so that the produced boards can more accurately meet the requirements of wiring.
In the vacuum etching process, the shrinkage of the side attack of the etching medium on the wire under the resist film and the value of the etching factor used to describe the etching depth and side etching amount of the wire are very high.
Of course, there are also a series of other factors that are basically not affected by the manufacturer that will affect the actual etching effect. For example, the thickness of the resist, the quality of the exposure and development process, and the copper thickness of the etched substrate each have a great impact. In general, it is estimated that the impact of the etching process or the renewal frequency of the etching solution on the etching effect is only half. However, Oliver Briel, the project manager of PILL, emphasized that "facts have proved that we let this 50% be completely controlled".
Vacuum etching technology also shows a series of advantages in other aspects:
The capacity of the etching process can be fully utilized. As the etching speed increases, the production time decreases, so the output of the etching process increases.
Because the first etching can achieve satisfactory results, there is no need to rework for re etching.
It can reduce the relevant PCB factory control engineering and reduce the corresponding cost.
The vacuum etching system uses a relatively simple technology to produce ultra-fine wires, eliminating the need to install oscillating injection manifolds.
The nozzle structure with intermittently adjustable injection pressure can no longer be used. This design is mainly used to ensure that the puddle effect is reduced, and now this function can be completed simply by using the suction system. The vacuum etching technology allows the process module to be shorter and tighter, and the suction and etching functions can be completed simultaneously in the same module.
The additional advantage of the vacuum etching technology system is that the injection manifold can be positioned laterally in the direction of travel. For the traditional injection manifold used to produce fine wire boards, the nozzle usually needs to be arranged longitudinally along the travel direction, so that there can be different injection pressures at the board edge and in the board. The angle between the nozzle and the travel direction is appropriate, which is convenient for maintenance and requires less time for replacement. Moreover, this arrangement method can also conduct simple flow electrical monitoring for each injection manifold separately. In case of any irregularity, the user can immediately identify which injection manifold is in trouble, and then can directly adjust it without delay.
Vacuum etching pcb technology has great potential in the future, because this process is particularly suitable for the production of thin wires and ultra-fine wire structural plates. Initial testing of conductive patterns below 50 microns can yield promising results. Now we are further evaluating the capability of using vacuum etching technology to produce thick copper circuit, and all the data at present show that the results are good. It is worth noting that not only the traditional copper chloride is used as the etching medium, but also the ferric chloride (III) commonly used in Asia is used as the etching medium. Although it takes a long time to use this etching medium, its effect is better when the conductor profile is steep, and it undoubtedly provides a substitute for the process that has been accepted as a standard at present, especially for the production of pcb for ultra-fine lines.a